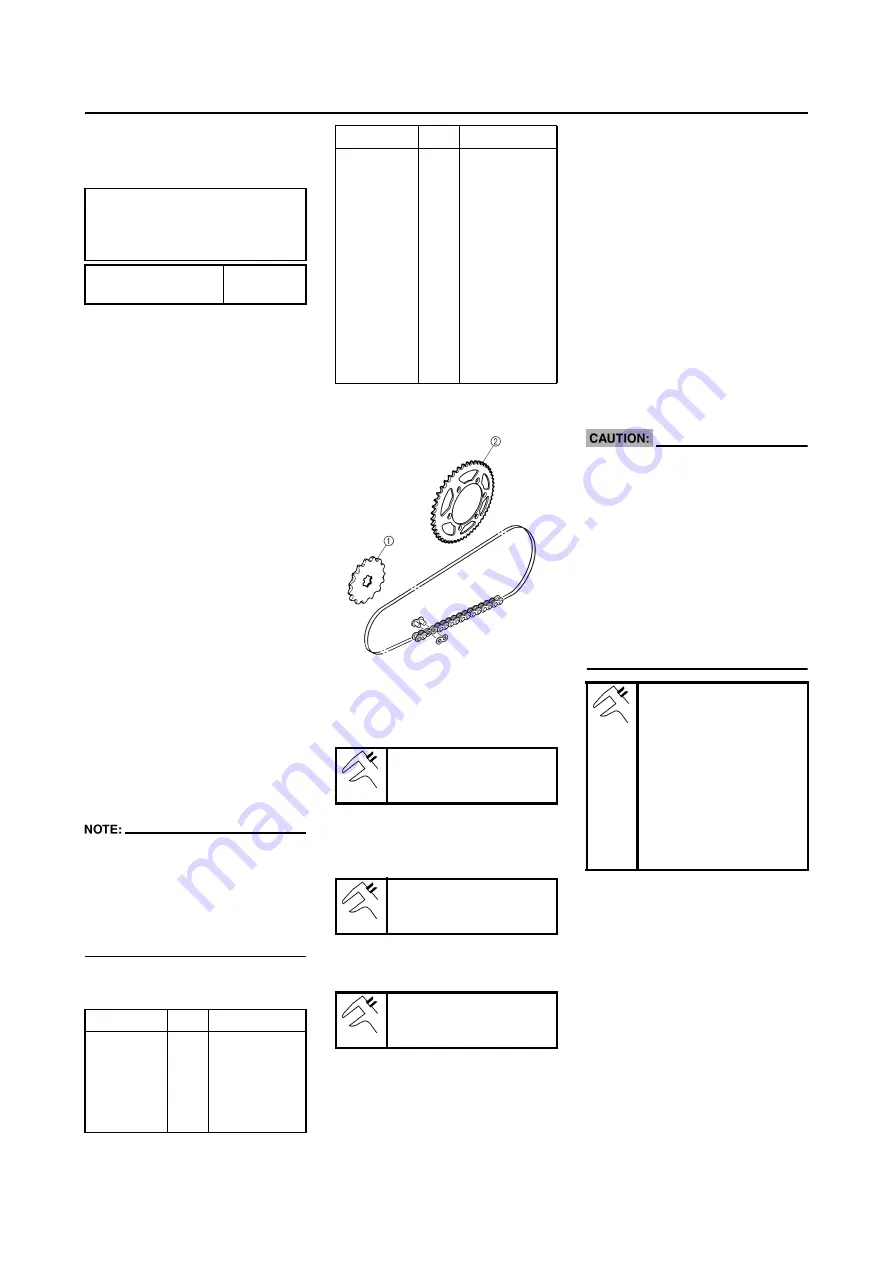
4-5
CHASSIS
CHASSIS
SELECTION OF THE SECONDARY
REDUCTION RATIO (SPROCKET)
<Requirement for selection of sec-
ondary gear reduction ratio>
•
It is generally said that the second-
ary gear ratio should be reduced for
a longer straight portion of a speed
course and should be increased for
a course with many corners. Actual-
ly, however, as the speed depends
on the ground condition of the day
of the race, be sure to run through
the circuit to set the machine suit-
able for the entire course.
•
In actuality, it is very difficult to
achieve settings suitable for the en-
tire course and some settings may
be sacrificed. Thus, the settings
should be matched to the portion of
the course that has the greatest ef-
fect on the race result. In such a
case, run through the entire course
while making notes of lap times to
find the best balance; then, deter-
mine the secondary reduction ratio.
•
If a course has a long straight por-
tion where a machine can run at
maximum speed, the machine is
generally set such that it can devel-
op its maximum revolutions toward
the end of the straight line, with care
taken to avoid the engine over-rev-
ving.
Riding technique varies from rider to
rider and the performance of a ma-
chine also vary from machine to ma-
chine. Therefore, do not imitate other
rider's settings from the beginning but
choose your own setting according to
the level of your riding technique.
DRIVE AND REAR WHEEL
SPROCKETS SETTING PARTS
TIRE PRESSURE
Tire pressure should be adjust to suit
the road surface condition of the cir-
cuit.
•
Under a rainy, muddy, sandy, or
slippery condition, the tire pressure
should be lower for a larger area of
contact with the road surface.
•
Under a stony or hard road condi-
tion, the tire pressure should be
higher to prevent a flat tire.
FRONT FORK SETTING
The front fork setting should be made
depending on the rider's feeling of an
actual run and the circuit conditions.
The front fork setting includes the fol-
lowing three factors:
1. Setting of air spring characteris-
tics
•
Change the fork oil level.
2. Setting of spring preload
•
Change the spring.
•
Install the adjustment washer.
3. Setting of damping force
•
Change the compression damp-
ing.
•
Change the rebound damping.
The spring acts on the load and
the damping force acts on the
cushion travel speed.
CHANGE IN LEVEL AND
CHARACTERISTICS OF FORK OIL
Damping characteristic near the final
stroke can be changed by changing
the fork oil amount.
Adjust the oil level in 5 mm (0.2 in)
increments or decrements. Too
low oil level causes the front fork
to produce a noise at full rebound
or the rider to feel some pressure
on his hands or body. Alternative-
ly, too high oil level will develop
unexpectedly early oil lock with
the consequent shorter front fork
travel and deteriorated perfor-
mance and characteristics. There-
fore, adjust the front fork within
the specified range.
Secondary reduction ratio =
Number of rear wheel sprocket
teeth/Number of drive sprocket
teeth
Standard secondary
reduction ratio
50/13
(3.846)
Part name
Size
Part number
Drive
sprocket
"1"
(STD) 13T 9383E-13233
* 14T 9383E-14215
* For AUS and NZ
Part name
Size
Part number
Rear wheel
sprocket
"2"
48T 5GS-25448-50
* 48T 1C3-25448-00
* 49T 1C3-25449-00
(STD) 50T 5TJ-25450-80
* (STD) * 50T 1C3-25450-00
* 51T 1C3-25451-00
52T 5TJ-25452-80
* 52T 1C3-25452-00
* For AUS and NZ
Standard tire pressure:
100 kPa (1.0 kgf/cm
2
,
15 psi)
Extent of adjustment:
60–80 kPa (0.6–0.8 kgf/
cm
2
, 9.0–12 psi)
Extent of adjustment:
100–120 kPa (1.0–1.2
kgf/cm
2
, 15–18 psi)
Standard oil level:
132 mm (5.20 in)
*125 mm (4.92 in)
Extent of adjustment:
95–150 mm (3.74–5.91
in)
From top of outer tube
with inner tube and
damper rod fully com-
pressed without
spring.
* For AUS, NZ and ZA
Summary of Contents for WR450Fv2008
Page 2: ......
Page 43: ...2 18 TIGHTENING TORQUES ...
Page 45: ...2 20 LUBRICATION DIAGRAMS 1 Intake camshaft 2 Exhaust camshaft A To main axle B From oil pump ...
Page 69: ...3 16 ENGINE INTAKE EXHAUST ...
Page 82: ...3 29 ELECTRICAL Charging method using a variable voltage charger ...
Page 83: ...3 30 ELECTRICAL Charging method using a constant voltage charger ...
Page 114: ...5 20 CYLINDER HEAD 3 Install Bolt cylinder head 1 Bolt cylinder head 10 Nm 1 0 m kg 7 2 ft lb ...
Page 133: ...5 39 OIL PUMP 15 Oil pump drive shaft 1 16 Rotor housing 1 Order Part name Q ty Remarks ...
Page 197: ...6 40 REAR SHOCK ABSORBER 8 Install Plastic band Taillight coupler Locking tie ...
Page 205: ...7 8 ELECTRIC STARTING SYSTEM 2 Inspect Rubber part a Tears damage Replace ...
Page 219: ......