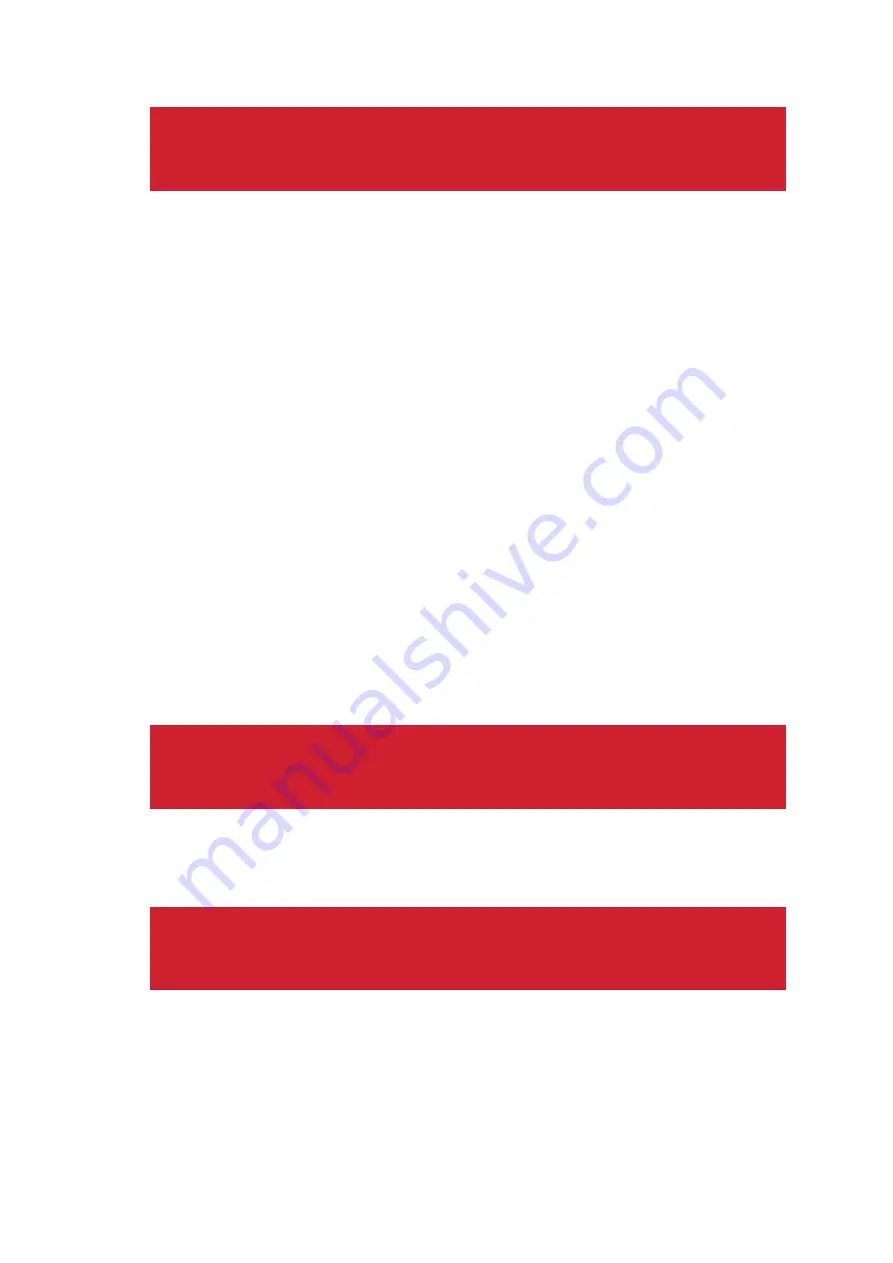
BOSS
TM
X-POT6+ Operation & Maintenance Manual
(V1.2 September 2017)
Page 7
tRAnsPoRtAtIon, stoRAGe,
unPACkInG
The equipment is delivered in packing units in conformity with contract specifications or
specifications required for certain transportation method and climate zone.
They meet the requirements of BSS’s packaging guidelines as a bare minimum. In
conformity with these guidelines, equipment is shipped horizontally, each unit packed on
disposable pallets. These pallets are suitable for horizontal transportation with approved
fork-lift trucks.
The forks must be set to the widest possible outer dimensions in order to prevent the
load from tipping over. When moving the equipment in question, the forks must be in the
lowest possible position, with the article at right angles to the forks. If the packages are
suitable for lifting gear, they will be marked at the appropriate lifting points.
Important note: Transport the packed goods as close as possible to the envisaged set-
up location and make sure there is a vertical, solid surface on which the goods can be
mounted / secured.
Caution:
Please take precautions to make sure the equipment, once it has been removed from the
pallet and the packaging, does not impact any other equipment or surface, tip over or
rock.
Once it has been removed from the pallet and the packaging, the equipment must be
transferred in a safe manner. Use methods that prevent uncontrolled falling, sliding or
tipping over.
The equipment may also be warehoused in their packaging. Once it has been removed
from its packaging, the equipment must be put in position, observing standard safety
procedures. Do not stack the equipment. Use only permitted lifting gear and safe tools,
and wear the required personal protective equipment.
emeRGenCy stoP /
emeRGenCy oFF
The in line with directive 2006/42/EC required EMERGENCY-STOP facility is made
available by the main power switch on the mounting board – Back Panel, refer to the
BOSS™ X-POT6+ Schematic, item 24 on page 10 of this document.
PeRsonAL PRoteCtIve eQuIPment
(PPe)
PPE must be used when carrying out potentially dangerous work and other activities, in
order to prevent or minimize the risk of personal injury if other measures cannot be taken.
These must comply with the requirements referred by the main contractor or operator of
the plant room or the site in question. If no requirements are set, to operate the equipment
minimum requirements are safety goggles, hand protection, well-fitting clothing and
sturdy, closed and skid-proof footwear.