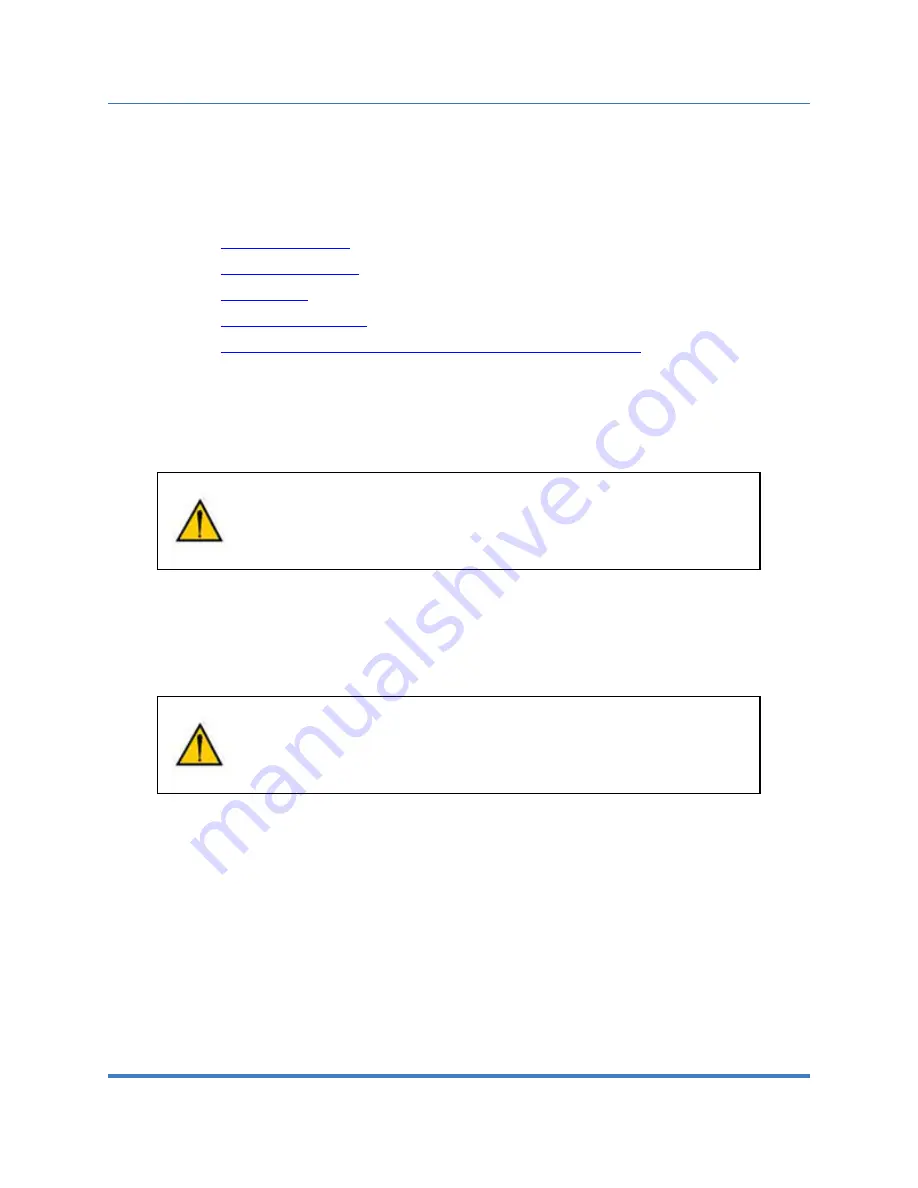
Hardware Reference
PreciseFlex™ DDR Collaborative Robots
P/N: PFD0-DI-00010, Rev 5.0.0, April 9, 2022
66
Copyright © 2022, Brooks Automation, Inc.
To simplify interfacing, most of the electrical interfaces provided by the robot's embedded PreciseFlex™
Controller are available on the Facilities Panel. These include:
•
•
•
•
•
RS-485, Belt Encoder, OSSD (Output Safety Switching Device)
Each of these interfaces is described in detail in the following sections. In addition, the robot's slave
controllers, which are mounted near the motors of the robot, may contain additional interfaces (e.g. inputs
or outputs). Please refer to the
PreciseFlex™
GSBP Controllers, Hardware Introduction and Reference
Manual
for additional information.
DANGER:
The 24 VDC and 48 VDC power supplies are all open frame
electrical devices that contain unshielded high voltage pins, components
and surfaces.
The main AC power should always be disconnected
before the Rear Z column cover is removed.
If the pneumatic gripper option is ordered two air lines are routed through the interior of the robot. At the
Facilities Panel, these air lines are presented in one-touch push-to-release fittings on the facilities
panel. The other end of these lines exit in the Outer Link. When using these lines, clean, dry external air
should be provided.
CAUTION:
The maximum air pressure that can be conveyed by the air
lines through the robot is
70 PSI
. Applying a pressure exceeding this level
may disconnect interior connections or damage fittings or hoses. If a higher
pressure is required, an external air line should be utilized.
E-Stop Connector
For users that wish to have a hardware E-Stop button, Precise offers an E-Stop Box or a portable
Hardware Manual Control Pendant that includes an E-Stop button. The E-Stop box can be plugged into
the 9 pin D-Sub connector in the connector panel in the base casting. The E-Stop box completes a circuit
from Pin 1 (Estop 1) to Pin 6 (FE Out 1) and from Pin 2 (Estop 2) to Pin 7 (FE Out2) in this connector. If
this circuit is not completed it is not possible to enable motor power to the robot. The FE Out signals
allow each Estop circuit to be toggled during the CAT3 startup sequence to make sure both circuits are
working. If no E-Stop box or Manual Control Pendant is connected, jumpers must be connected between
these four pins to enable robot motor power. For those applications where an operator must be inside the
working volume of the robot while teaching, a second teach pendant with a 3-position run hold switch is