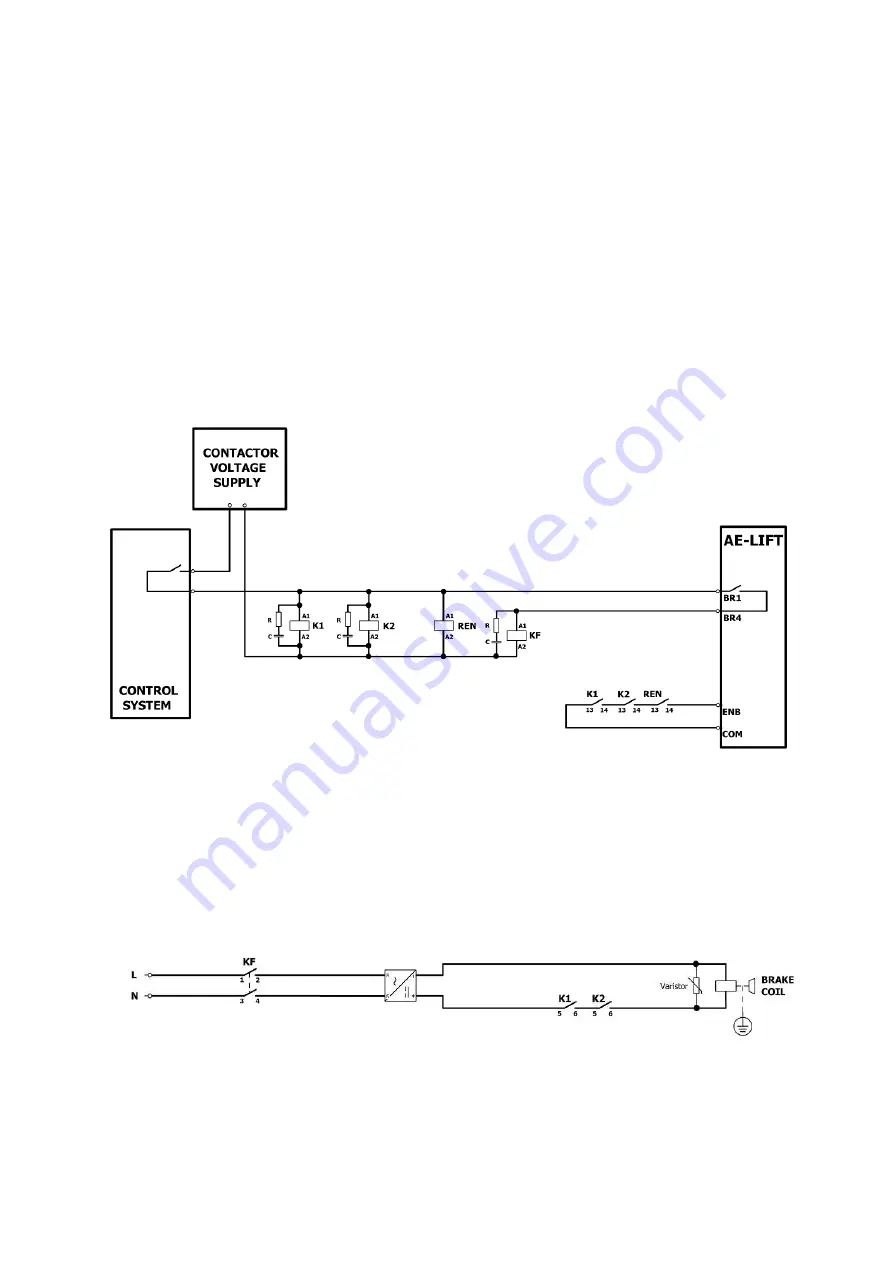
4.3.2 Control of Motor Contactors by Control Panel
When switching of contactors is achieved by control panel, use connections in Figure 4.6.
In this application, when control panel send motion command, it activates K1 and K2 contactor coils and
REN relay. Then K1, K2 and REN relay triggers ENB input. When control panel release contact to stop
motion, REN relay deactivates ENB input faster than the main contactor and stop motor outputs so delay
of contactor release have no risk. For this reason, REN relay is a must when contactor activation is
controlled by control panel. Both of ENB input and motor driver current output are controlled by the
contactor if no REN relay is used. If there is a risk when the lift in motion that has to stop motor
immediately like safety circuit interruption, main contactor starts to release however auxiliary contacts
may still triggering ENB input. In this scenario, main contacts of contactor and driver output may be
damaged.
REN relay is a must in Gearless machine connection. Type of REN relay has to meet the release time
requirement that maximum 20 ms.
Figure 4.6 Motor Contactors are Driven by AE-LIFT (ENB triggers from REN relay)
NOTE : Supply of the contactors in Figure 4.4, 4.5 and 4.6 is shown as AC. When the supply of contactor
is DC, connect a diode to contactor coils instead of RC filter. Do not connect diode to REN relay contacts.
4.4 BRAKE COIL SWITCHING
Connection of brake coil is shown in Figure 4.7.
Figure 4.7 Brake Coil Connection
Switching DC circuit of brake coil from main contacts of motor contactors (K1-K2); switching AC circuit of
brake coil from main contacts of brake contactor (KF) is advised. A varistor according to brake coil voltage
has to connect parallel to brake coil as shown in Figure 4.7.
F/7.5.5.02.95 R:1
9
AE-LIFT