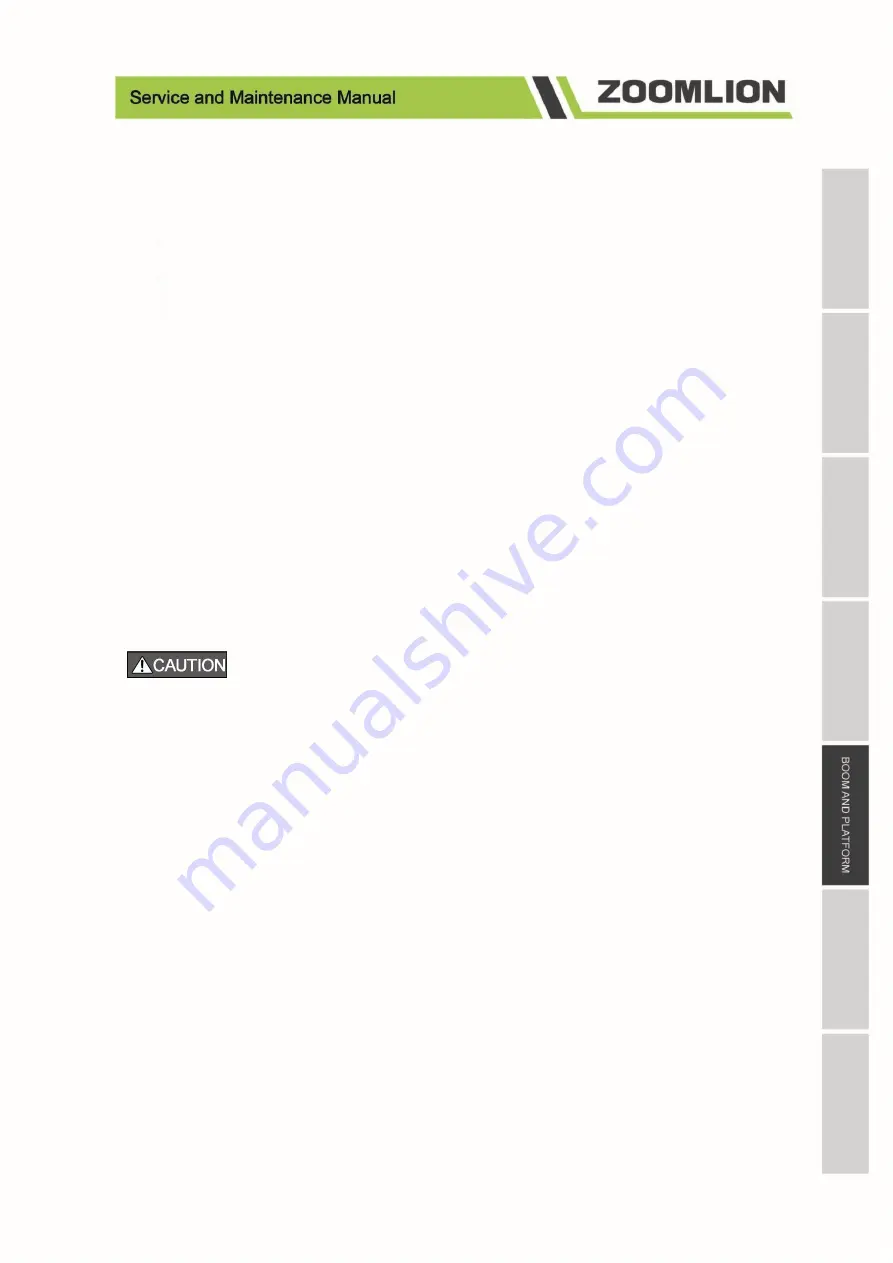
5-9
e.
Use the lifting equipment to support the boom to make the boom slowly swing upward, and adjust
the support of the swing cylinder at the same time. During the boom swing upward, one end of the
swing cylinder pin will be separated from the base boom.Continue to lift the boom until the pin 2 is
completely exposed and in a position that is easy to disassemble.
f.
Use suitable lifting equipment to support the lifting cylinder near the end of pin 2 and remove pin 2.
g.
With the assistance of lifting equipment, slowly and carefully take out the lifting cylinder to avoid
damage from the collision between the luffing and the connecting rod.
h.
Plug the connector of the lifting cylinder with a suitable plug to prevent dust and other pollutants
from entering the oil circuit.
5.2.4.2 Inspection
a.
Inspect the shaft pin for wear, scratches, taper, ovality or other damage and replace the pin if
necessary.
b.
Inspect the inner ring of the bearing for scratches, distortion, wear or other damage and replace the
bearing if necessary.
c.
Inspect all threaded parts for damage such as stretching, thread deformation or distortion and replace
if necessary.
Refer to the Pin and Bearing Inspection Instructions in the Section 3 for pin and bearing inspection.
5.2.4.3 Installation
a.
Follow the reverse steps of disassembly. The interface of the hydraulic pipe joint and balance valve
before installation should be cleaned to prevent contaminants from entering the hydraulic system.
b.
A hydraulic system pipe joint equipped with a sealing device needs to replace a sealing device before
the hydraulic line is connected.
c.
Threaded fasteners should be tightened in place according to the torque values in Section 2
Specifications.
5.2.5 Boom
5.2.5.1 Disassembly
Summary of Contents for ZT20J
Page 8: ......
Page 9: ......
Page 17: ......
Page 18: ......
Page 25: ......
Page 26: ......
Page 43: ......
Page 44: ......
Page 58: ......
Page 59: ......
Page 83: ......
Page 84: ......
Page 96: ......
Page 97: ......
Page 105: ...7 8 Figure 7 11 Electrical Schematics Figure 1 6 Perkins engine ...
Page 106: ...7 9 Figure 7 12 Electrical Schematics Figure 1 6 Deutz D447 engine ...
Page 107: ...7 10 Figure 7 13 Electrical Schematics Figure 1 6 Deutz D2 9 engine ...
Page 108: ...7 11 Figure 7 14 Electrical Schematics Figure 2 6 ...
Page 109: ...7 12 Figure 7 14 Electrical Schematics Figure 3 6 ...
Page 110: ...7 13 Figure 7 16 Electrical Schematics Figure 4 6 ...
Page 111: ...7 14 Figure 7 17 Electrical Schematics Figure 5 6 ...
Page 112: ...7 15 Figure 7 18 Electrical Schematics Figure 6 6 ...
Page 113: ...7 16 7 5 Hydraulic Schematics Figure 7 19 Hydraulic Schematics Figure ...