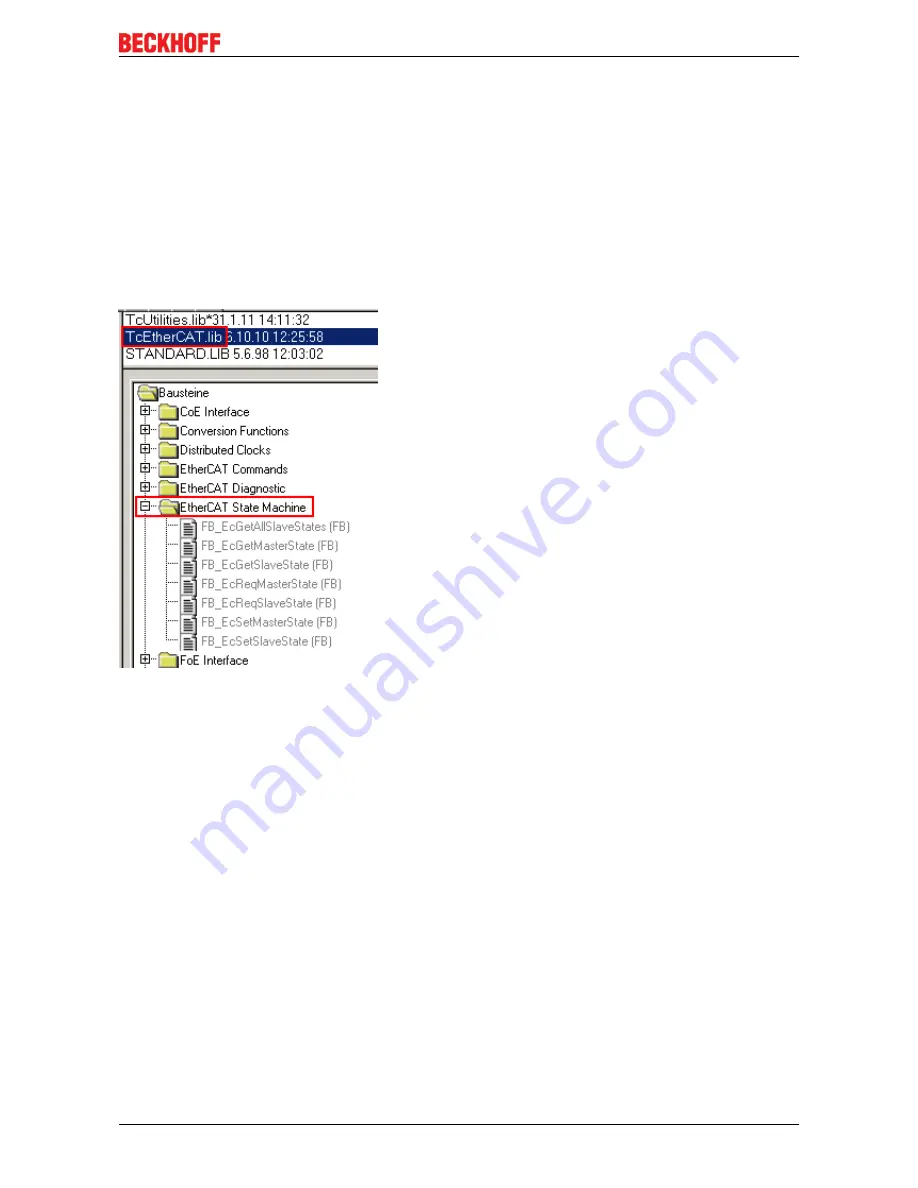
Commissioning
EL3692
101
Version: 2.1
Manual Control
There are particular reasons why it may be appropriate to control the states from the application/task/PLC.
For instance:
• for diagnostic reasons
• to induce a controlled restart of axes
• because a change in the times involved in starting is desirable
In that case it is appropriate in the PLC application to use the PLC function blocks from the
TcEtherCAT.lib
,
which is available as standard, and to work through the states in a controlled manner using, for instance,
FB_EcSetMasterState
.
It is then useful to put the settings in the EtherCAT Master to INIT for master and slave.
Fig. 132: PLC function blocks
Note regarding E-Bus current
EL/ES terminals are placed on the DIN rail at a coupler on the terminal strand. A Bus Coupler can supply the
EL terminals added to it with the E-bus system voltage of 5 V; a coupler is thereby loadable up to 2 A as a
rule. Information on how much current each EL terminal requires from the E-bus supply is available online
and in the catalogue. If the added terminals require more current than the coupler can supply, then power
feed terminals (e.g. EL9410) must be inserted at appropriate places in the terminal strand.
The pre-calculated theoretical maximum E-Bus current is displayed in the TwinCAT System Manager as a
column value. A shortfall is marked by a negative total amount and an exclamation mark; a power feed
terminal is to be placed before such a position.