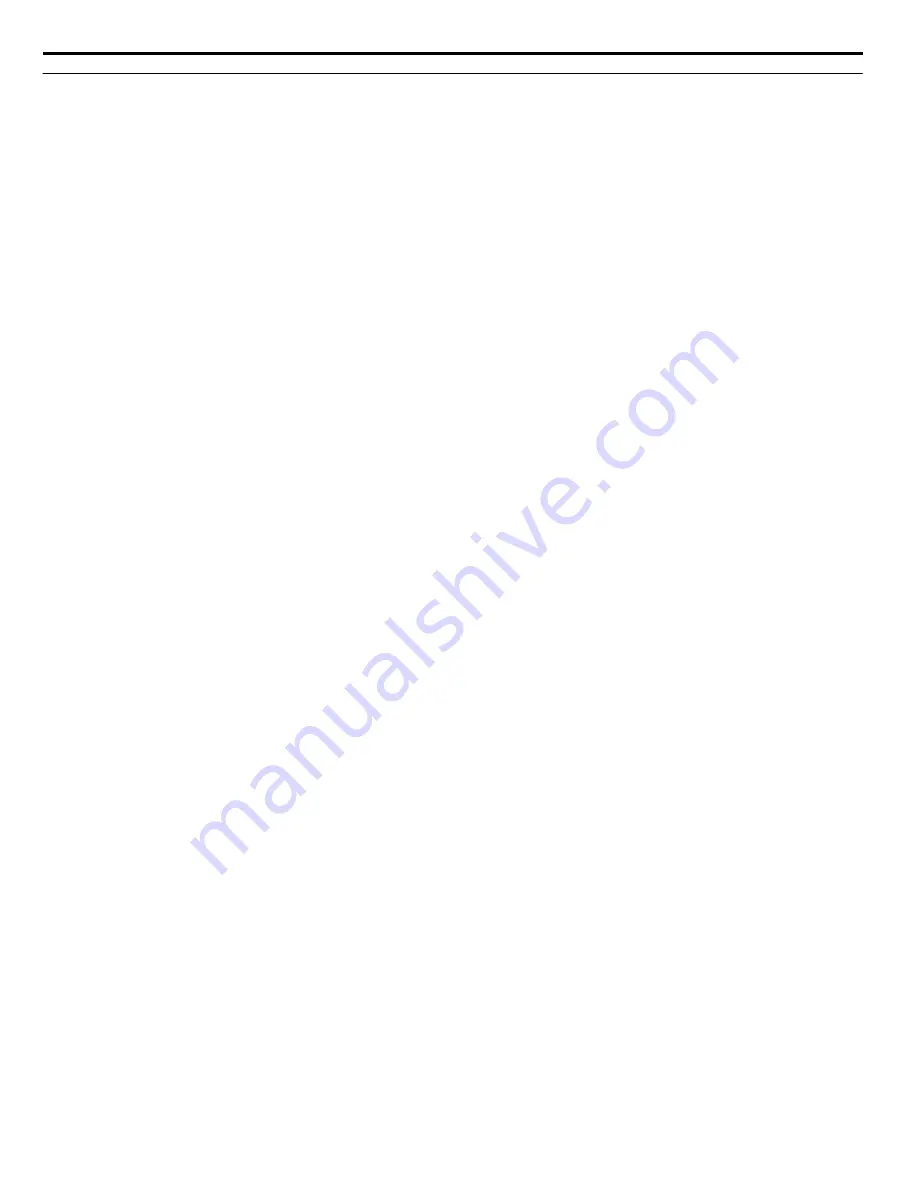
u
Copy Function
Parameter settings can be copied to another drive to simplify parameter restoration or multiple drive setup. The drive supports
the following copy options:
•
HOA Keypad (standard in all models)
The HOA keypad used to operate the drive supports copying, importing, and verifying parameter settings.
•
USB Copy Unit and CopyUnitManager
The copy unit is an external option connected to the drive to copy parameter settings from one drive and save those settings
to another drive. Refer to the manual supplied with the USB Copy Unit for instructions.
The CopyUnitManager is a PC software tool. It allows the user to load parameter settings from the Copy Unit onto a PC,
or from the PC onto a Copy Unit. This is useful when managing parameters for various drives or applications. Refer to the
manual supplied with the CopyUnitManager for instructions.
4.11 Verifying Parameter Settings and Backing Up Changes
154
YASKAWA ELECTRIC TOEP C710616 45F YASKAWA AC Drive – Z1000 User Manual
Summary of Contents for Z1000 CIMR-ZU*A Series
Page 399: ......