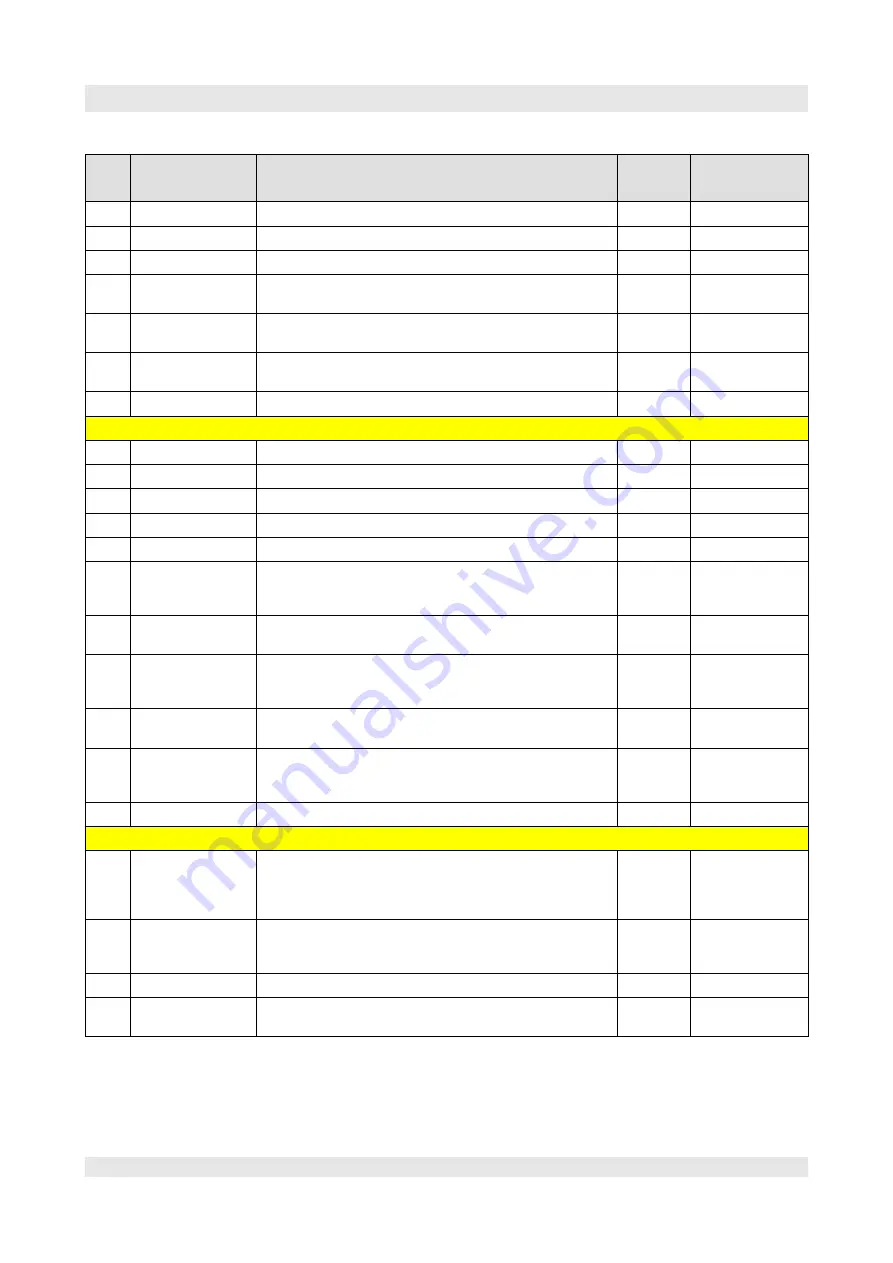
Manual-overview of system
No.
name
description
Factory
setup
scope
F250 ID No 3
Only read
F251 ID No 4
Only read
F252 ID No 5
Only read
F253
Inverter rated
current
Rated current inverter
x0.1A
Only read
F254
Rated current of
current sensor
Rated current of current sensor
A
Only read
F255
Motor power
coefficient
Max. rated output Power
200,00%
50~400%
F245=5 >> F246 bis F255 as follows:
F246 Stator Resistor
Stator resistance Asynchronous-motor
x0.001R
F247 Rotor Resistor
Rotor resistance Asynchronous-Motor
x0.001R
F248 Stator Inductor
Stator Induktivitiy Asynchronous-Motor
x0.0001H
F249 Rotor Inductor
Rotor Induktivitiy Asynchronous-Motor
x0.0001H
F250 Mutual Inductor
x0.0001H
F251
Motor low speed
overcurrent
threshold
Over-current limit for RPM below 20% of rated RPM
x0.1%
F252
Low speed
overcurrent time
Duration of Over-current for low RPM
x0.1s
F253
Motor high speed
overcurrent
threshold
Over-current limit for RPM above 20% of rated RPM
x0.1%
F254
High speed
overcurrent time
Duration of over-current for high RPM
x0.1s
F255
Frequency dividing
coefficient of
encoder
Divisor for encoder.Requires convinient board for encoder
with divisor
0
0~7
F245=6 >> F246 bis F255 as follows:
F246
Synchronous
motor study angle
when power on
Auto measurement of phase -angle after return of
synchronous motor.
0: deactivated 1: activated
Sshould be turned OFF, if phase-angel is known and set
1
0~1
F247
Current gain when
self study
Strenght of measurement current for phase -angle. Has to
be adopted for some montors. The less is better as to
much.
150,00%
0~400
F248 Command option
Option for run command
2
0~2
F249
Zero servo process
current loop gain
Hold-up current-normaly is not to change!
100,00%
48~65535
Seite 67