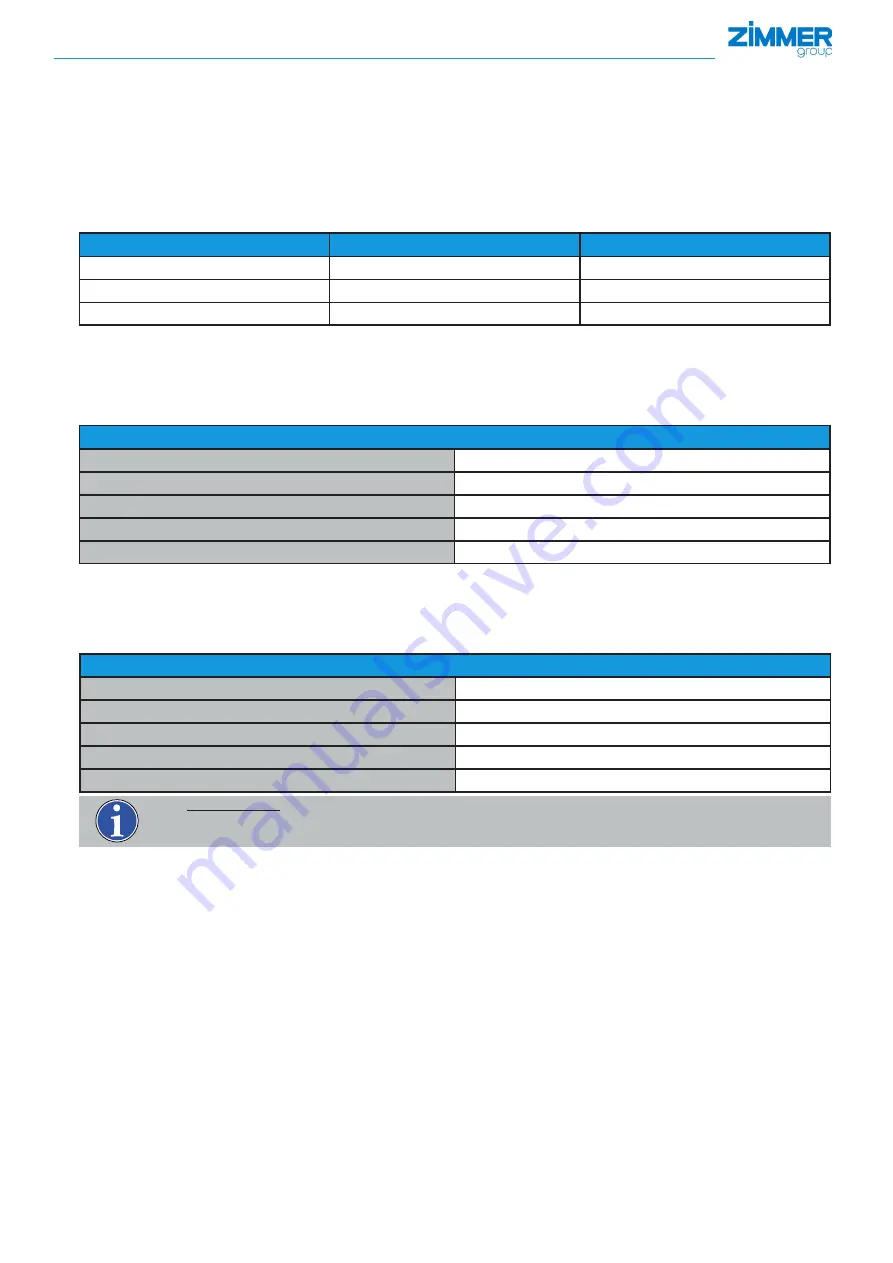
DDOC00247
enu / 2018-09-14 / Index a
INSTALLATION AND OPERATING INSTRUCTIONS:
Pneumatic gripper, intelligent GPP/GPD5000IL series
Zimmer GmbH
●
Im Salmenkopf 5
●
77866 Rheinau, Germany
●
Phone: +49 7844 9138-0
●
Fax: +49 7844 9138-80
●
www.zimmer-group.de
12
The stroke measurement system has a resolution of the position of 1/100 mm.
Product
Stroke per gripper jaw
Maximum "TeachPosition" (approx.)
GPP/GPD5006IL
6 mm
1200
GPP/GPD5008IL
8 mm
1600
GPP/GPD5010IL
10 mm
2000
Example:
Explanation of the values using GPP5006IL
Full stroke of 6mm per gripper jaw:
"BasePosition" = 0
"WorkPosition" = 1200 (2*6*100 => 2 gripper jaws * 6 mm stroke per gripper jaw * Resolution at 1/100 mm)
The "TeachPosition" can acquire values from 0 to 1200
Details:
Name
TeachPosition
Data type
UINT 16
Permission
Write
Transmission
Cyclical
Value range
0–max. jaw stroke of the gripper
7.5.6. "PositionTolerance" parameter
This parameter can be used to transmit the current desired position detection tolerance for the workpiece to the gripper.
Also see
Section 6.3.4
This can be input in mm/100 and always functions equally well in both the "+" direction and the "-" direction.
Details
Name
Position tolerance
Data type
UINT 8
Permission
Write
Transmission
Cyclical
Value range
0–255
INFORMATION:
All transmitted process data must be acquired using the "ControlWord" = 0x01 "Data transfer."
Refer to "HANDSHAKE" procedure
7.5.5 "TeachPosition" parameter
The "TeachPosition" process data byte is only valid if, at the same time, the workpiece number is "0".
The "TeachPosition" tells the gripper the position at which the workpiece is expected. The "PositionTolerance" parameter can be
used to set a tolerance range around this position. Thus the gripper can distinguish whether a correct or incorrect workpiece has
been gripped. Confirmation that the correct workpiece has been gripped is communicated to the controller via the "StatusWord"
(input). If the detection is correct, the "teach" bit is set in this status word, thereby giving the user the option to monitor this work
step.