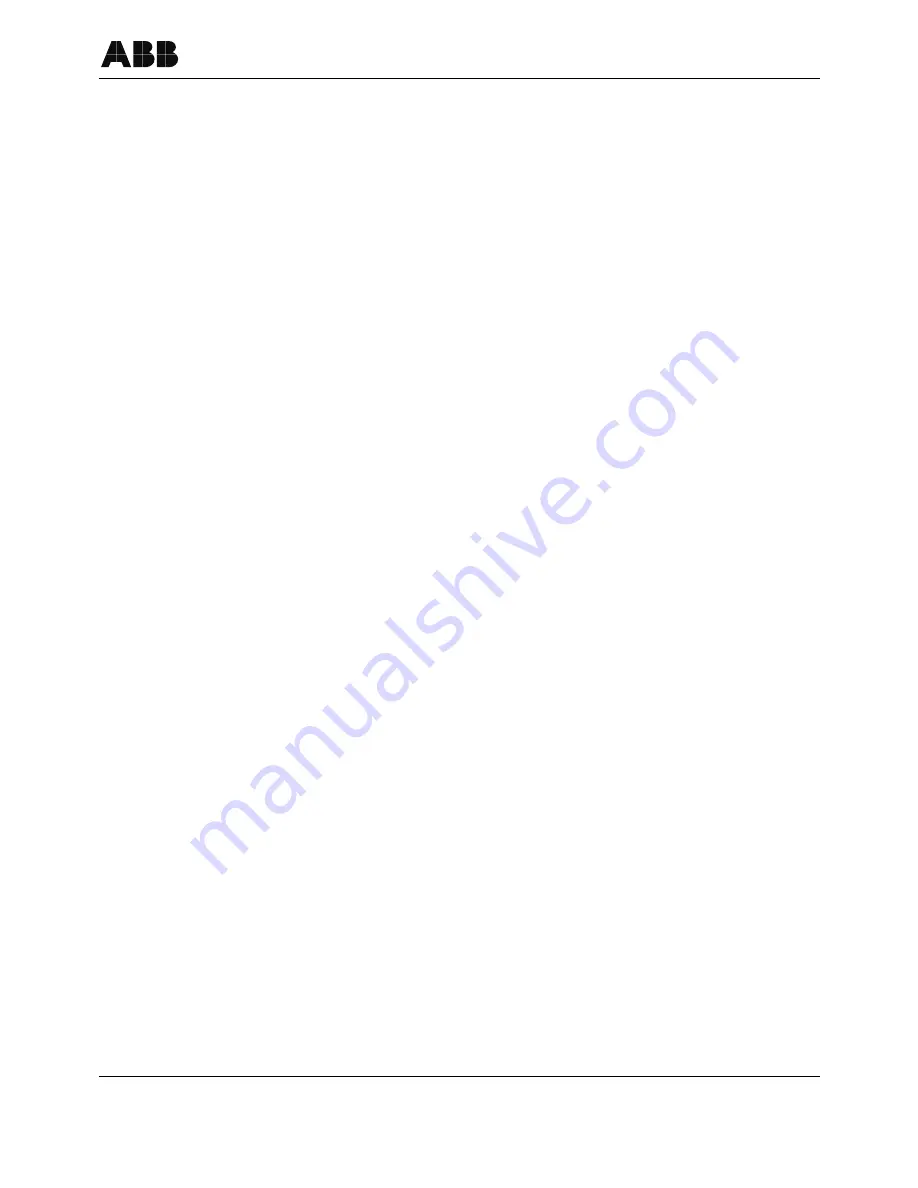
Mechanical installation
12
Sensyflow iG, Version 1.00
42/14-39 EN
• Components that influence the flow (e. g. valves, shut-off fittings and similar components) should pos-
sibly be mounted at the outlet run length, i. e. behind the measuring point .
• The sealings used must not change the cross-section of the pipeline opening and must guarantee the
absolute tightness after installing the transducer and pipe component.
• Centric installation must be especially observed when using pipe component 1. The inside diameter of
pipes and flanges must match exactly. Every step, edge, or untidy weld disturbs the flow profile forma-
tion, thus reducing the achievable measuring accuracy.
• The flow direction must be in line with the arrow indicated on the pipe component. The positioning pin
at the pipe component respectively weld-on adapter must be at the outlet run length (behind the measu-
ring point).
To achieve the stated measuring accuracy, the steadying run lengths shown above are absolutely requi-
red. For combinations of several inlet run disturbances, e. g. valve and reducer, you must always consider
the longer inlet run length.
In confined spaces at the mounting location the outlet run length can be reduced to 3
×
D. The reduction
of the minimum inlet run length, however, will take it's tall on the achievable accuracy. High repeatability
of the measuring value is still provided.
Under certain circumstances, special calibration can be performed for insufficient steadying run lengths.
For this purpose and in individual cases, consult ABB's DKD Calibration Department at Alzenau.
For gases with extremely low density (hydrogen, helium) the stated steadying run lengths must be dou-
bled.
4.1.2
Adaption of a Sensyflow iG transducer by using a weld-on adapter
When installing the transducer in pipes with larger nominal width or non-round cross-section, the weld-
on adapter must be welded to the pipeline under consideration of the following information:*
1.
The weld-on adapter must be shortened to length L according to following formula:
L = L
1
- ½
× ∅
D
outside
with L1 = 263, 425 or 775 mm (transducer lengths)
– Observe the pipeline wall thickness and amount of shrinkage when welding!
– The distance L1 from the flange top edge of the adapter to the pipe center line must be within
a tolerance of ±2 mm.
2.
Rectangularity to the pipe axis must be absolutely kept (max. tolerance 2°).
3.
The positioning pin of the adapter must be aligned in flow direction to the pipe axis (at outlet run
length, behind measuring point).
4.
After welding the free passage for inserting the transducer must be at least 28 mm (if required, use
drill to clear).
5.
Transducer installation:
– For the standard version, insert the supplied O-ring (55
×
3 mm) into the provided groove.
– For special version with groove and tongue system you must use a suitable flat sealing!
– Push the transducer into the adapter and screw together.