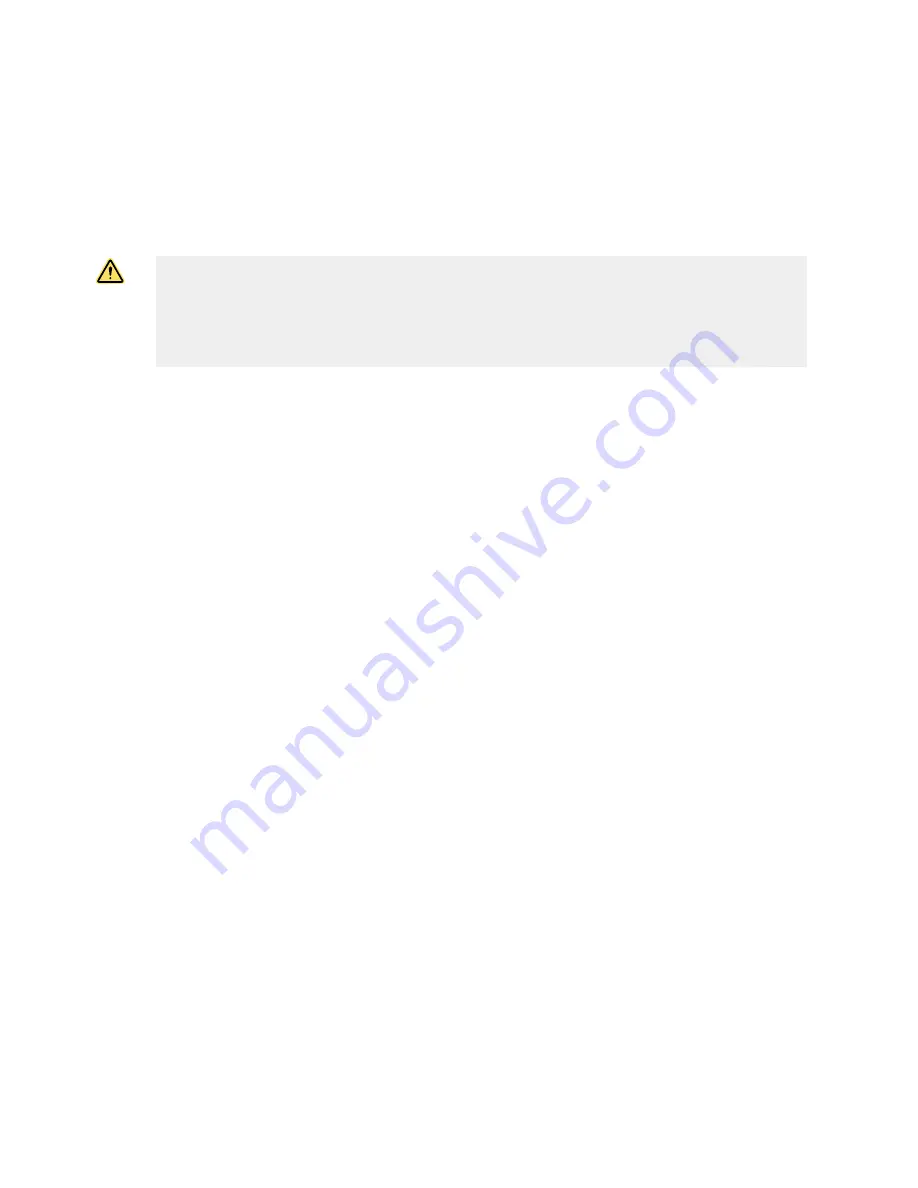
Additional Safety Outputs can be added to expandable models of the Base Controller by incorporating I/O modules. These
additional safety outputs can be isolated relay outputs that can be used to control/switch a wide range of power
SC10-2
on page 18 for rating and derating considerations.
XS/SC26-2
and
SC10-2
WARNING: Safety Outputs must be connected to the machine control so that the machine’s safety-
related control system interrupts the circuit to the machine primary control element(s), resulting in a non-
hazardous condition.
Do not wire an intermediate device(s), such as a PLC, PES, or PC, that can fail in such a manner that
there is the loss of the safety stop command, or that the safety function can be suspended, overridden,
or defeated, unless accomplished with the same or greater degree of safety.
The following list describes additional nodes and attributes that can be configured from the Safety Output function block
Properties window (see
Adding Inputs and Status Outputs
on page 62):
EDM (External Device Monitoring)
Enables the Safety Controller to monitor devices under control (FSDs and MPCEs) for proper response to the
stopping command of the safety outputs. It is strongly recommended to incorporate EDM (or AVM) in the machine
design and the Safety Controller configuration to ensure the proper level of safety circuit integrity (see
AVM (Adjustable Valve Monitoring)
Enables the Safety Controller to monitor valves or other devices that may become slow, stick, or fail in an energized
state or position and whose operation needs to be verified after a Stop signal occurs. Up to three AVM inputs can
be selected if EDM is not used. It is strongly recommended to incorporate AVM (or EDM) in the machine design and
the Safety Controller configuration to ensure the proper level of safety circuit integrity (see
LR (Latch Reset)
Keeps the SO or RO output Off until the input changes to the Run state and a manual reset operation is performed
on page 42 for more information.
RE (Reset Enable)
This option appears only if LR (Latch Reset) is enabled. The Latch Reset can be controlled by selecting Reset
Enable to restrict when the Safety Output can be reset to a Run condition.
FR (Fault Reset)
Provides a manual reset function when input faults occur. The FR node needs to be connected to a Manual Reset
button or signal. This function is used to keep the SO or RO output Off until the Input device fault is cleared, the
faulted device is in the Run state , and a manual reset operation is performed. This replaces power down/up cycle
reset operation. See
on page 42 for more information.
Power up mode
The Safety Output can be configured for three power-up scenarios (operational characteristics when power is
applied):
• Normal Power-Up Mode (default)
• Manual Power-up Mode
• Automatic Power-Up Mode
on page 42 for more information.
Split (Safety Outputs)—XS/SC26-2 only
This option is only available for Solid-State Safety Outputs. Each redundant Solid-State Safety Output can be
configured to function individually or in pairs (default). Splitting a solid-state safety output creates two independent
single channel outputs (control of SO1a is independent of SO1b). To combine a split safety output, open the
Mx:SOxA Properties window and click Join.
XS/SC26-2 and SC10-2 Safety Controllers
www.bannerengineering.com - Tel: + 1 888 373 6767
47