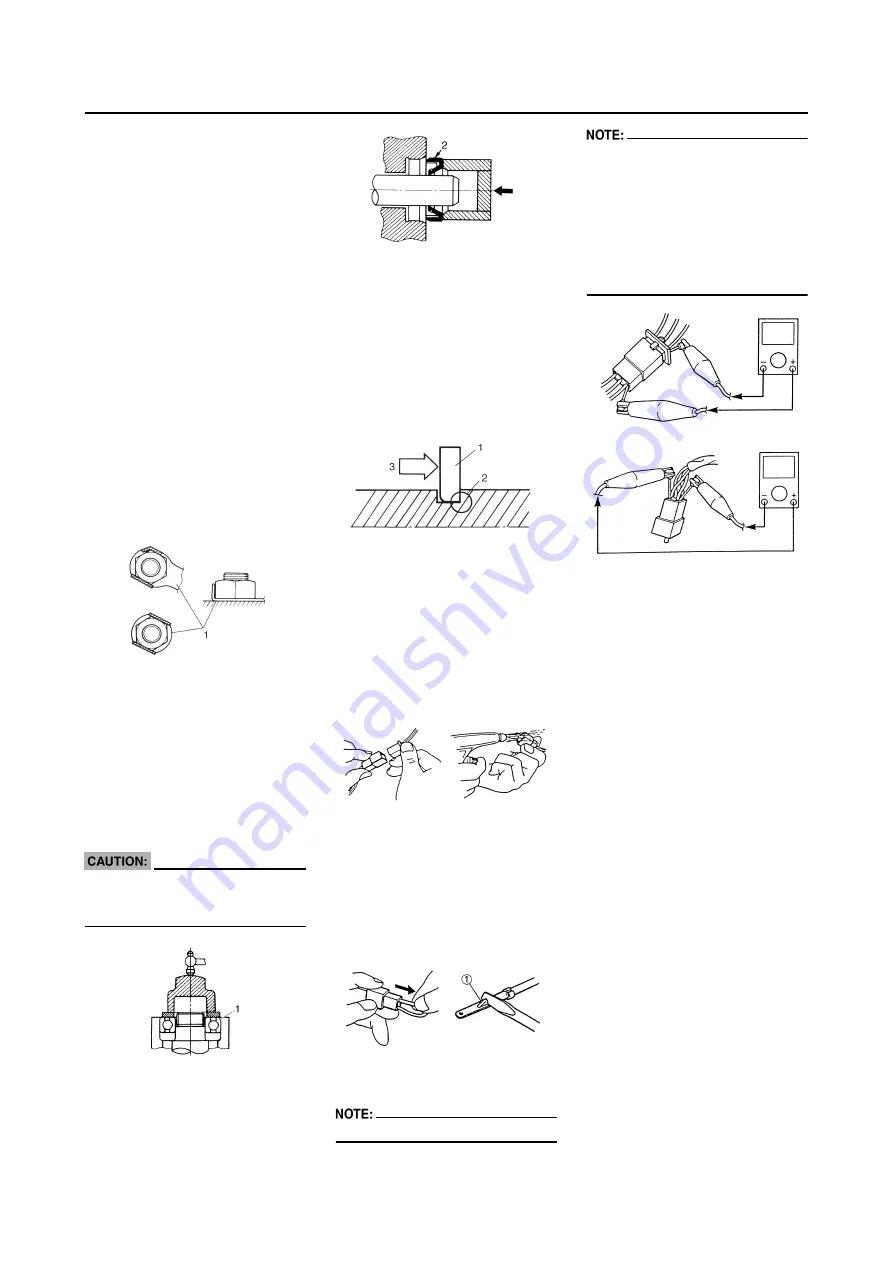
1-3
CHECKING OF CONNECTION
ALL REPLACEMENT PARTS
1. We recommend to use Yamaha
genuine parts for all replace-
ments. Use oil and/or grease rec-
ommended by Yamaha for
assembly and adjustment.
GASKETS, OIL SEALS AND O-
RINGS
1. All gaskets, oil seals, and O-rings
should be replaced when an en-
gine is overhauled. All gasket sur-
faces, oil seal lips, and O-rings
must be cleaned.
2. Properly oil all mating parts and
bearings during reassembly. Ap-
ply grease to the oil seal lips.
LOCK WASHERS/PLATES AND
COTTER PINS
1. All lock washers/plates "1" and
cotter pins must be replaced
when they are removed. Lock
tab(s) should be bent along the
bolt or nut flat(s) after the bolt or
nut has been properly tightened.
BEARINGS AND OIL SEALS
1. Install the bearing(s) "1" and oil
seal(s) "2" with their manufactur-
er's marks or numbers facing out-
ward. (In other words, the
stamped letters must be on the
side exposed to view.) When in-
stalling oil seal(s), apply a light
coating of lightweight lithium base
grease to the seal lip(s). Oil the
bearings liberally when installing.
Do not use compressed air to spin
the bearings dry. This causes dam-
age to the bearing surfaces.
CIRCLIPS
1. All circlips should be inspected
carefully before reassembly. Al-
ways replace piston pin clips after
one use. Replace distorted cir-
clips. When installing a circlip "1",
make sure that the sharp-edged
corner "2" is positioned opposite
to the thrust "3" it receives. See
the sectional view.
CHECKING OF
CONNECTION
Dealing with stains, rust, moisture,
etc. on the connector.
1. Disconnect:
•
Connector
2. Dry each terminal with an air
blower.
3. Connect and disconnect the con-
nector two or three times.
4. Pull the lead to check that it will
not come off.
5. If the terminal comes off, bend up
the pin "1" and reinsert the termi-
nal into the connector.
6. Connect:
•
Connector
The two connectors "click" together.
7. Check for continuity with a tester.
•
If there in no continuity, clean the
terminals.
•
Be sure to perform the steps 1 to 7
listed above when checking the
wire harness.
•
For a field remedy, use a contact re-
vitalizer available on the market.
•
Use the tester on the connector as
shown.
Summary of Contents for WR450Fv2008
Page 2: ......
Page 43: ...2 18 TIGHTENING TORQUES ...
Page 45: ...2 20 LUBRICATION DIAGRAMS 1 Intake camshaft 2 Exhaust camshaft A To main axle B From oil pump ...
Page 69: ...3 16 ENGINE INTAKE EXHAUST ...
Page 82: ...3 29 ELECTRICAL Charging method using a variable voltage charger ...
Page 83: ...3 30 ELECTRICAL Charging method using a constant voltage charger ...
Page 114: ...5 20 CYLINDER HEAD 3 Install Bolt cylinder head 1 Bolt cylinder head 10 Nm 1 0 m kg 7 2 ft lb ...
Page 133: ...5 39 OIL PUMP 15 Oil pump drive shaft 1 16 Rotor housing 1 Order Part name Q ty Remarks ...
Page 197: ...6 40 REAR SHOCK ABSORBER 8 Install Plastic band Taillight coupler Locking tie ...
Page 205: ...7 8 ELECTRIC STARTING SYSTEM 2 Inspect Rubber part a Tears damage Replace ...
Page 219: ......