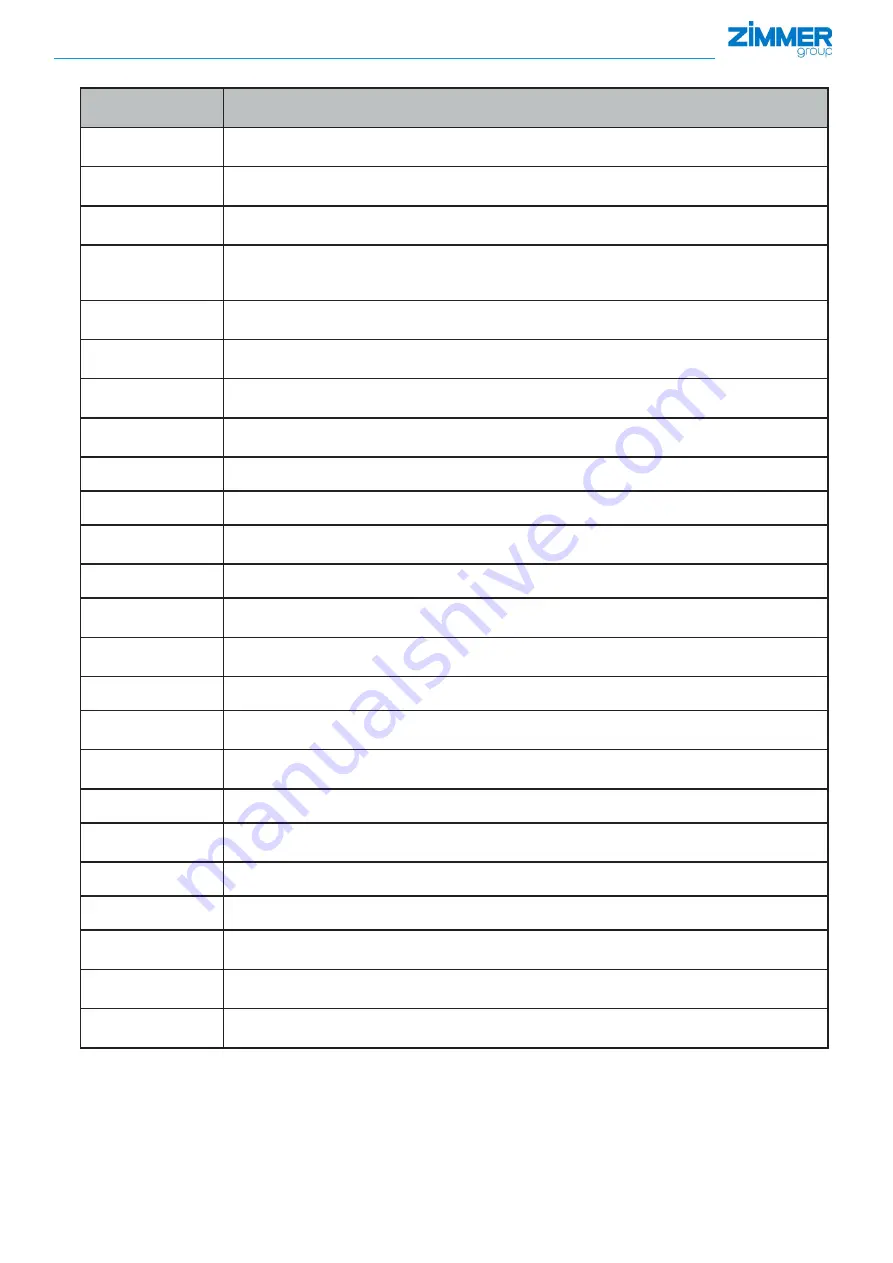
DDOC00247
enu / 2018-09-14 / Index a
INSTALLATION AND OPERATING INSTRUCTIONS:
Pneumatic gripper, intelligent GPP/GPD5000IL series
Zimmer GmbH
●
Im Salmenkopf 5
●
77866 Rheinau, Germany
●
Phone: +49 7844 9138-0
●
Fax: +49 7844 9138-80
●
www.zimmer-group.de
20
10. Glossary
Term/
abbreviation
Description
"BasePosition"
Base position
Initial position from which the gripper moves
"WorkPosition"
Work position,
Any position of the gripper within the maximum and minimum possible movement range
"TeachPosition"
Teach position,
for conditioning the gripper to the workpiece.
"ActualPosition"
Current position,
Position of the gripper jaws with respect the maximum
possible stroke
"ControlWord"
Control word,
Parameter for command execution
"DeviceMode"
Process parameter,
Switch that changes between movement profiles of the gripper
"Workpiece No."
Workpiece number,
Option for saving multiple recipes
"PositionTolerance"
Position tolerance,
referring to the tolerance of the teach position
HRC
H
uman-
R
obot-
C
ollaboration
Status
Display parameter
Diagnostics
Diagnostics
Display parameter = error number
Offset
Value for the subsequent correction of a parameter
"GripForce"
Gripping force
Value in the data set of the controller
Direction
Command/signal from the controller
Specification of the movement direction of the gripper jaws
Normal
N
The gripper can be used for both external and internal gripping (no gripping force safety device).
normally open
NO
The gripper is set up for external gripping.
With gripping force safety device
normally closed
NC
The gripper is set up for internal gripping.
With gripping force safety device
GND
Ground/power supply 0V
Workpiece No.
Workpiece number
Designation of the data set in the control system
GPD
Pneumatic gripper/three-jaw version
GPP
Pneumatic gripper/two-parallel-jaw version
Traversing routine
Traversing routine
Defined process for moving the gripper jaws
Travel path
Travel path
Path on which the gripper jaws travel
Adjust
adjust
The gripper carries out an adjustment run