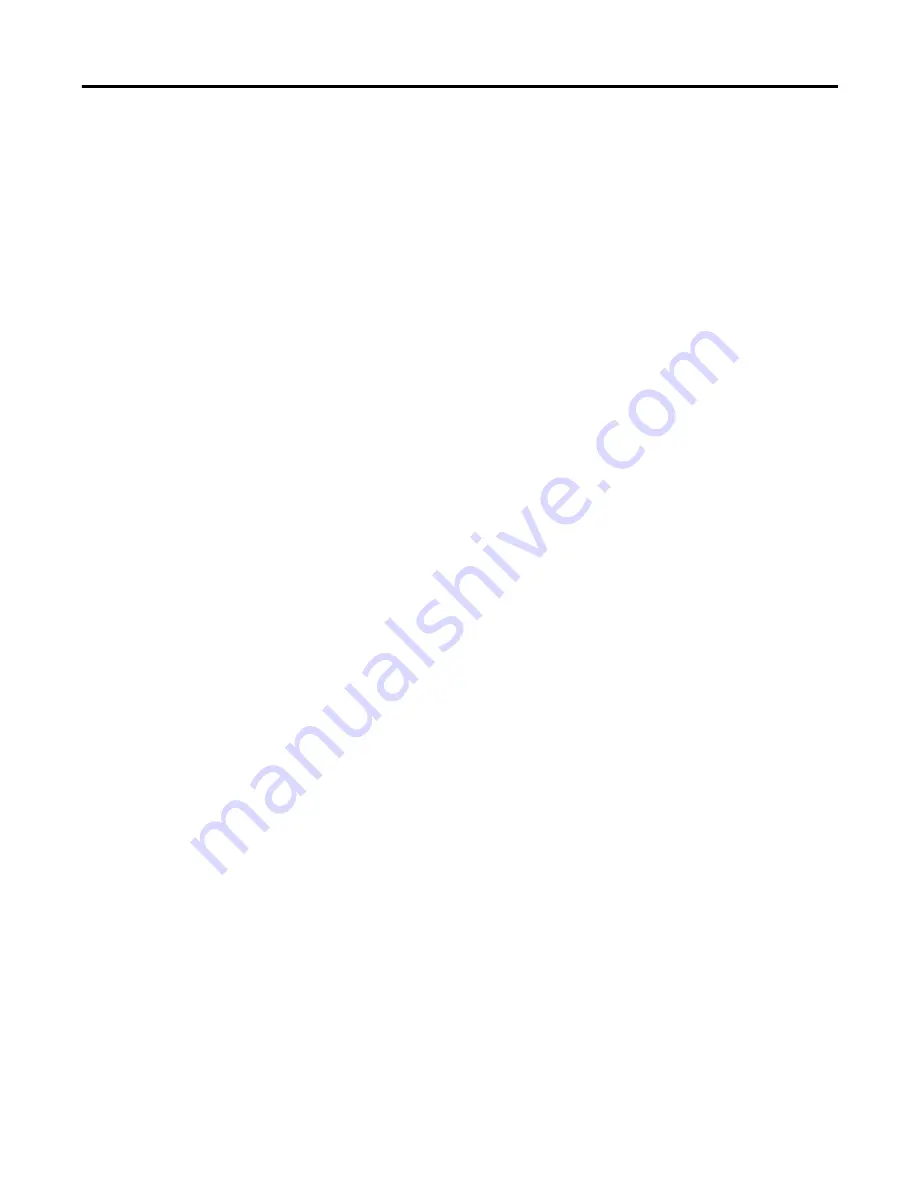
Publication 1766-RM001A-EN-P - October 2008
358
Process Control Instruction
Record the gain value. Return to the MANUAL mode (stop the
process if necessary).
10.
Set the loop update time (and STI time interval if applicable) to a
value of 5 to 10 times faster than the natural period.
For example, if the cycle time is 20 seconds, and you choose to set
the loop update time to 10 times faster than the natural rate, set the
loop update time to 200, which would result in a 2-second rate.
11.
Set the gain K
c
value to 1/2 the gain needed to obtain the natural
period of the process. For example, if the gain value recorded in
step 9 was 80, set the gain to 40.
12.
Set the reset term T
i
to approximate the natural period. If the natural
period is 20 seconds, as in our example, you would set the reset
term to 3 (0.3 minutes per repeat approximates 20 seconds).
13.
Now set the rate T
d
equal to a value 1/8 that of the reset term. For
our example, the value 4 is used to provide a rate term of 0.04
minutes per repeat.
14.
Place the process in the AUTO mode. If you have an ideal process,
the PID tuning is complete.
15.
To make adjustments from this point, place the PID instruction in
the MANUAL mode, enter the adjustment, then place the PID
instruction back in the AUTO mode.
This technique of going to MANUAL, then back to AUTO, ensures
that most of the “gain error” is removed at the time each adjustment
is made. This allows you to see the effects of each adjustment
immediately. Toggling the PID rung allows the PID instruction to
restart itself, eliminating all of the integral buildup. You may want to
toggle the PID rung false while tuning to eliminate the effects of
previous tuning adjustments.
Verifying the Scaling of Your Continuous System
To ensure that your process is linear, and that your equipment is properly
connected and scaled, do the following:
1.
Place the PID instruction in MANUAL and enter the following
parameters:
–
type:
0
for MinS
–
type:
100
for MaxS
efesotomasyon.com - Allen Bradley,Rockwell,plc,servo,drive