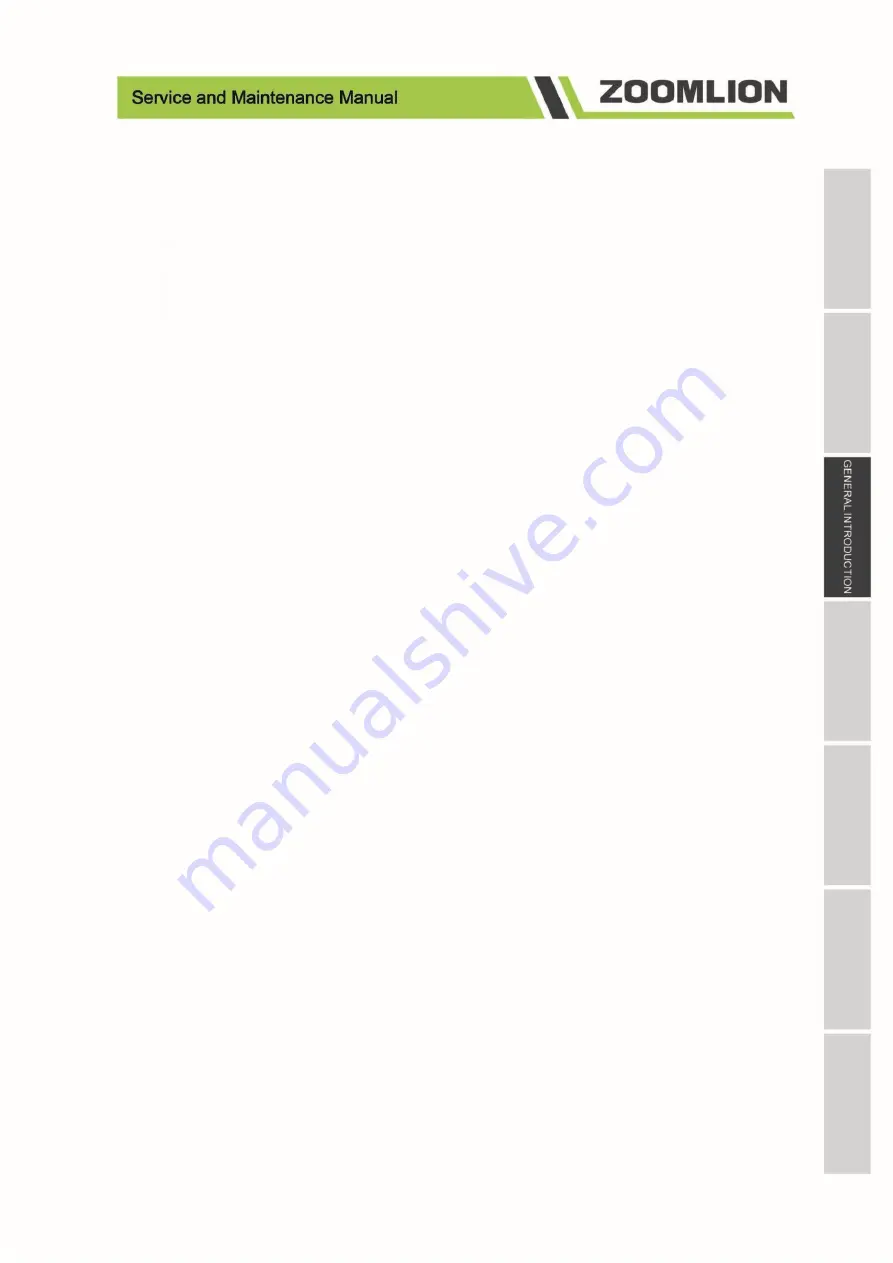
3-7
more.
3.3.3 Hydraulic oil replacement
Good quality hydraulic fluids are critical to machine performance and service life. Unclean hydraulic
fluid can affect machine performance and can cause damage to parts if used continuously. This
operation should be performed more frequently in adverse working conditions.
a)
Regular hydraulic fluid changes are required to use the recommended crankcase or hydraulic fluid.
Run for the first time for 50 hours, and the filter element should be replaced every 300 hours
thereafter. If the hydraulic oil has not been replaced for two years, it should be tested once every
quarter, and the hydraulic oil should be replaced if the test fails. If you need to replace the
hydraulic fluid, use a hydraulic fluid that meets or exceeds the specifications described in this
manual. If you are unable to obtain the same type of product with random hydraulic oil, please
consult your local supplier for the right equivalent. Do not mix petroleum with synthetic oil. We
recommend the hydraulic oil replacement time used by the machine as follows:
b)
First replacement: run for 500 hours after debugging.
c)
Second or thereafter replacement: run 2,000 hours or once every two years.
d)
The above recommended values are suitable for most applications. Higher temperatures, pressures
and adverse working conditions will accelerate oil failure, so hydraulic oil should be replaced
earlier. If the system load is small, the oil change time can be extended.
e)
Always take the necessary measures to keep the hydraulic oil clean. Ensure all the containers used
are clean. After replacing the hydraulic fluid of the hydraulic system, the mesh element of the filter
must be cleaned and the cartridge filter replaced.
f)
After shutting down the equipment, conduct good preventive maintenance measures, that is,
implement a thorough inspection of all hydraulic components, piping, fittings, etc., and perform a
functional check of each system before reusing the machine.
3.3.4 Lubrication specification
Special lubricants recommended by the component manufacturer are always the best choice. However,
multi-purpose greases typically have characteristics that meet the requirements of various single
function greases. If you have any questions regarding the use of grease in maintenance supplies, please
consult your local supplier. Please refer to the description of the lubricant abbreviation in the
Lubrication Table in Section 2.
3.4 Cylinder Drift Test
Use the following method to determine the maximum acceptable cylinder drift.
3.4.1 Platform drift
Measure drift from the platform to the ground. Raise the lower boom slightly (if equipped) and fully
Summary of Contents for ZT20J
Page 8: ......
Page 9: ......
Page 17: ......
Page 18: ......
Page 25: ......
Page 26: ......
Page 43: ......
Page 44: ......
Page 58: ......
Page 59: ......
Page 83: ......
Page 84: ......
Page 96: ......
Page 97: ......
Page 105: ...7 8 Figure 7 11 Electrical Schematics Figure 1 6 Perkins engine ...
Page 106: ...7 9 Figure 7 12 Electrical Schematics Figure 1 6 Deutz D447 engine ...
Page 107: ...7 10 Figure 7 13 Electrical Schematics Figure 1 6 Deutz D2 9 engine ...
Page 108: ...7 11 Figure 7 14 Electrical Schematics Figure 2 6 ...
Page 109: ...7 12 Figure 7 14 Electrical Schematics Figure 3 6 ...
Page 110: ...7 13 Figure 7 16 Electrical Schematics Figure 4 6 ...
Page 111: ...7 14 Figure 7 17 Electrical Schematics Figure 5 6 ...
Page 112: ...7 15 Figure 7 18 Electrical Schematics Figure 6 6 ...
Page 113: ...7 16 7 5 Hydraulic Schematics Figure 7 19 Hydraulic Schematics Figure ...