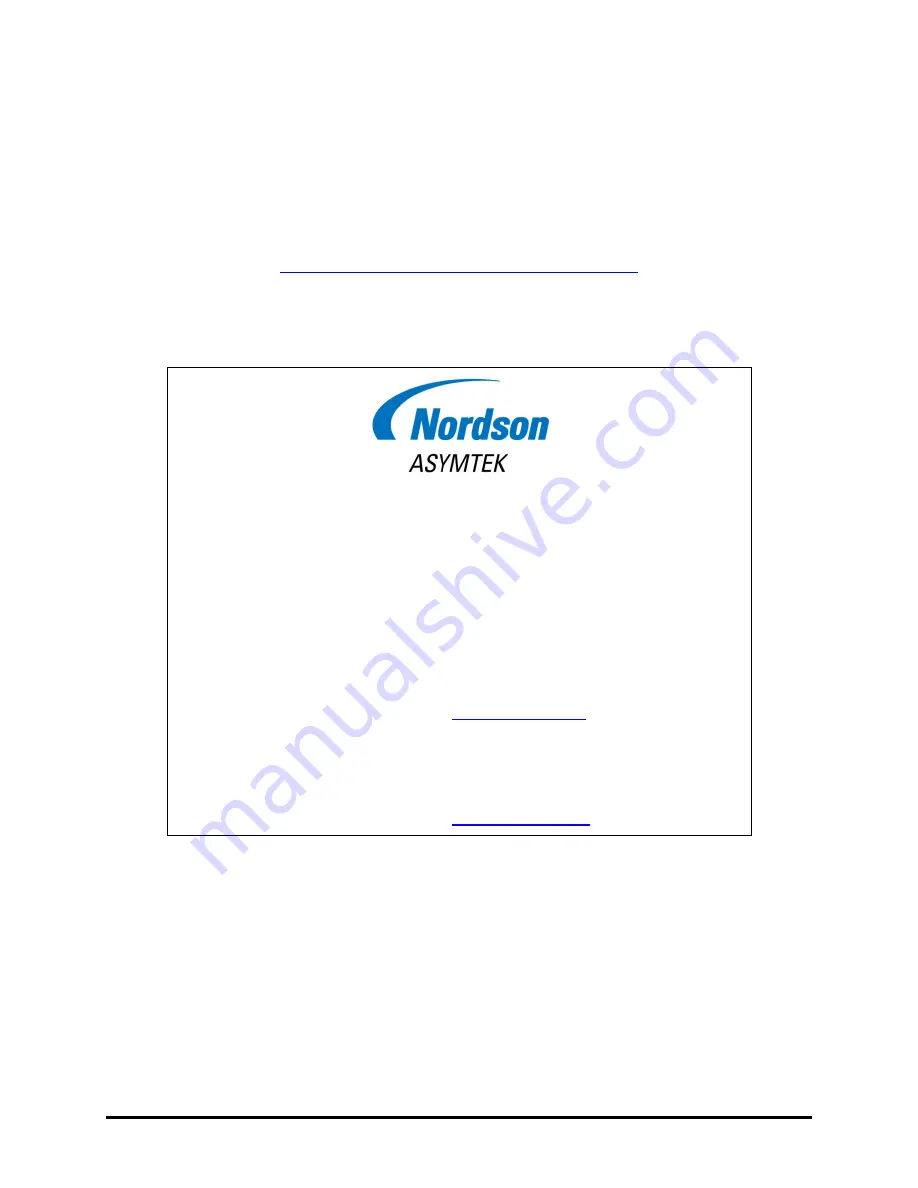
P/N 108384, Revision L
© 2010
NOTICE
This is an Asymtek publication which is protected by copyright. Original copyright date 1992. No part of this document
may be photocopied, reproduced, or translated to another language without the prior written consent of Asymtek. The
information contained in this publication is subject to change without notice.
Manuals on the Internet
For the convenience of Asymtek customers and field service representatives, copies of Asymtek manuals can be
downloaded from:
Asymtek welcomes requests for information, comments, and inquiries about its products. Please contact us using the
information below:
Headquarters
2762 Loker Avenue West
Carlsbad, CA 92010-6603
USA
Toll Free:
1-800-ASYMTEK (1-800-279-6835)
Tel:
+1-760-431-1919
Fax:
+1-760-431-2678
E-mail:
[email protected]
Website:
Technical Support
USA:
1-800-ASYMTEK (1-800-279-6835)
Other regions:
Asymtek
®
, Century
®,
and EasyCoat
®
are registered trademarks of Asymtek.
Microsoft
®
, Windows
®
, and Windows NT
®
are registered trademarks of Microsoft Corporation.
Teflon
®
, Viton
®
, and Zalak
®
are registered trademarks of E.I. DuPont de Nemours & Co.
Chemraz
®
is a registered trademark of Green, Tweed and Company.
Thiokol
®
is a registered trademark of Morton Thiokol, Incorporated.
Parker Lubricant
®
is a registered trademark of Parker Seal.