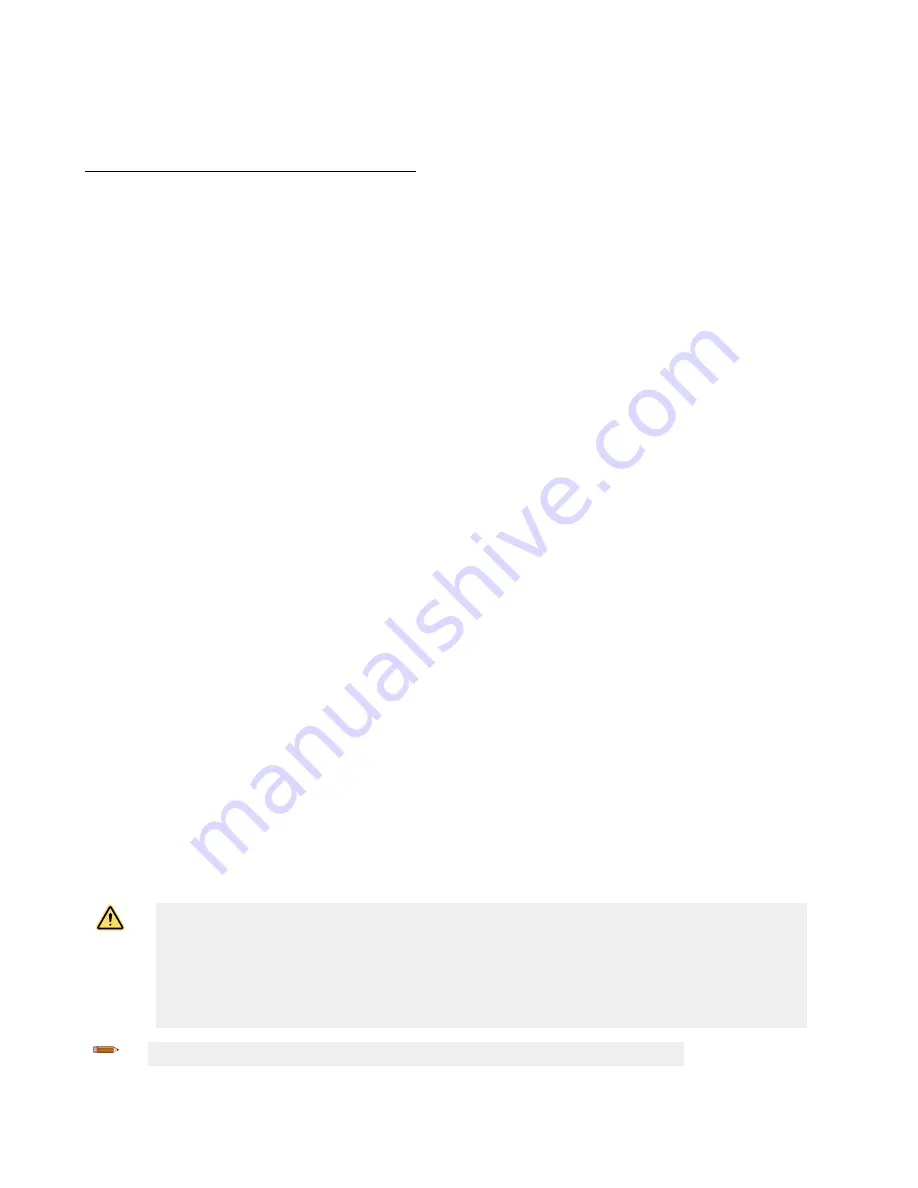
1. When the Safety Controller is first installed, to ensure proper installation.
2. Whenever any maintenance or modification is performed on the System or on the machine being guarded by the
System, to ensure continued proper Safety Controller function (see
Schedule of Required Checkouts
For the initial part of the commissioning checkout, the Safety Controller and associated safety systems must be checked
without power being available to the guarded machine. Final interface connections to the guarded machine cannot take
place until these systems have been checked out.
Verify that:
• The Safety Output leads are isolated—not shorted together, and not shorted to power or ground
• If used, the external device monitoring (EDM) connections have been connected to +24 V dc via the N.C.
monitoring contacts of the device(s) connected to the safety outputs, as described in
on page 53 and the wiring diagrams
• The proper Safety Controller configuration file for your application has been installed into the Safety Controller
• All connections have been made according to the appropriate sections and comply with NEC and local wiring
codes
This procedure allows the Safety Controller and the associated safety systems to be checked out, by themselves, before
permanent connections are made to the guarded machine.
11.2.2 Initial Setup, Commissioning, and Periodic Checkout
Procedures
There are two ways to verify that the Safety Outputs are changing state at the appropriate times in the initial configuration
check out phase (open the Configuration Summary tab in the Software to view the Start-up test and Power-up configuration
settings):
• Monitor the LEDs associated with the inputs and outputs. If the input LED is green, the input is high (or 24 V). If the
input LED is red, the input is low (or 0 V). Similarly, if the RO1 or RO2 output contacts are closed, the corresponding
LED is green. If the contacts are open, the LED is red.
• Start the Live Mode in the Software (the Safety Controller must be powered up and plugged in to the PC via the SC-
USB2 cable).
Start-Up Configuration
Outputs associated with Two-Hand Control, Bypass or Enabling Device functions do not turn on at power-up. After power-
up, switch these devices to the Stop state and back to the Run state for their associated outputs to turn On.
If configured for Normal Power-Up
If latch function is not used: verify that Safety Outputs turn on after power-up.
If either input devices or outputs use the latch function: verify that Safety Outputs do not turn on after the power-up
until the specific manual latch reset operations are performed.
If configured for Automatic Power-Up
Verify that all Safety Outputs turn On within approximately 5 seconds (outputs with On-Delay enabled may take
longer to turn On).
If configured for Manual Power-Up
Verify that all Safety Outputs remain Off after power up.
Wait at least 10 seconds after power-up and perform the Manual Power-Up reset.
Verify that the Safety Outputs turn On (outputs with On-Delay enabled may take longer to turn On).
CAUTION: Verifying Input and Output Function
The Qualified Person is responsible to cycle the input devices (Run state and Stop state) to verify that the
Safety Outputs turn On and Off to perform the intended safeguarding functions under normal operating
conditions and foreseeable fault conditions. Carefully evaluate and test each Safety Controller
configuration to make sure that the loss of power to any safeguarding input device, the Safety Controller,
or the inverted input signal from a safeguarding input device, do not cause an unintended Safety Output
On condition, mute condition, or bypass condition.
Note: If an Input or Output indicator is flashing red, see
XS/SC26-2 and SC10-2 Safety Controllers
126
www.bannerengineering.com - Tel: + 1 888 373 6767