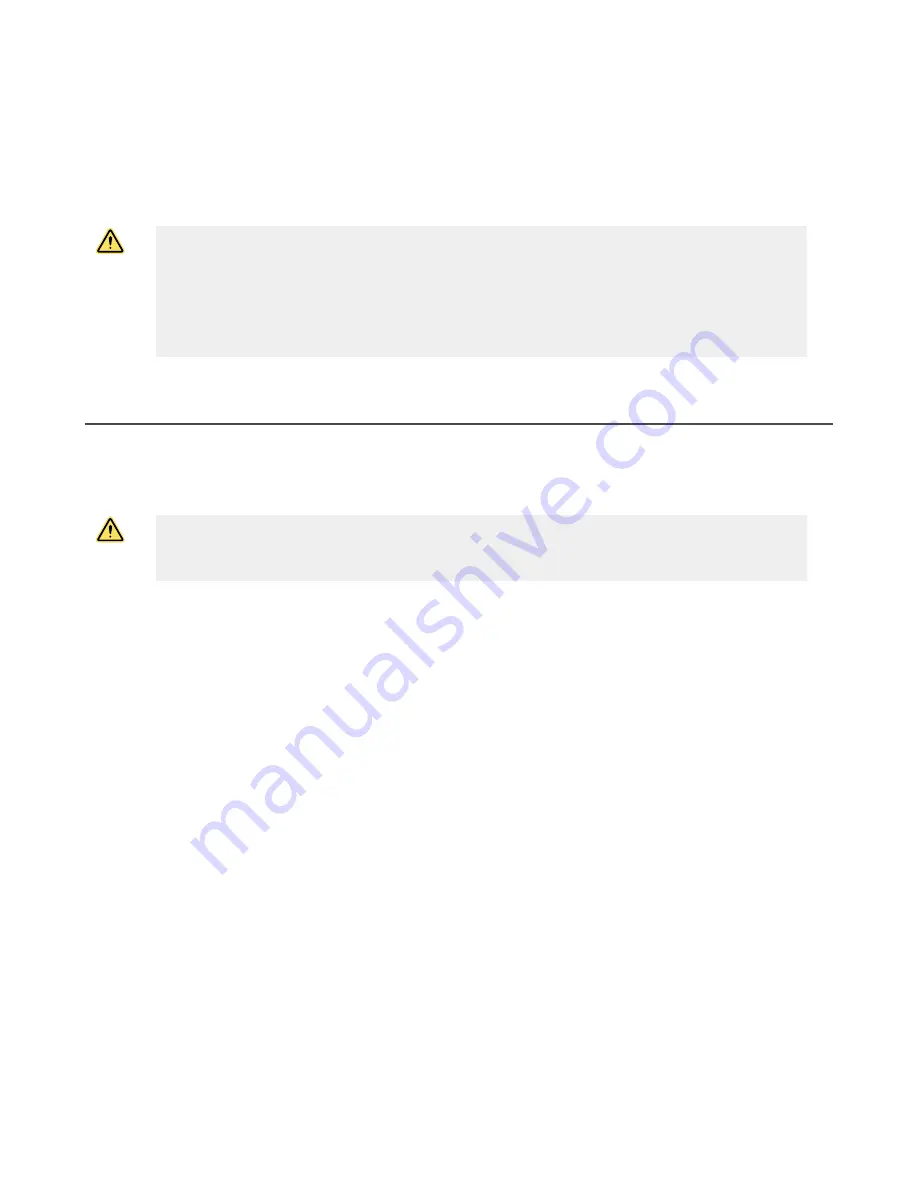
The Adjustable Valve (Device) Monitoring function is useful for dynamically monitoring devices under the control of the
safety output that may become slow, stick, or fail in an energized state or position, and whose operation needs to be
verified after a Stop signal occurs. Example applications include single- or dual-solenoid valves controlling clutch/brake
mechanisms, and position sensors that monitor the home position of a linear actuator.
Synchronization or checking a maximum differential timing between two or more devices, such as dual valves, may be
achieved by mapping multiple AVM functions to one safety output and configuring the AVM timer to the same values. Any
number of AVM inputs can be mapped to one safety output. An input signal can be generated by a hard/relay contact or a
solid-state PNP output.
WARNING:
• Adjustable Valve Monitoring (AVM) Operation
• When the AVM function is used, the Safety Output(s) will not turn ON until the AVM input is
satisfied. This could result in an ON-delay up to the configured AVM monitoring time.
• It is the user's responsibility to ensure the AVM monitoring time is properly configured for the
application and to instruct all individuals associated with the machine about the possibility of the
ON-Delay effect, which may not be readily apparent to the machine operator or to other
personnel.
7.6 Non-Safety Input Devices
The non-safety input devices include manual reset devices, On/Off switches, mute enable devices, and cancel delay inputs.
Manual Reset Devices—Used to create a reset signal for an output or function block configured for a manual reset,
requiring an operator action for the output of that block to turn on. Resets can also be created using virtual reset input; see
Virtual Non-Safety Input Devices (XS/SC26-2 FID 2 Only and SC10-2)
on page 44.
WARNING: Non-Monitored Resets
If a non-monitored reset (either latch or system reset) is configured and if all other conditions for a reset
are in place, a short from the Reset terminal to +24 V will turn On the safety output(s) immediately.
ON/Off Switch—Provides an On or Off command to the machine. When all of the controlling safety inputs are in the Run
state, this function permits the safety output to turn On and Off. This is a single-channel signal; the Run state is 24 V dc and
the Stop state is 0 V dc. An On/Off input can be added without mapping to a safety output, which allows this input to
control only a status output. An On/Off switch can also be created using a virtual input; see
Devices (XS/SC26-2 FID 2 Only and SC10-2)
Mute Enable Switch—Signals the Safety Controller when the mute sensors are permitted to perform a mute function. When
the mute enable function is configured, the mute sensors are not enabled to perform a mute function until the mute enable
signal is in the Run state. This is a single-channel signal; the enable (Run) state is 24 V dc and the disable (Stop) state is 0 V
dc. A mute enable switch can also be created using a virtual input; see
Virtual Non-Safety Input Devices (XS/SC26-2 FID 2
Cancel Off-Delay Devices—Provide the option to cancel a configured Off-delay time of a safety output or a delay block
output. It functions in one of the following ways:
• Keeps the safety output or delay block output On
• Turns the safety output or delay block output Off immediately after the Safety Controller receives a Cancel Off-Delay
signal
• When Cancel Type is set to "Control Input", the safety output or delay block output stays on if the input turns On
again before the end of the delay
A status output function (Output Delay in Progress) indicates when a Cancel Delay Input can be activated in order to keep
the Off-delayed safety output On. A cancel off-delay device can also be created using a virtual input; see
Input Devices (XS/SC26-2 FID 2 Only and SC10-2)
on page 44.
XS/SC26-2 and SC10-2 Safety Controllers
www.bannerengineering.com - Tel: + 1 888 373 6767
41