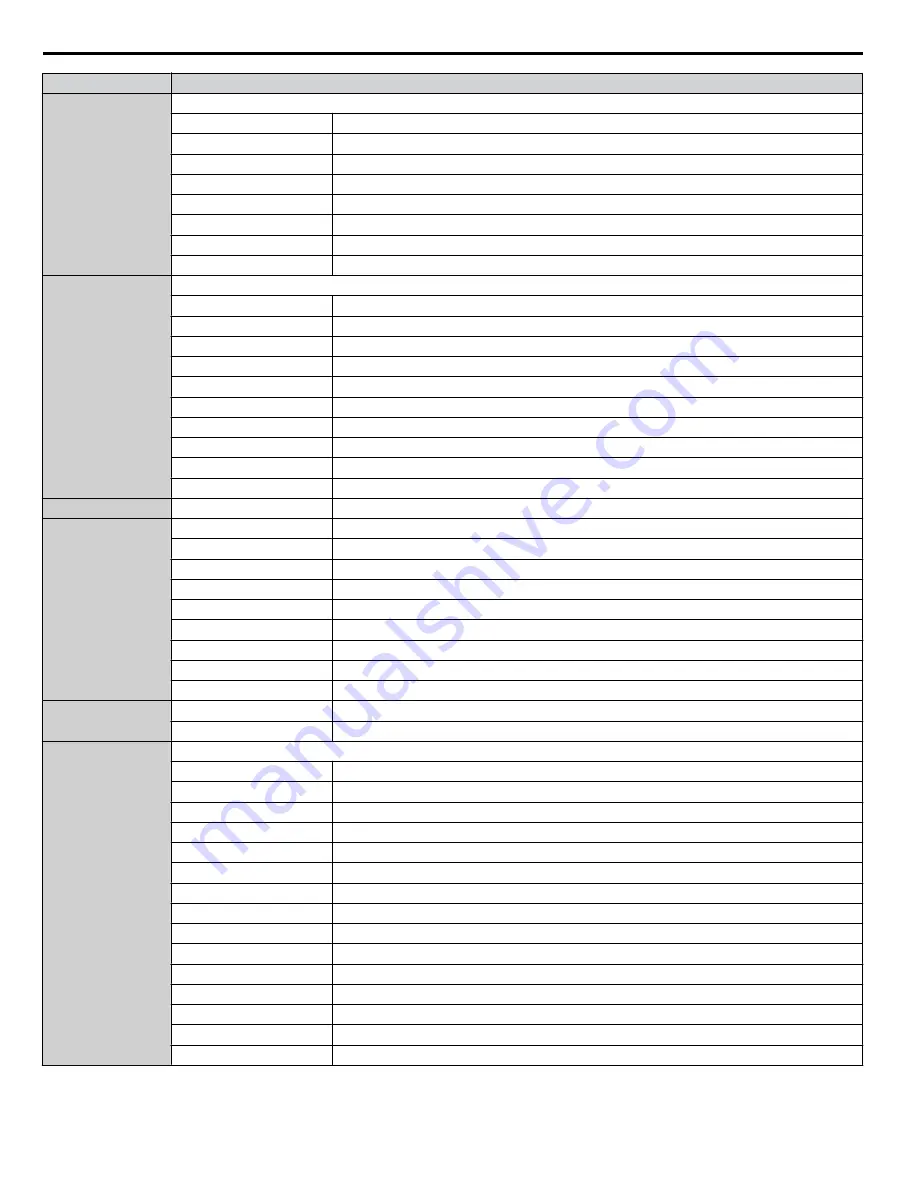
Register No.
Contents
00C3H
Fault contents 6
bit 0 to 4
Reserved
bit 5
Output Current Imbalance (LF2)
bit 6
Pullout Detection (STo)
bit 7
Reserved
bit 8
MECHATROLINK Watchdog Timer Error (E5)
bit 9
Reserved
bit A
Too many speed search restarts (SEr)
bit B to F
Reserved
00C4H
Fault contents 7
bit 0
Reserved
bit 1
Pump Fault 1, input terminal S1 (EF1)
bit 2
Pump Fault 2, input terminal S2 (EF2)
bit 3
Mechanical Weakening Detection 1 (oL5)
bit 4
Mechanical Weakening Detection 2 (UL5)
bit 5
Current Offset Fault (CoF)
bit 6
Reserved
bit 7
Reserved
bit 8
Reserved
bit 9 to F
Reserved
00C5H
bit 9
Underload Detection 6 (UL6)
00C6H
bit 0
Loss of Prime (LOP)
bit 3
Low Feedback (LFB)
bit 4
High Feedback (HFB)
bit 5
Setpoint Not Met (NMS)
bit 6
Pump Over Cycle (POC)
bit 8
Net Master Lost (MSL)
bit A
Anti-Jam Fault (AJF)
bit C
Wire Break (FDBKL)
bit F
Low Water Level (LWL)
00C7H
bit 0
High Water Level (HWL)
bit 4
Volute-TStat Flt (VLTS)
00C8H
Alarm contents 2
bit 0
Undervoltage (Uv)
bit 1
Overvoltage (ov)
bit 2
Heatsink Overheat (oH)
bit 3
Drive Overheat (oH2)
bit 4
Overtorque 1 (oL3)
bit 5
Overtorque 2 (oL4)
bit 6
Run Commands Input Error (EF)
bit 7
Drive Baseblock (bb)
bit 8
Pump Fault 3, input terminal S3 (EF3)
bit 9
Pump Fault 4, input terminal S4 (EF4)
bit A
Pump Fault 5, input terminal S5 (EF5)
bit B
Pump Fault 6, input terminal S6 (EF6)
bit C
Pump Fault 7, input terminal S7 (EF7)
bit D, E
Reserved
bit F
Overspeed (oS)
C.10 MEMOBUS/Modbus Data Table
408
YASKAWA
TOEP YAIQPM 03B YASKAWA AC Drive - iQpump Micro User Manual
Summary of Contents for iQpump Micro CIMR-PW Series
Page 443: ......