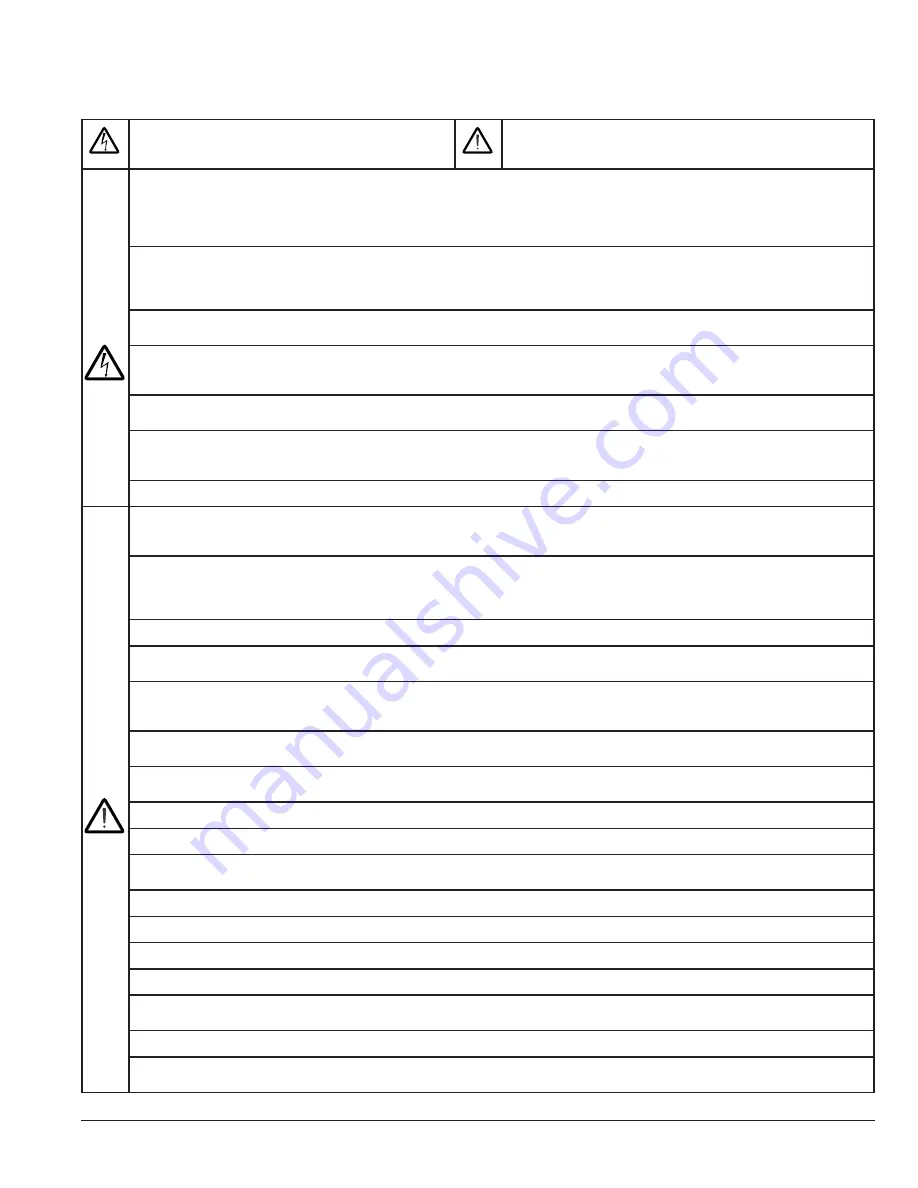
Introduction 1-3
MN448
Danger: Indicates a risk of electric shock, which,
if not avoided, could result in damage to the
equipment and possible injury or death.
Danger: Indicates a potentially hazardous situation other
than electrical, which if not avoided, could result in damage
to property.
The IMD should be properly installed and commissioned. If installed incorrectly it may present a safety hazard. The IMD
uses high voltages and currents, carries a high level of stored electrical energy, and is used to control mechanical plant
that may cause injury. Close attention is required to system design and electrical installation to avoid hazards in either
normal operation or in the event of equipment malfunction. Only qualified electricians are allowed to install and maintain
this product.
System design, installation, commissioning and maintenance must be carried out only by personnel who have the
necessary training and experience. They must carefully read this safety information and the instructions in this Guide and
follow all information regarding transport, storage, installation and use of the IMD, including the specified environmental
limitations.
Do not perform any flash test or voltage withstand test on the IMD. Any electrical measurements required should be
carried out with the IMD disconnected.
Electric shock hazard! Disconnect and ISOLATE the IMD before attempting any work on it. High voltages are present at
the terminals and within the IMD for up to 10 minutes after disconnection of the electrical supply. Always ensure by using
a suitable multimeter that no voltage is present on any drive power terminals prior to commencing any work.
Where supply to the IMD is through a plug and socket connector, do not disconnect until 10 minutes have elapsed after
turning off the supply.
Ensure correct grounding connections. The ground cable must be sufficient to carry the maximum supply fault current
which normally will be limited by the fuses. Suitably rated fuses should be fitted in the mains supply to the IMD, according
to any local legislation or codes.
Do not carry out any work on the IMD control cables when power is applied to the IMD or to the external control circuits.
Within the European Union, all machinery in which this product is used must comply with the Machinery Directive
2006/42/EC, Safety of Machinery. In particular, the machine manufacturer is responsible for providing a main switch and
ensuring the electrical equipment complies with EN60204-1.
The level of integrity offered by the IMD control input functions – for example stop/start, forward/reverse and maximum
speed is not sufficient for use in safety-critical applications without independent channels of protection. All applications
where malfunction could cause injury or loss of life must be subject to a risk assessment and further protection provided
where needed.
The IMD can start at power up if the enable input signal is present.
The STOP function does not remove potentially lethal high voltages. ISOLATE the IMD and wait 10 minutes before
starting any work on it. Never carry out any work on the IMD or power cable when the input power is still applied.
The IMD can be programmed to operate at speeds up to Motor Rated Speed (parameter 9908). Obtain confirmation from
the manufacturers of the driven machine about suitability for operation over the intended speed range prior to machine
start up.
Do not activate the automatic fault reset function on any systems whereby this may cause a potentially dangerous
situation.
The IMD has an Ingress Protection rating of IP55 (drive assembly) and IP54 (motor) and must be installed in a suitable
environment.
The IMDs are intended for indoor use only.
Do not carry out drilling operations with the IMD in place, dust and metal shavings from drilling may lead to damage.
The entry of conductive or flammable foreign bodies should be prevented. Flammable material should not be placed
close to the IMD.
Relative humidity must be less than 95% (non-condensing).
Ensure that the supply voltage, frequency and number of phases correspond to the rating of the IMD as delivered.
Never connect the mains power supply to the Output terminals U, V, W.
Do not install any type of automatic switchgear between the drive and the motor
Wherever control cabling is close to power cabling, maintain a minimum separation of 4 in. (100 mm) and arrange
crossings at 90 degrees.
Ensure that all terminals are tightened to the appropriate torque setting
Do not attempt to carry out any repair of the IMD. In the case of suspected fault or malfunction, contact your local ABB
representative for further assistance.
Содержание EC Titanium ECS100A1H1DF4
Страница 1: ... MN448_May 2020 May 2020 EC Titanium Manual User s guide ...
Страница 10: ...1 4 Introduction MN448 ...
Страница 20: ...3 4 Mechanical Information and Mounting MN448 ...
Страница 26: ...4 6 Electrical Installation and Planning MN448 ...
Страница 32: ...5 6 Control Pad Wiring and Keypad Interface MN448 ...
Страница 36: ...6 4 Keypad Programming and Basic Operation MN448 ...
Страница 44: ...8 4 Parameter Navigation and Groups MN448 ...
Страница 51: ...9 7 Control Modes MN448 ...
Страница 77: ...11 8 Standalone Motor and ABB Drive Setup MN448 ...
Страница 99: ...A 12 Modbus RTU Example Connection MN448 ...
Страница 102: ......