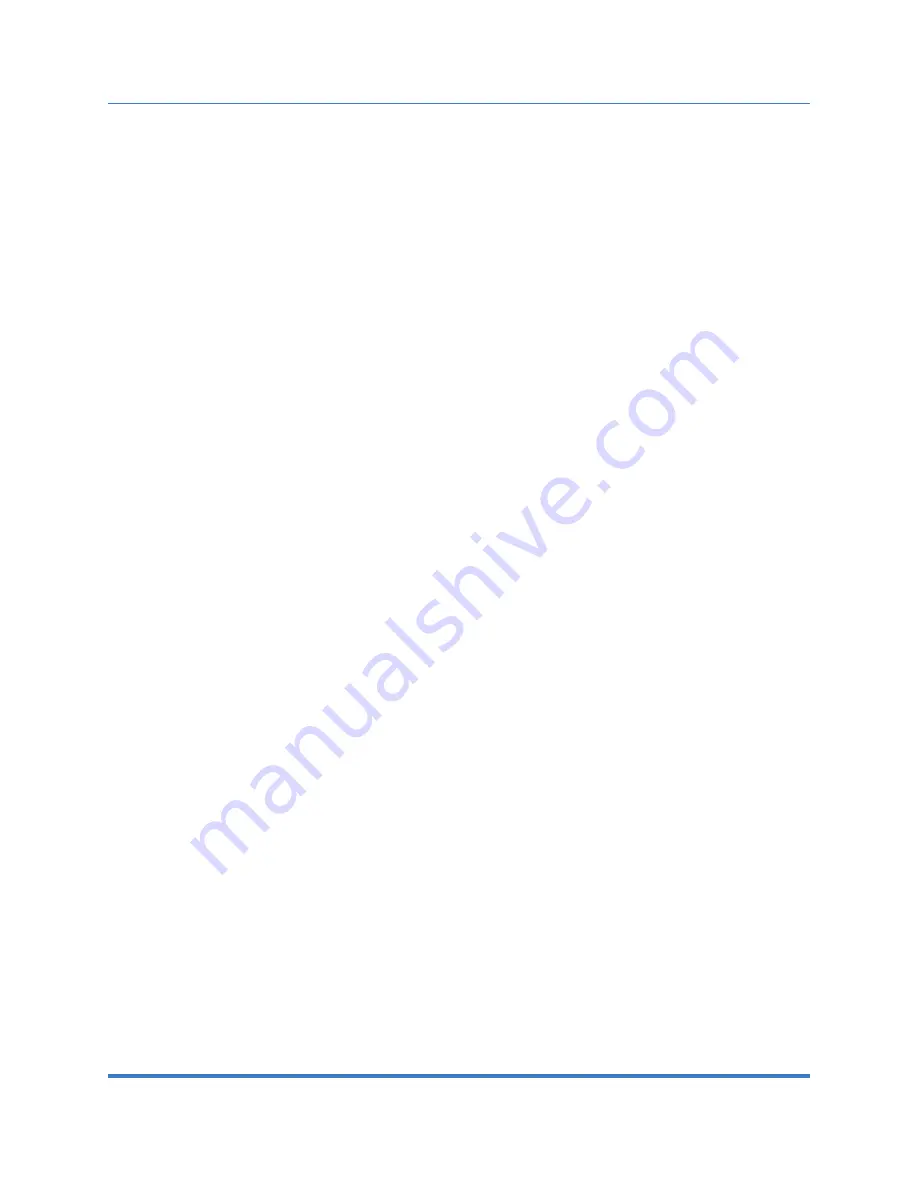
Brooks Automation
P/N: PFD0-DI-00010, Rev 5.0.0, April 9, 2022
Gripper Support
Copyright © 2022, Brooks Automation, Inc.
82
Gripper Support
Gripper Introduction
This section discusses adding grippers to the PFDD4 and PFDD6 robots. For the PFDD4, there is a
hollow output pulley in J4. For some electric grippers a slip ring is installed in this pulley. For other
grippers pneumatic tubes, or a high-flex wire pigtail can be routed up through this hollow pulley, which
allows all the gripper wiring to be kept inside the robot.
For the PFDD6, the 6
th
axis has a harmonic drive and motor installed, and there is not a wire path through
the axis. Therefore, all gripper wiring must go through an external service loop from the gripper into a
port on the J5 side cover. Since the gripper will rotate on J6, care should be taken to be sure the gripper
pigtail has enough length to wrap around J6 as it rotates, but is not so long that it catches on items in the
workcell. For some applications, helical coiled pneumatic tubing or even a helical coiled electrical pigtail
may be desirable.
For the PFDD4 at least one customer has requested the Precise 23N Micro-titer plate handing
gripper. This is a light duty gripper with 70mm of travel that is optimized to handle micro-titer plates for
laboratory automation applications. It is designed for very light payloads typically 500 grams or less. It is
controlled by a dedicated slave amplifier, the GSBP amp, which is connected through a slip ring in the J4
pulley.
Other commercial grippers can be attached to the PFDD4 and PFDD6 robots. These may be pneumatic
or electric grippers. They may be interfaced in several ways. For pneumatic grippers and DIO controlled
24VDC electric grippers, they may be controlled by the IO available on either the J4 or J6 slave
amplifier. See below for details.
The PFDD robots also have 100Mb Ethernet available for gripper control or camera interfacing. 24VDC
is available at the IO connector on the slave amplifiers.
Controlling the Precise Servo Grippers
Overview
The 23 Newton Precise Servo Gripper with spring return contains a brushless servo motor with an
incremental encoder with both counting and motor phase tracks. At power up the encoder provides motor
commutation information for a brief period, and then switches the incremental encoder A, B and Z signals
onto the same set of wires. This allows the motor commutation to be initialized at startup without any
motion.