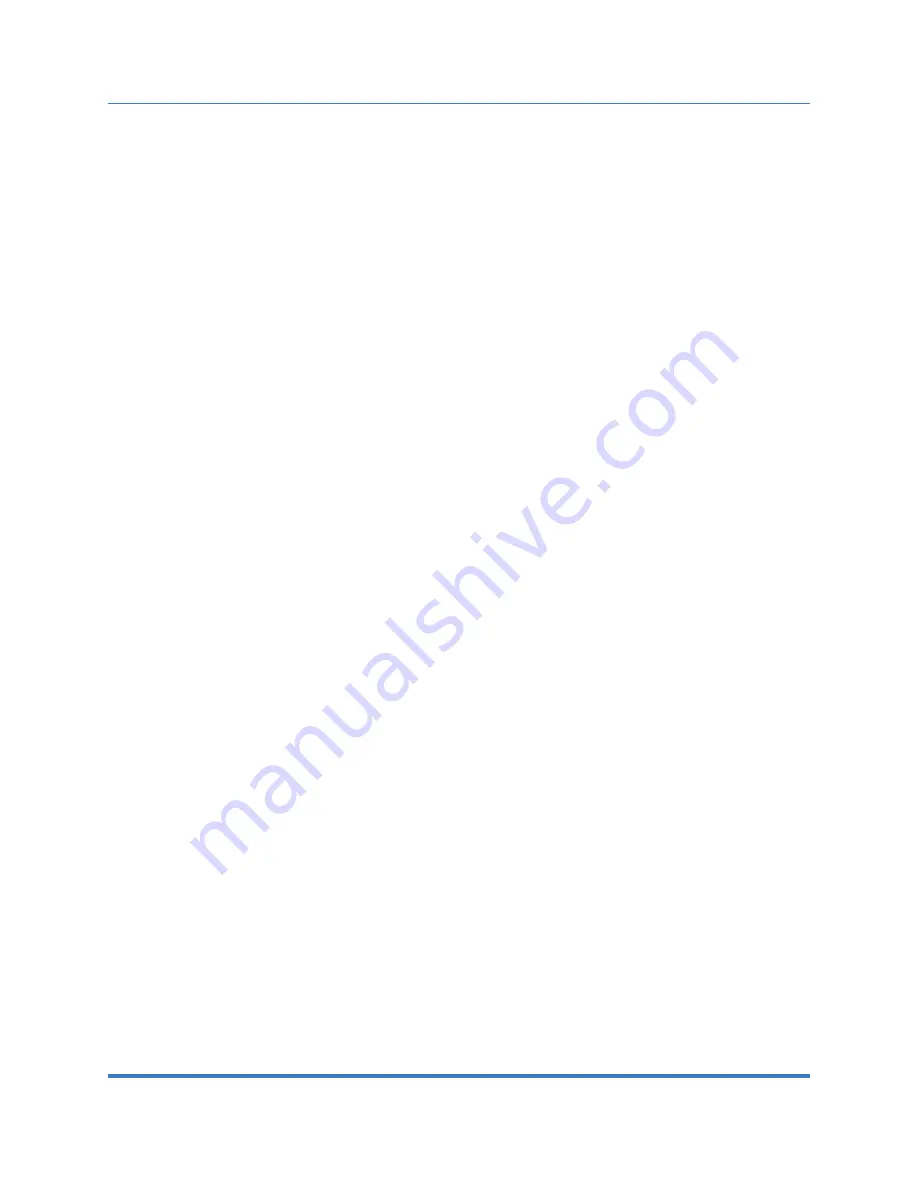
Introduction to the Hardware
PreciseFlex™ DDR Collaborative Robots
P/N: PFD0-DI-00010, Rev 5.0.0, April 9, 2022
14
Copyright © 2022, Brooks Automation, Inc.
For the PFDD4, the J4 axis is at the end of the outer link and is parallel to the J1 axis. A positive change
in the J4 axis angle results in a positive rotation about the World Z-axis.
The outer link may include a gripper controller that provides control of the optional electric gripper. It is
also possible to order the robot with a pneumatic gripper; in which case the outer link will house a
solenoid to control air to the pneumatic gripper. A light bar is mounted at the top of the elbow and blinks
at a rate of once per second to indicate that the controller is operational and at a rate of 4 times a second
when power is being supplied to the motors.
The Z-axis includes a fail-safe brake. This brake must be released to move the Z-axis up and down
manually. There is a manual brake release button on the bottom of the inner link near the Z-axis.
Depressing this button when 24VDC power is on will release the Z-axis brake while the button is
depressed. It is not necessary for the control system to be operating for the brake release to function; the
only requirement is providing 24VDC to the controller. Care should be taken to support the Z-axis when
the brake release button is pushed, as the axis will fall due to gravity.
System Diagram
Control System Overview
The PFDD Robots are controlled by a distributed control system (see below). The main control board
(PFD0) is located in the base casting behind the connector panel. This board contains various IO
functions, the main CPU, RAM and Flash memory, and the motor drive for the J1 motor. The 24VDC and
48VDC power supplies are located on the back of the Z column. A flexible ribbon cable is routed around
the robot to provide 24VDC, Gnd, 48VDC, Gnd, Ethernet, and RS485. Ethernet is routed to the outer link
and is available for certain gripper applications. A series of smart amplifiers (GSBP) are distributed
around the robot and located near each motor to minimize wiring through the robot. These are connected
by means of an RS485 network.