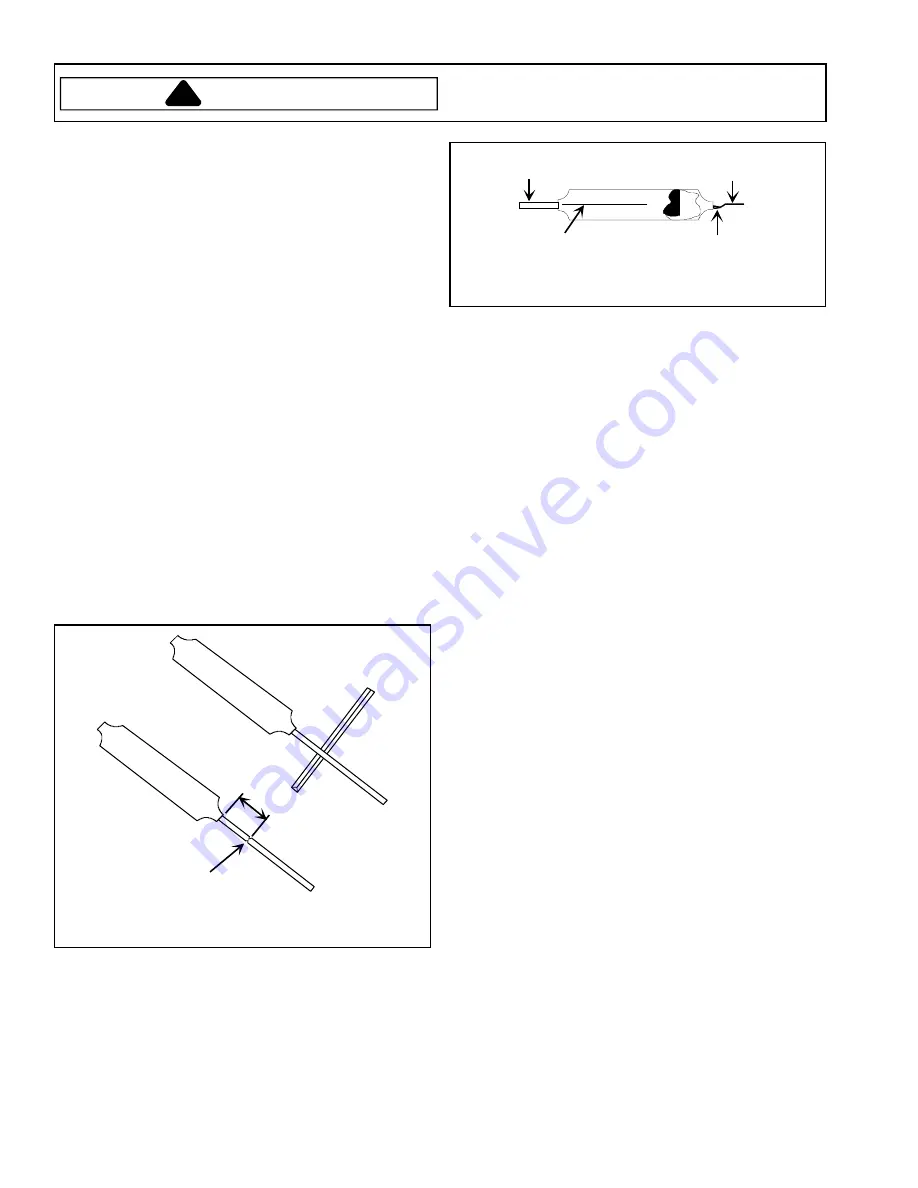
RS1500000 Rev. 0
26
Disassembly Procedures
To avoid risk of electrical shock, personal injury, or
death, disconnect power to unit before following any
disassembly procedures.
WARNING
!
Replacing Dryer
NOTE:
A new drier must be installed whenever any
system component is replaced, or whenever the
system is opened.
The replacement drier is sealed at both ends to prevent
entrance of moisture. Do not break these seals until all
preparations for the installation have been completed.
1. Disconnect line cord from electrical outlet.
2. Clean the process tube using steel wool or fine emery
cloth.
3. Install service valve as close as possible to the tip of
the process tube, for easy pinch-off after recharging
the system.
4. Connect a hose to the service valve and capture the
charge.
NOTE:
Effective July 1, 1992, before opening any
refrigeration system it is the responsibility of the
service technician to capture the refrigerant for
safe disposal.
5. Remove all paint and scale from the capillary tube for
a distance of approximately three inches from the
original joint, (use steel wool or emery cloth).
6. Cut the capillary tube approximately one inch from
the old joint. Verify the cut is uniform around the
tubing, then break it with the fingers
Score here
then snap tube
1"
Cutting Capillary Tube
7. Cut the drier from condenser outlet and thoroughly
clean the end of the tube.
8. Make an offset 1/2 inch (13 mm) from the end of the
capillary tube to prevent its penetrating too far into
drier tubing. When forming the offset, use a radius
large enough so the inside diameter of the tubing is
not reduced.
Condenser end
inlet end
Capillary end
outlet end
Form offset
Flow
direction
Capillary Tube Insertion
9. Cut the inlet tube on the new drier.
10.Snap off the scored end of replacement drier with
your fingers.
11. Install new drier and solder all joints. Use silfos on all
copper to copper joints. On copper to steel joints,
silver solder with proper flux must be used. Excess
flux must be wiped off after soldering.
12.Visually check all soldered joints, evacuate and
recharge the system.
13.Test run the unit to verify proper operation.
14.Pinch process tube and cut off the service valve.
Solder the joint and test for leaks.
Replacing Compressor
Replacement compressors are charged with the correct
amount of oil and contain a holding charge of either dry
nitrogen or a refrigerant.
The replacement compressor will be similar to the type of
compressor originally used and may or may not have an
oil cooler. If the sealed system does not use the oil
cooler, do not disturb the oil cooler plugs. Simply
disregard the oil cooler.
The holding charge assures compressor is dry. A
compressor which shows no evidence of internal
pressure when cutting the line or pulling the plugs,
should be returned for replacement.
When replacing a compressor, cut as close to the
soldered joints as possible. If tubes are not long enough,
it may be necessary to unsolder the joints to allow
connections to the replacement compressor.
When replacing compressor, proceed as follows:
1. Disconnect line cord from electrical outlet.
2. Install a service valve on the process tube.
3. Connect a hose to the service valve and capture the
charge.
NOTE:
Effective July 1, 1992, before opening any
refrigeration system it is the responsibility of the
service technician to capture the refrigerant for
safe disposal.
4. Clean the tubing approximately three inches (76 mm)
at the point of intended cut. Before cutting the tube,
verify it will be long enough to reconnect to the
replacement compressor. If not, unsolder the joints.