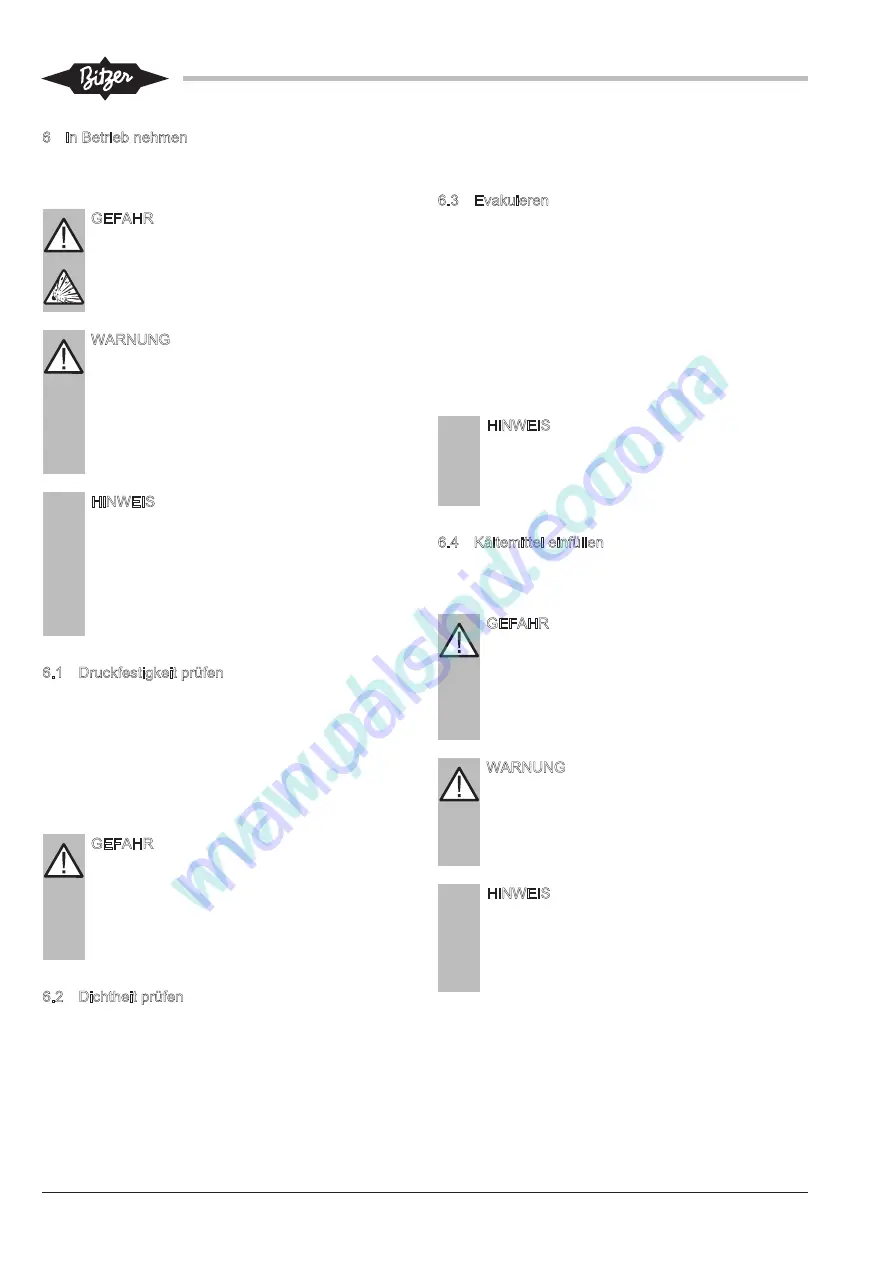
SB-170-9 RUS
60
SB-170-9
90
5.1 Raccordements réseau
Lors du dimensionnement des contacteurs du moteur,
des conduites d'amenée et des fusibles :
• Prendre en considération le courant de service maxi-
mal ou la puissance absorbée maximale du moteur.
• Choisir des contacteurs de la catégorie d'utilisation
AC3.
• Régler le relais thermique sur le courant de service
maximal du compresseur.
5.2 Versions moteur
!
!
AVIS
Risque de défaillance de compresseur !
N'utiliser le compresseur que dans le sens de
rotation prescrit !
Les séries de compresseurs CS.65, CS.75, CS.85,
CSH76 et CSH86 sont équipées de série de moteurs à
bobinage partiel (Part Winding, « PW ») avec
connexion Δ/ΔΔ. En option, elles peuvent également
être équipées de moteurs à étoile/triangle (Y/Δ). Pour
des informations détaillées, se reporter au manuel
SH-170.
Les modèles CS.95, CSH96 et CSW105 sont générale-
ment équipés de moteurs à étoile/triangle (Y/Δ).
Moteurs à bobinage partiel (PW)
Méthodes de démarrage :
• Démarrage à bobinage partiel pour réduire le cou-
rant de démarrage.
• Démarrage direct.
Retard de temps avant l’allumage du 2ème bobinage
partiel : 0,5 s max. !
Effectuer correctement les raccordements ! Une erreur
d’arrangement des raccords électriques aboutit à des
champs tournants contraires ou à l’angle de phase dé-
calé, et donc à un blocage du moteur !
Raccorder les bornes du moteur au couvercle de la
boîte de raccordement conformément aux instructions.
Tenir compte absolument de l’ordre des bobinages par-
tiels !
• 1er bobinage partiel (contacteur K1) : Raccords 1 /
2 / 3.
• 2ème bobinage partiel (contacteur K2) : Raccords 7 /
8 / 9.
• Partage de bobinage 50%/50%.
• Répartition des contacteurs moteur :
– 1er contacteur (PW 1) : 60% du courant de ser-
vice max.
– 2ème contacteur (PW 2) : 60% du courant de ser-
vice max.
Moteur à étoile-triangle
Le retard de temps entre la mise en route du compres-
seur d’un côté et, de l’autre, la commutation entre
l’opération en étoile et celle en triangle ne doit pas dé-
passer les 2 s.
Effectuer correctement les raccordements !
Toute erreur d’arrangement des raccords électriques
aboutit à un court-circuit !
Information
Les contacteurs réseau et triangles doivent être
calculés à au moins 60% du courant de service
max., le contacteur étoile à 33%.
5.3 Essai de haute tension (test de résistance
d'isolation)
Les compresseurs ont déjà été soumis avant leur sortie
d’usine à un essai de haute tension conformément à la
norme EN12693 ou conformément aux normes UL984
ou UL60335-2-34 pour la version UL.
!
!
AVIS
Risque d'endommagement de l'isolant et de dé-
faillance du moteur !
Il ne faut surtout pas répéter l'essai de haute
tension de la même manière !
Un nouvel essai de haute tension ne doit être réalisé
qu’à une tension alternative max. de 1000 V CA.
SB-170-9
60
6 In Betrieb nehmen
Der Verdichter ist ab Werk sorgfältig getrocknet, auf
Dichtheit geprüft und mit Schutzgas (N
2
) befüllt.
GEFAHR
Explosionsgefahr!
Verdichter keinesfalls mit Sauerstoff (O
2
) oder
anderen technischen Gasen abpressen!
WARNUNG
Berstgefahr!
Kritische Verschiebung der Kältemittelzündgren-
ze bei Überdruck möglich!
Dem Prüfmedium (N
2
oder Luft) kein Kältemittel
beimischen (z. B. als Leckindikator).
Umweltbelastung bei Leckage und beim Abbla-
sen!
!
!
HINWEIS
Gefahr von Öloxidation!
Druckfestigkeit und Dichtheit der gesamten An-
lage bevorzugt mit getrocknetem Stickstoff (N
2
)
prüfen.
Bei Verwendung von getrockneter Luft: Verdich-
ter aus dem Kreislauf nehmen – Absperrventile
unbedingt geschlossen halten.
6.1 Druckfestigkeit prüfen
Kältekreislauf (Baugruppe) entsprechend EN378-2 prü-
fen (oder gültigen äquivalenten Sicherheitsnormen).
Der Verdichter wurde bereits im Werk einer Prüfung auf
Druckfestigkeit unterzogen. Eine Dichtheitsprüfung ist
deshalb ausreichend, siehe Kapitel Dichtheit prüfen,
Seite 60. Wenn dennoch die gesamte Baugruppe auf
Druckfestigkeit geprüft wird:
GEFAHR
Berstgefahr durch zu hohen Druck!
Prüfdruck darf die maximal zulässigen Drücke
nicht überschreiten!
Prüfdruck: 1,1-facher Druck des maximal zuläs-
sigen Betriebsdrucks (siehe Typschild). Dabei
Hoch- und Niederdruckseite unterscheiden!
6.2 Dichtheit prüfen
Kältekreislauf (Baugruppe) als Ganzes oder in Teilen
auf Dichtheit prüfen – entsprechend EN378-2 (oder gül-
tigen äquivalenten Sicherheitsnormen). Dazu vorzugs-
weise mit getrocknetem Stickstoff einen Überdruck er-
zeugen.
Prüfdrücke und Sicherheitshinweis beachten, siehe Ka-
pitel Druckfestigkeit prüfen, Seite 60.
6.3 Evakuieren
• Ölheizung einschalten.
• Vorhandene Absperr- und Magnetventile öffnen.
• Die gesamte Anlage einschließlich Verdichter auf
Saug- und Hochdruckseite mit Vakuumpumpe eva-
kuieren.
Bei abgesperrter Pumpenleistung muss ein "stehen-
des Vakuum" kleiner als 1,5 mbar erreicht werden.
• Wenn nötig Vorgang mehrfach wiederholen.
!
!
HINWEIS
Gefahr von Motor- und Verdichterschaden!
Verdichter nicht im Vakuum anlaufen lassen!
Keine Spannung anlegen, auch nicht zum Prü-
fen!
6.4 Kältemittel einfüllen
Nur zulässige Kältemittel einfüllen, siehe siehe Kapitel
Anwendungsbereiche, Seite 38.
GEFAHR
Berstgefahr von Bauteilen und Rohrleitungen
durch hydraulischen Überdruck bei Flüssig-
keitseinspeisung.
Schwere Verletzungen möglich.
Überfüllung der Anlage mit Kältemittel unbe-
dingt vermeiden!
WARNUNG
Berstgefahr des Verdichters durch gefälschte
Kältemittel!
Schwere Verletzungen möglich!
Kältemittel nur von renommierten Herstellern
und seriösen Vertriebspartnern beziehen!
!
!
HINWEIS
Gefahr von Nassbetrieb bei Flüssigkeitseinspei-
sung!
Äußerst fein dosieren!
Druckgastemperatur mindestens 20 K über Ver-
flüssigungstemperatur halten.
➙ Bevor Kältemittel eingefüllt wird:
➙ Verdichter nicht einschalten!
➙ Ölheizung einschalten.
➙ Ölniveau im Verdichter prüfen.