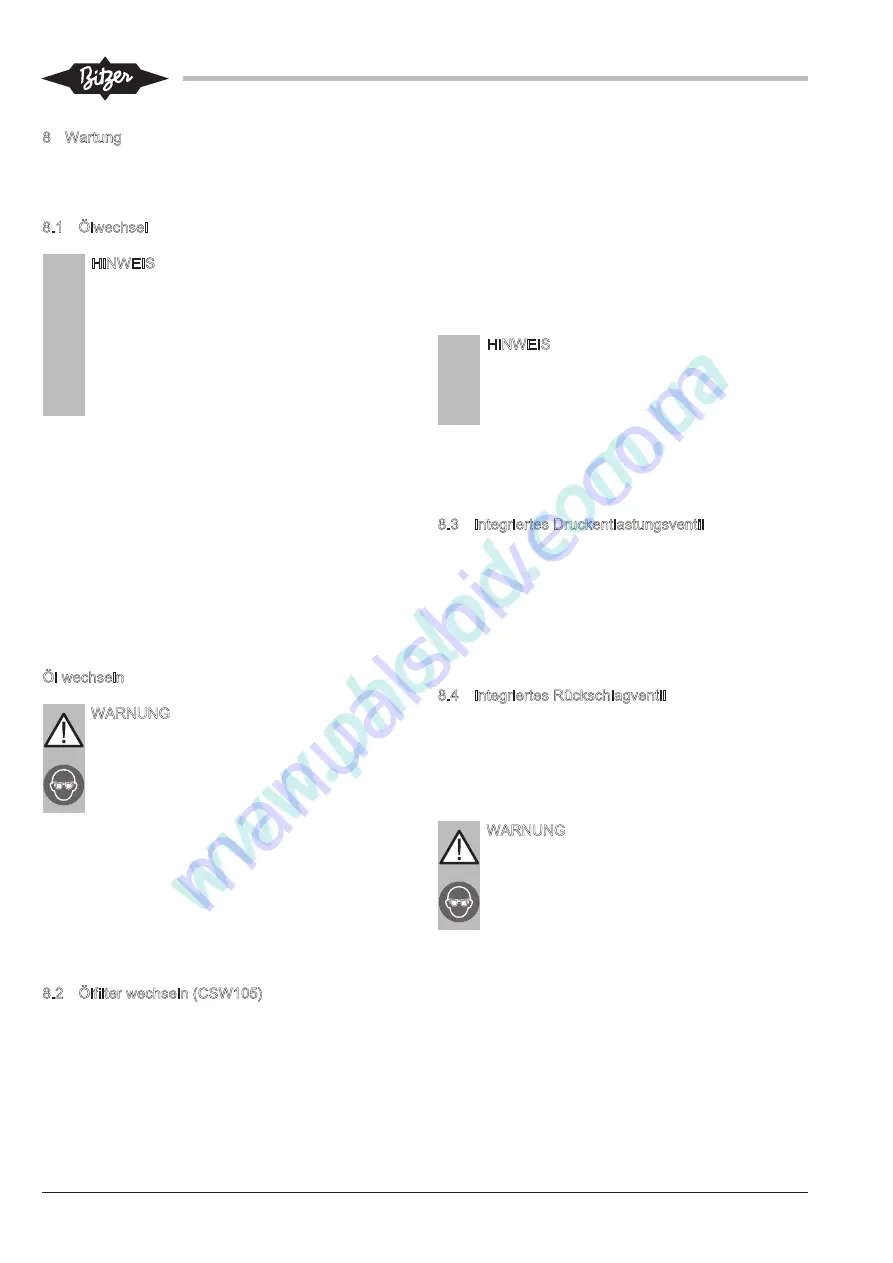
SB-170-9 RUS
64
SB-170-9
90
5.1 Raccordements réseau
Lors du dimensionnement des contacteurs du moteur,
des conduites d'amenée et des fusibles :
• Prendre en considération le courant de service maxi-
mal ou la puissance absorbée maximale du moteur.
• Choisir des contacteurs de la catégorie d'utilisation
AC3.
• Régler le relais thermique sur le courant de service
maximal du compresseur.
5.2 Versions moteur
!
!
AVIS
Risque de défaillance de compresseur !
N'utiliser le compresseur que dans le sens de
rotation prescrit !
Les séries de compresseurs CS.65, CS.75, CS.85,
CSH76 et CSH86 sont équipées de série de moteurs à
bobinage partiel (Part Winding, « PW ») avec
connexion Δ/ΔΔ. En option, elles peuvent également
être équipées de moteurs à étoile/triangle (Y/Δ). Pour
des informations détaillées, se reporter au manuel
SH-170.
Les modèles CS.95, CSH96 et CSW105 sont générale-
ment équipés de moteurs à étoile/triangle (Y/Δ).
Moteurs à bobinage partiel (PW)
Méthodes de démarrage :
• Démarrage à bobinage partiel pour réduire le cou-
rant de démarrage.
• Démarrage direct.
Retard de temps avant l’allumage du 2ème bobinage
partiel : 0,5 s max. !
Effectuer correctement les raccordements ! Une erreur
d’arrangement des raccords électriques aboutit à des
champs tournants contraires ou à l’angle de phase dé-
calé, et donc à un blocage du moteur !
Raccorder les bornes du moteur au couvercle de la
boîte de raccordement conformément aux instructions.
Tenir compte absolument de l’ordre des bobinages par-
tiels !
• 1er bobinage partiel (contacteur K1) : Raccords 1 /
2 / 3.
• 2ème bobinage partiel (contacteur K2) : Raccords 7 /
8 / 9.
• Partage de bobinage 50%/50%.
• Répartition des contacteurs moteur :
– 1er contacteur (PW 1) : 60% du courant de ser-
vice max.
– 2ème contacteur (PW 2) : 60% du courant de ser-
vice max.
Moteur à étoile-triangle
Le retard de temps entre la mise en route du compres-
seur d’un côté et, de l’autre, la commutation entre
l’opération en étoile et celle en triangle ne doit pas dé-
passer les 2 s.
Effectuer correctement les raccordements !
Toute erreur d’arrangement des raccords électriques
aboutit à un court-circuit !
Information
Les contacteurs réseau et triangles doivent être
calculés à au moins 60% du courant de service
max., le contacteur étoile à 33%.
5.3 Essai de haute tension (test de résistance
d'isolation)
Les compresseurs ont déjà été soumis avant leur sortie
d’usine à un essai de haute tension conformément à la
norme EN12693 ou conformément aux normes UL984
ou UL60335-2-34 pour la version UL.
!
!
AVIS
Risque d'endommagement de l'isolant et de dé-
faillance du moteur !
Il ne faut surtout pas répéter l'essai de haute
tension de la même manière !
Un nouvel essai de haute tension ne doit être réalisé
qu’à une tension alternative max. de 1000 V CA.
SB-170-9
64
8 Wartung
Herstellerdokumentation der eingesetzten Bauteile be-
achten!
8.1 Ölwechsel
!
!
HINWEIS
Verdichterschaden durch zersetztes Esteröl.
Feuchtigkeit wird im Esteröl chemisch gebun-
den und kann durch Evakuieren nicht entfernt
werden.
Äußerst sorgsamer Umgang erforderlich:
Lufteintritt in Anlage und Ölgebinde vermeiden.
Nur originalverschlossene Ölgebinde verwen-
den!
Die aufgeführten Öle, siehe Kapitel Anwendungsberei-
che, Seite 38, zeichnen sich durch einen besonders ho-
hen Grad an Stabilität aus. Bei ordnungsgemäßer Mon-
tage bzw. Einsatz von saugseitigen Feinfiltern erübrigt
sich deshalb im Regelfall ein Ölwechsel. Bei Verdich-
ter- oder Motorschaden generell Säuretest durchfüh-
ren. Bei Bedarf Reinigungsmaßnahmen treffen: Säure-
bindenden Saugleitungsfilter (bi-direktional) einbauen
und Öl wechseln. Anlage druckseitig an der höchsten
Stelle in Recyclingbehälter entlüften. Nach einigen Be-
triebsstunden ggf. Filter und Öl erneut wechseln sowie
Anlage entlüften.
Öl wechseln
WARNUNG
Verdichter steht unter Druck!
Schwere Verletzungen möglich.
Verdichter auf drucklosen Zustand bringen!
Schutzbrille tragen!
• Das Öl aus Verdichter- und Motorgehäuse ablassen.
Ölablasspositionen am Verdichter sind die An-
schlusspositionen 5 und 6, siehe Kapitel Anschlüsse
und Maßzeichnungen, Seite 47.
• Neues Öl einfüllen.
• Altöl umweltgerecht entsorgen.
8.2 Ölfilter wechseln (CSW105)
➙ Neuen Ölfilter bereitlegen.
• Flache Wanne unter dem Ölventil für die Wartung (5)
und dem Ölfilterflansch (18) platzieren.
• Öl ablassen und umweltgerecht entsorgen.
• Ölfilterflansch öffnen und nach vorne abziehen.
Der integrierte Ölfilter ist auf der Rückseite des Flan-
sches montiert.
• Ölfilter vom Flansch abschrauben.
• Neuen Ölfilter auf den Flansch montieren.
• O-Ring am Flansch austauschen.
• Flansch mit neuem Ölfilter, neuer Flachdichtung und
neuem O-Ring wieder einbauen.
!
!
HINWEIS
Beschädigungen des Verdichters möglich.
Schrauben und Muttern nur mit vorgeschriebe-
nem Anzugsmoment und wo möglich, über
Kreuz in mindestens 2 Schritten anziehen.
• Neues Öl einfüllen.
• Vor Inbetriebnahme Dichtheit prüfen.
8.3 Integriertes Druckentlastungsventil
Das Ventil ist wartungsfrei. Es hat eine Ansprechdruck-
differenz von 28 bar.
Allerdings kann es nach wiederholtem Abblasen auf
Grund abnormaler Betriebsbedingungen zu permanen-
ter Leckage kommen. Folgen sind Minderleistung und
erhöhte Druckgastemperatur.
8.4 Integriertes Rückschlagventil
Nach dem Abschalten läuft der Verdichter kurzzeitig
rückwärts (ca. 5 s, bis zum Druckausgleich im Ölab-
scheider). Bei Defekt oder Verschmutzung des Rück-
schlagventils verlängert sich dieser Zeitraum. Dann
muss das Ventil ausgetauscht werden.
WARNUNG
Verdichter steht unter Druck!
Schwere Verletzungen möglich.
Verdichter auf drucklosen Zustand bringen!
Schutzbrille tragen!
Einbauposition: im Druckgasaustritt unterhalb des
Druckabsperrventils oder Rohranschlusses. Austausch
siehe Wartungsanleitung SW-170.