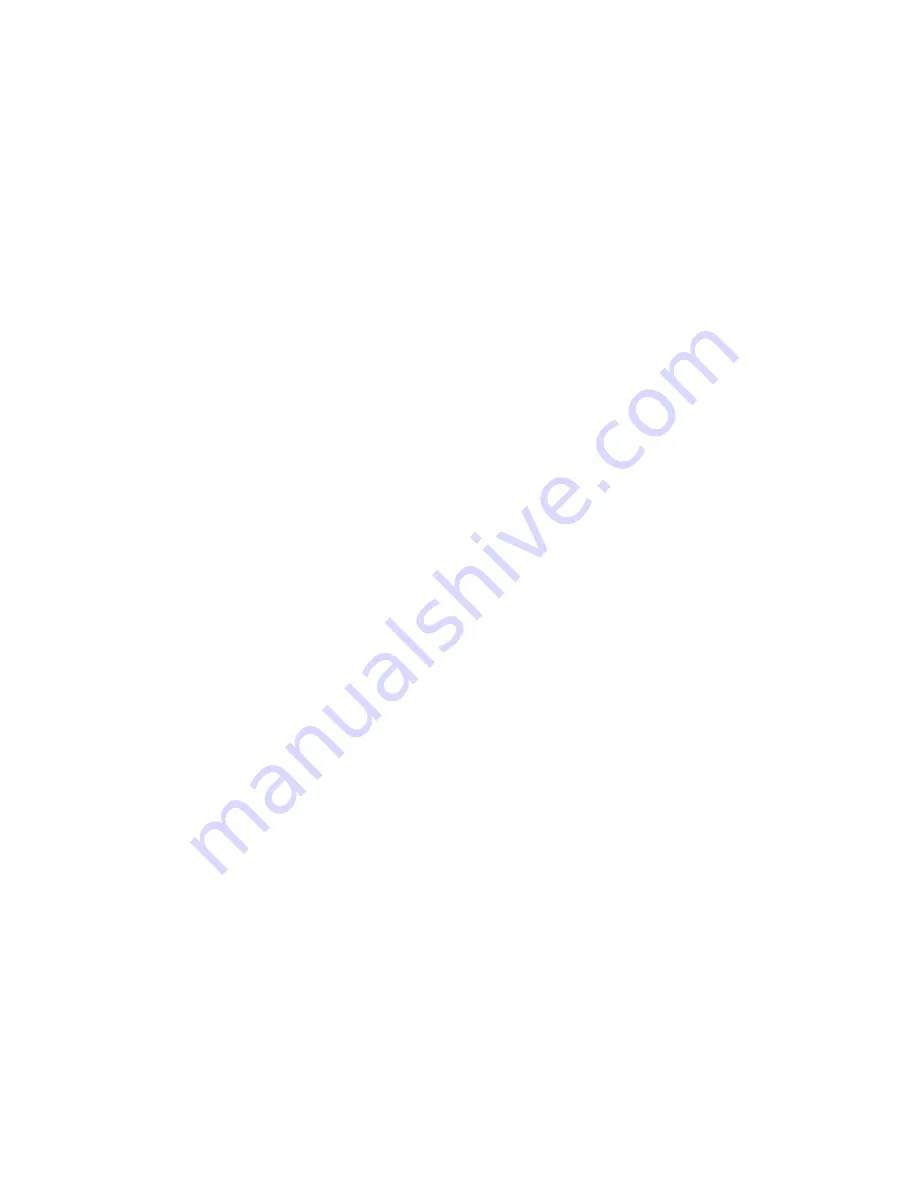
Safety Mat Requirements
The following are minimum requirements for the design, construction, and installation of four-wire safety mat sensor(s) to be
interfaced with the Safety Controller. These requirements are a summary of standards ISO 13856-1, ANSI/RIA R15.06 and
ANSI B11.19. The user must review and comply with all applicable regulations and standards.
Safety Mat System Design and Construction
The safety mat system sensor, Safety Controller, and any additional devices must have a response time that is fast enough
to reduce the possibility of an individual stepping lightly and quickly over the mat’s sensing surface (less than 100 to 200
ms, depending on the relevant standard).
For a safety mat system, the minimum object sensitivity of the sensor must detect, at a minimum, a 30 kg (66 lb) weight on
an 80 mm (3.15 in) diameter circular disk test piece anywhere on the mat’s sensing surface, including joints and junctions.
The effective sensing surface or area must be identifiable and can comprise one or more sensors. The safety mat supplier
should state this minimum weight and diameter as the minimum object sensitivity of the sensor.
User adjustments to actuating force and response time are not allowed (ISO 13856-1). The sensor should be manufactured
to prevent any reasonably foreseeable failures, such as oxidation of the contact elements which could cause a loss in
sensitivity.
The environmental rating of the sensor must meet a minimum of IP54. When the sensor is specified for immersion in water,
the sensor’s minimum enclosure level must be IP67. The interconnect cabling may require special attention. A wicking
action may result in the ingress of liquid into the mat, possibly causing a loss of sensor sensitivity. The termination of the
interconnect cabling may need to be located in an enclosure that has an appropriate environmental rating.
The sensor must not be adversely affected by the environmental conditions for which the system is intended. The effects of
liquids and other substances on the sensor must be taken into account. For example, long-term exposure to some liquids
can cause degradation or swelling of the sensor’s housing material, resulting in an unsafe condition.
The sensor’s top surface should be a lifetime non-slip design, or otherwise minimize the possibility of slipping under the
expected operating conditions.
The four-wire connection between the interconnect cables and the sensor must withstand dragging or carrying the sensor
by its cable without failing in an unsafe manner, such as broken connections due to sharp or steady pulls, or continuous
flexing. If such connection is not available, an alternative method must be employed to avoid such failure, for example, a
cable which disconnects without damage and results in a safe situation.
Safety Mat Installation
The mounting surface quality and preparation for the safety mat must meet the requirements stated by the sensor’s
manufacturer. Irregularities in the mounting surfaces may impair the function of the sensor and should be reduced to an
acceptable minimum. The mounting surface should be level and clean. Avoid the collection of fluids under or around the
sensor. Prevent the risk of failure due to a build-up of dirt, turning chips, or other material under the sensor(s) or the
associated hardware. Special consideration should be given to joints between the sensors to ensure that foreign material
does not migrate under or into the sensor.
Any damage (cuts, tears, wear, or punctures) to the outer insulating jacket of the interconnect cable or to any part of the
exterior of the safety mat must be immediately repaired or replaced. Ingress of material (including dirt particles, insects,
fluid, moisture, or turning-chips), which may be present near the mat, may cause the sensor to corrode or to lose its
sensitivity.
Routinely inspect and test each safety mat according to the manufacturer’s recommendations. Do not exceed operational
specifications, such as the maximum number of switching operations.
Securely mount each safety mat to prevent inadvertent movement (creeping) or unauthorized removal. Methods include, but
are not limited to, secured edging or trim, tamper-resistant or one-way fasteners, and recessed flooring or mounting
surface, in addition to the size and weight of large mats.
Each safety mat must be installed to minimize tripping hazards, particularly towards the machine hazard. A tripping hazard
may exist when the difference in height of an adjacent horizontal surface is 4 mm (1/8 in) or more. Minimize tripping hazards
at joints, junctions, and edges, and when additional coverings are used. Methods include a ground-flush installation of the
mat, or a ramp that does not exceed 20° from horizontal. Use contrasting colors or markings to identify ramps and edges.
Position and size the safety mat system so that persons cannot enter the hazardous area without being detected, and
cannot reach the hazard before the hazardous conditions have ceased. Additional guards or safeguarding devices may be
required to ensure that exposure to the hazard(s) is not possible by reaching over, under, or around the device’s sensing
surface.
A safety mat installation must take into account the possibility of easily stepping over the sensing surface and not being
detected. ANSI and international standards require a minimum depth of field of the sensor surface (the smallest distance
between the edge of the mat and hazard) to be from 750 to 1200 mm (30 to 48 in), depending on the application and the
XS/SC26-2 and SC10-2 Safety Controllers
36
www.bannerengineering.com - Tel: + 1 888 373 6767