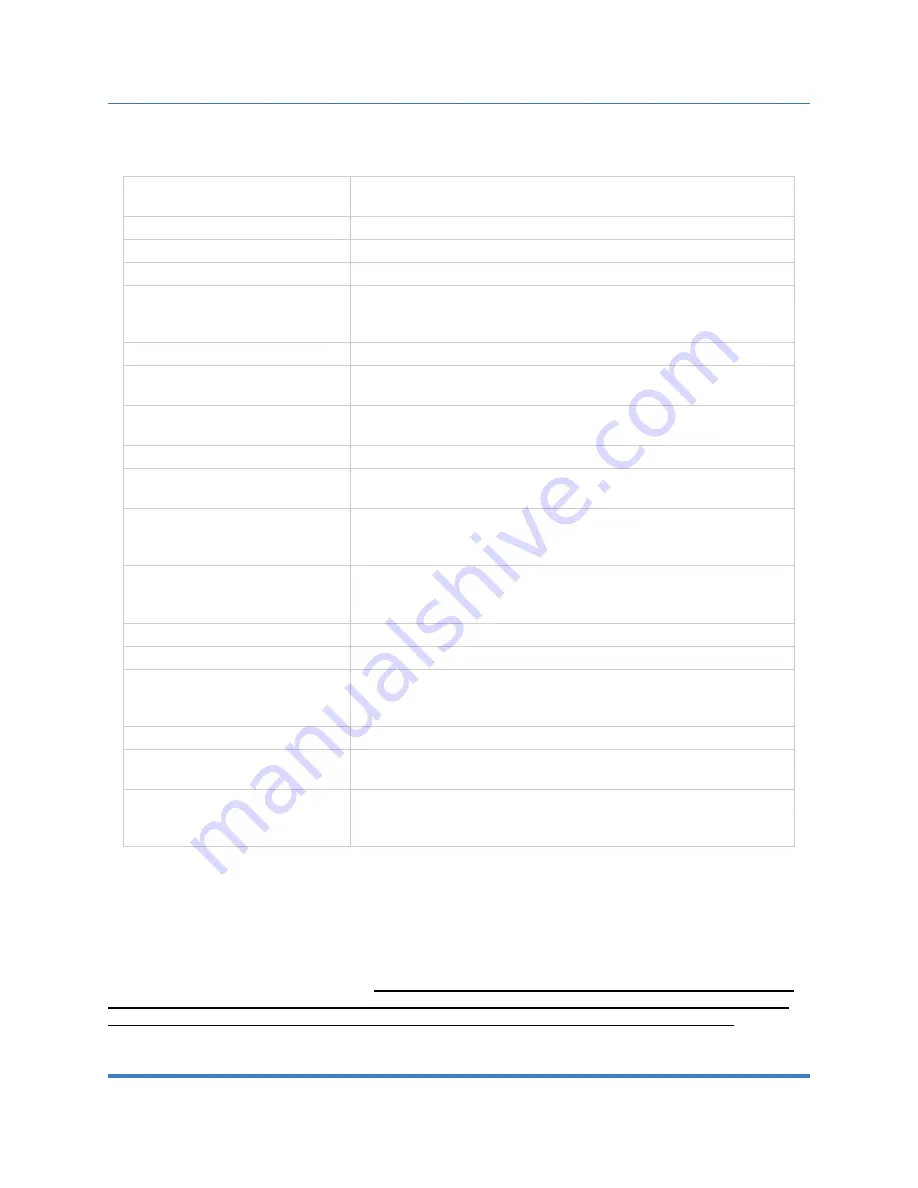
Brooks Automation
P/N: PFD0-DI-00010, Rev 5.0.0, April 9, 2022
Service Procedures
Copyright © 2022, Brooks Automation, Inc.
93
“Encoder Communication Error”
Check encoder connectors. Replace encoder cable or
motor/encoder.
"Encoder quadrature error"
Replace slip ring. Replace motor/encoder (only Gripper motor ).
"Missing zero index"
See "Encoder quadrature error"
“Motor duty cycle exceeded”
Reduce speed or acceleration of robot. Check for instability.
“Amplifier under voltage”
Motor power supply has reached current limit and
shutdown. Slow down robot. Check Energy Dump PCA. Replace
48V supply.
“Amplifier Fault”
Check harness and motor for shorts.
“Amplifier Over Voltage”
Check energy dump resistor is connected. Check harness for
shorts.
“Soft Envelope Error”
Make sure robot not pressing against surface. If this occurs on
the gripper repeatedly, replace slip ring.
“Hard Envelope Error”
Typically means robot has crashed into something.
Pneumatic Gripper Sensor not
working
Check continuity of cable through wrist. Check green lights on
sensor to see if sensor is triggering.
“Time Out Nulling Error”
Check that joint is free to move with brake off. Check that joint is
not vibrating or unstable. If unstable check belt tension. If
Gripper, check for free motion, if OK replace slip ring.
“Joint Out of Range”
The joint actual or commanded position may be beyond the
software limit stop. Move joint back into range while monitoring
virtual pendant or check program for commanded position.
“PAC Files Corrupted”
See recovering from corrupted PAC Files
Physical or audible problem
Brown streaks on linear bearing
Clean with alcohol and add grease to bearing blocks. This should
not be required sooner than 20,000 hours of run time. Grease is
Alvania Grease EP2 from Shell.
Mechanical noise from any joint Check joint bearings for failure. Re-tension belt.
Loud buzzing or vibration from
any joint
Re-tension timing belts. If timing belt will not hold tension, replace.
Squeaking from Z belt
Apply thick grease to front and rear edges of belt, (Mobile 222
XP). Belt can get stiff over time and squeak against pulley
flanges.
Encoder Operation Error
The PFDD robots are equipped with absolute encoders that keep track of the robot position even when
AC power to the robot is disconnected.
There are batteries in the back of the Z column of the robot
and outer link that provides standby power to the encoders for the Z axis and outer link motors.
J1 and J3 axes have single turn absolute encoders and do not require standby batteries
. In
standby mode, there is a limit on how quickly the motor can turn and still have the standby counter