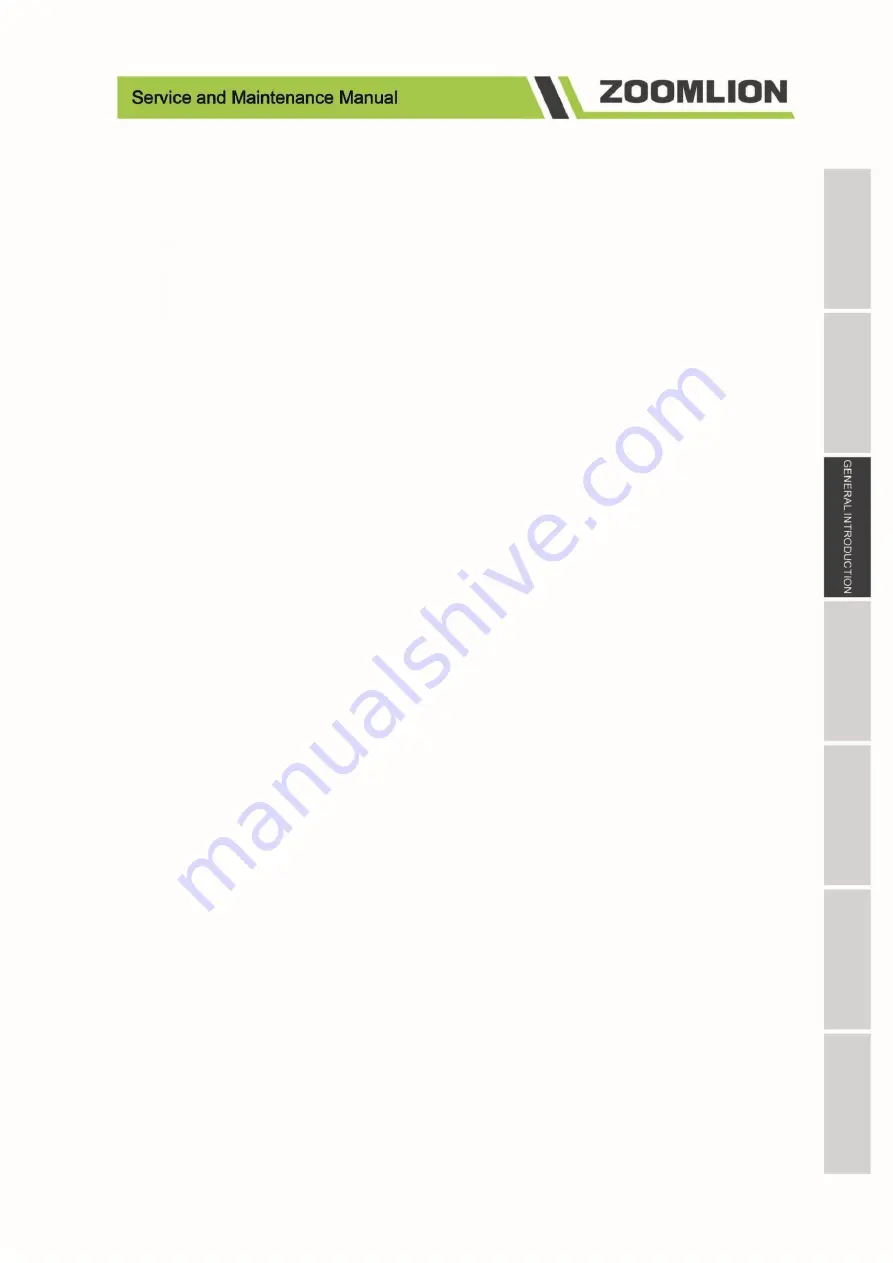
3-5
The battery was cleaned with a non-metallic brush and an aqueous solution of sodium bicarbonate. Then
rinse with clean water. When the battery is completely dry, apply the battery terminals with an
anti-corrosion compound.
3.2.14 Lubrication and maintenance
Parts and components that require lubrication and maintenance refer to the Regular Maintenance in
Section 5.
3.3 Lubrication and Information
3.3.1 Hydraulic system
a)
Contaminants are the primary factor in invading the hydraulic system. Contaminants can invade in
various ways, such as improper use of hydraulic oil, or the moisture, grease, metal shavings,
sealing elements, sand, etc. enter the system during maintenance, or the hydraulic pump forms
cavitation due to insufficient preheating of the system or leakage of the hydraulic pump inlet pipe.
b)
The design and manufacturing tolerances of the working part of the component are very strict, so
even if a small amount of dirt or foreign matter enters the system, it may cause wear or damage to
the component and may cause operational failure. Always take precautions to keep the hydraulic
fluid clean, including stored spare oil. The hydraulic system filter is inspected, cleaned, or replaced
as necessary, at intervals specified in the Regular Maintenance in Section 5. Always check for the
presence of metal particles in the filter.
c)
Turbidity of the hydraulic fluid indicates that the water content is too high, which may promote the
growth of organic matter and cause oxidation or corrosion. If this happens, the system should be
drained, flushed, and refilled with clean hydraulic fluid.
d)
Other hydraulic fluids may not contain the specified additives or have different viscosities, so do
not mix products of different brands or types. It is recommended to use high quality mineral oils
with a viscosity suitable for the machine’s operating environment.
The hydraulic oil cleanliness of the machine at the factory is NAS9 (ISO4406 18/15). The normal
operation of the machine requires that the hydraulic oil cleanliness is not lower than NAS10 (ISO4406
19/16). We recommend that the hydraulic oil be inspected every 6 months. When it is time to change the
oil, at least the oil should be sampled once. The oil sample can be sent to a hydraulic oil manufacturer or
a qualified third-party testing agency for analysis and to determine if it is still available.
Note: due to the wear of the screen components, metal particles may appear in the hydraulic fluid or
filter of the new machine.
3.3.2 Hydraulic oil
For hydraulic oil types and models, please refer to Table 2-3 Hydraulic oil technical parameters (Table
3-2 is not used to specify the type and parameters of hydraulic oil). Please select the hydraulic oil of the
Summary of Contents for ZT20J
Page 8: ......
Page 9: ......
Page 17: ......
Page 18: ......
Page 25: ......
Page 26: ......
Page 43: ......
Page 44: ......
Page 58: ......
Page 59: ......
Page 83: ......
Page 84: ......
Page 96: ......
Page 97: ......
Page 105: ...7 8 Figure 7 11 Electrical Schematics Figure 1 6 Perkins engine ...
Page 106: ...7 9 Figure 7 12 Electrical Schematics Figure 1 6 Deutz D447 engine ...
Page 107: ...7 10 Figure 7 13 Electrical Schematics Figure 1 6 Deutz D2 9 engine ...
Page 108: ...7 11 Figure 7 14 Electrical Schematics Figure 2 6 ...
Page 109: ...7 12 Figure 7 14 Electrical Schematics Figure 3 6 ...
Page 110: ...7 13 Figure 7 16 Electrical Schematics Figure 4 6 ...
Page 111: ...7 14 Figure 7 17 Electrical Schematics Figure 5 6 ...
Page 112: ...7 15 Figure 7 18 Electrical Schematics Figure 6 6 ...
Page 113: ...7 16 7 5 Hydraulic Schematics Figure 7 19 Hydraulic Schematics Figure ...