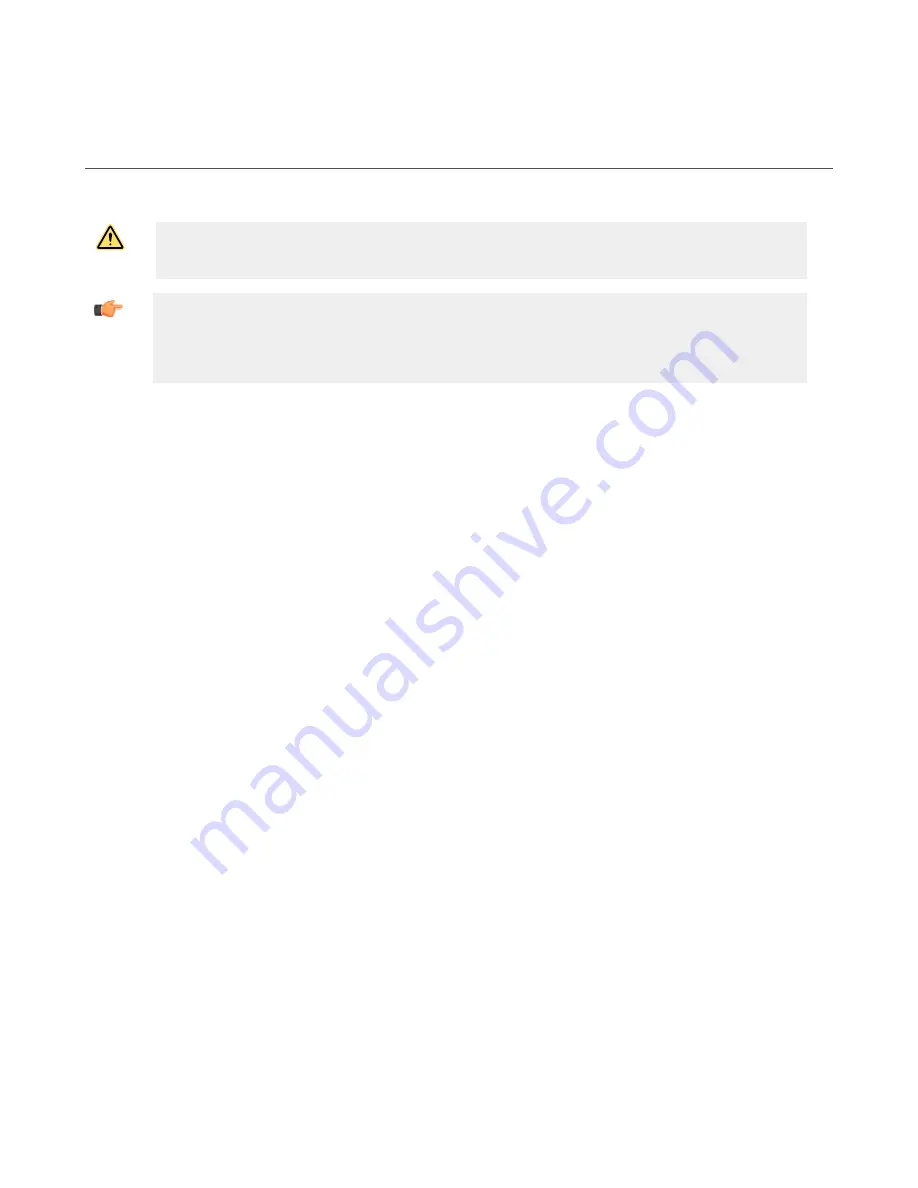
7.7 Virtual Non-Safety Input Devices (
XS/SC26-2
FID 2 Only
and
SC10-2
)
All virtual inputs require FID 2 for XS/SC26-2. The virtual non-safety input devices include manual reset, On/Off, mute
enable, and cancel off delay.
WARNING: Virtual Non-Safety Inputs must never be used to control any safety-critical applications. If a
Virtual Non-Safety Input is used to control a safety-critical application, a failure to danger is possible and
may lead to serious injury or death.
Important: Resetting a safeguard must not initiate hazardous motion. Safe work procedures require a
start-up procedure to be followed and the individual performing the reset to verify that the entire
hazardous area is clear of all personnel before each reset of the safeguard is performed. If any area
cannot be observed from the reset switch location, additional supplemental safeguarding must be used:
at a minimum, visual and audible warnings of the machine start-up.
7.7.1 Virtual Manual Reset and Cancel Delay (RCD) Sequence
According to section 5.2.2 of EN ISO 13849-1:2015, a "deliberate action" by the operator is required to reset a safety
function. Traditionally, this requirement is met by using a mechanical switch and associated wires connected to specified
terminals on the Safety Controller. For a monitored reset, the contacts must be open initially, then closed, and then open
again within the proper timing. If the timing is not too short or too long, it is determined to be deliberate and the reset is
performed.
Banner has created a virtual reset solution that requires deliberate action. For example, in place of the mechanical switch,
an HMI may be used. In place of the wires, a unique Actuation Code is used for each Safety Controller on a network. Also,
each virtual reset within a Safety Controller is associated with a specific bit in a register. This bit, along with the Actuation
Code, must be written and cleared in a coordinated way. If the steps are completed with the proper sequence and timing, it
is determined to be deliberate and the reset is performed.
While the standards do not require a "deliberate action" to perform a virtual cancel delay, to avoid additional complexity,
Banner has implemented this function in the same way as the virtual manual reset.
The user must set matching Actuation Codes in both the Safety Controller and the controlling network device (PLC, HMI,
etc.). The Actuation Code is part of the Network Settings and is not included in the configuration CRC. There is no default
Actuation Code. The user must set one up on the Network Settings screen. The Actuation Code can be active for up to 2
seconds for it to be effective. Different Safety Controllers on the same network should have different Actuation Codes.
The HMI/PLC programmer can choose from two different methods depending on their preferences; a feedback-based
sequence or a timed sequence. These methods are described in the following figures. The actual register location depends
upon which protocol is being used.
XS/SC26-2 and SC10-2 Safety Controllers
44
www.bannerengineering.com - Tel: + 1 888 373 6767