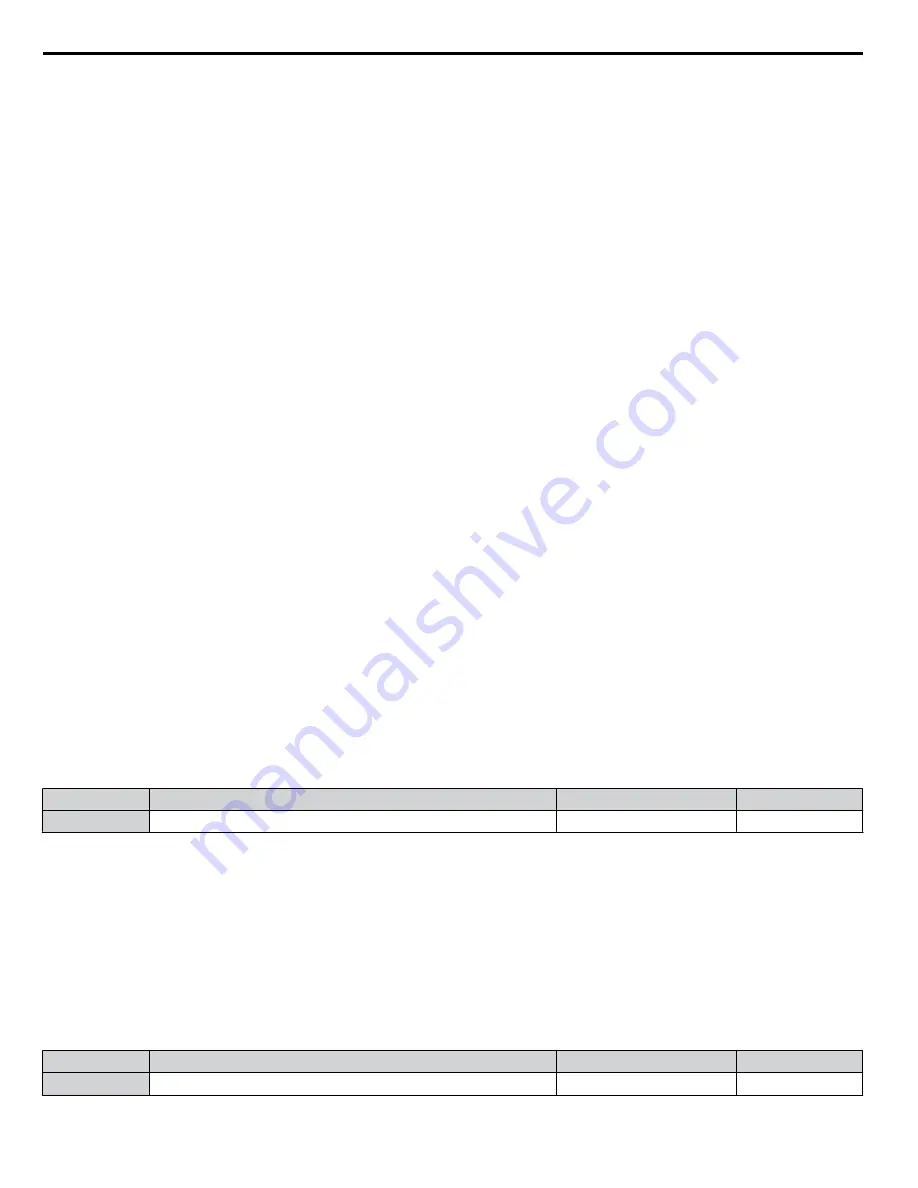
Example: If the analog frequency reference from analog input terminal A1 is 50% and a bias of 20% is applied by analog input
terminal A2, the resulting frequency reference will be 70% of the maximum output frequency.
Setting 1: Frequency Gain
The input value of an analog input set to this function will be multiplied with the analog frequency reference value.
Example: If the analog frequency reference from analog input terminal A1 is 80% and a gain of 50% is applied from analog
input terminal A2, the resulting frequency reference will be 40% of the maximum output frequency.
Setting 2: Auxiliary Reference 1
Sets the auxiliary frequency reference 1 when multi-step speed operation is selected.
Refer to Multi-Step Speed Selection on
for details.
Setting 3: Auxiliary Reference 2
Sets the auxiliary frequency reference 2 when multi-step speed operation is selected.
Refer to Multi-Step Speed Selection on
for details.
Setting B: PI Feedback
Supplies the PI feedback value. This setting requires PI operation to be enabled in b5-01.
Setting C: PI Setpoint
Supplies the PI setpoint value and makes the frequency reference selected in parameter b1-01 no longer the PI setpoint. PI
operation to be enabled in b5-01 to use this setting.
Setting D: Frequency Bias
The input value of an analog input set to this function will be added to the frequency reference. This function can be used with
any frequency reference source.
Setting E: Motor Temperature
In addition to motor overload fault detection oL1, it is possible to use a PTC (Positive Temperature Coefficient) thermistor
for motor insulation protection.
Setting F: Through Mode
When set to F, an input does not affect any drive function, but the input level can still be read out by a PLC via APOGEE
FLN, BACnet, MEMOBUS/Modbus, or Metasys N2 communications.
Setting 16: Differential PI Feedback
If an analog value is set for this function, the PI controller is set for differential feedback. The difference of the PI feedback
input value and the differential feedback input value builds the feedback value used to calculate the PI input.
n
H5-01: Drive Slave Address
Sets the drive slave address used for communications.
Note:
Cycle power for the setting to take effect.
No.
Name
Setting Range
Default
H5-01
Drive Slave Address
0 to FFH
1FH
Each slave drive must be assigned a unique slave address for serial communications to work. Slave addresses do not need to
be assigned in sequential order, but no two drives may share the same address.
n
H5-02: Communication Speed Selection
Sets the communications speed for APOGEE FLN, BACnet, MEMOBUS/Modbus, and Metasys N2.
Note:
1.
Cycle power for the setting to take effect.
2.
When Metasys N2 communications are selected (H5-08 = 1), selecting a baud rate other than 9600 bps will trigger an oPE29 error.
3.
When APOGEE FLN (P1) communications are selected (H5-08 = 2), selecting a baud rate other than 4800 bps will trigger an oPE29
error.
4.
When BACnet communications are selected (H5-08 = 3), selecting 115200 bps (Setting 8) will trigger an oPE29 error.
No.
Name
Setting Range
Default
H5-02
Communication Speed Selection
0 to 8
4.13 Advanced Drive Setup Adjustments
178
YASKAWA ELECTRIC TOEP C710616 45F YASKAWA AC Drive – Z1000 User Manual
Summary of Contents for Z1000 CIMR-ZU*A Series
Page 399: ......