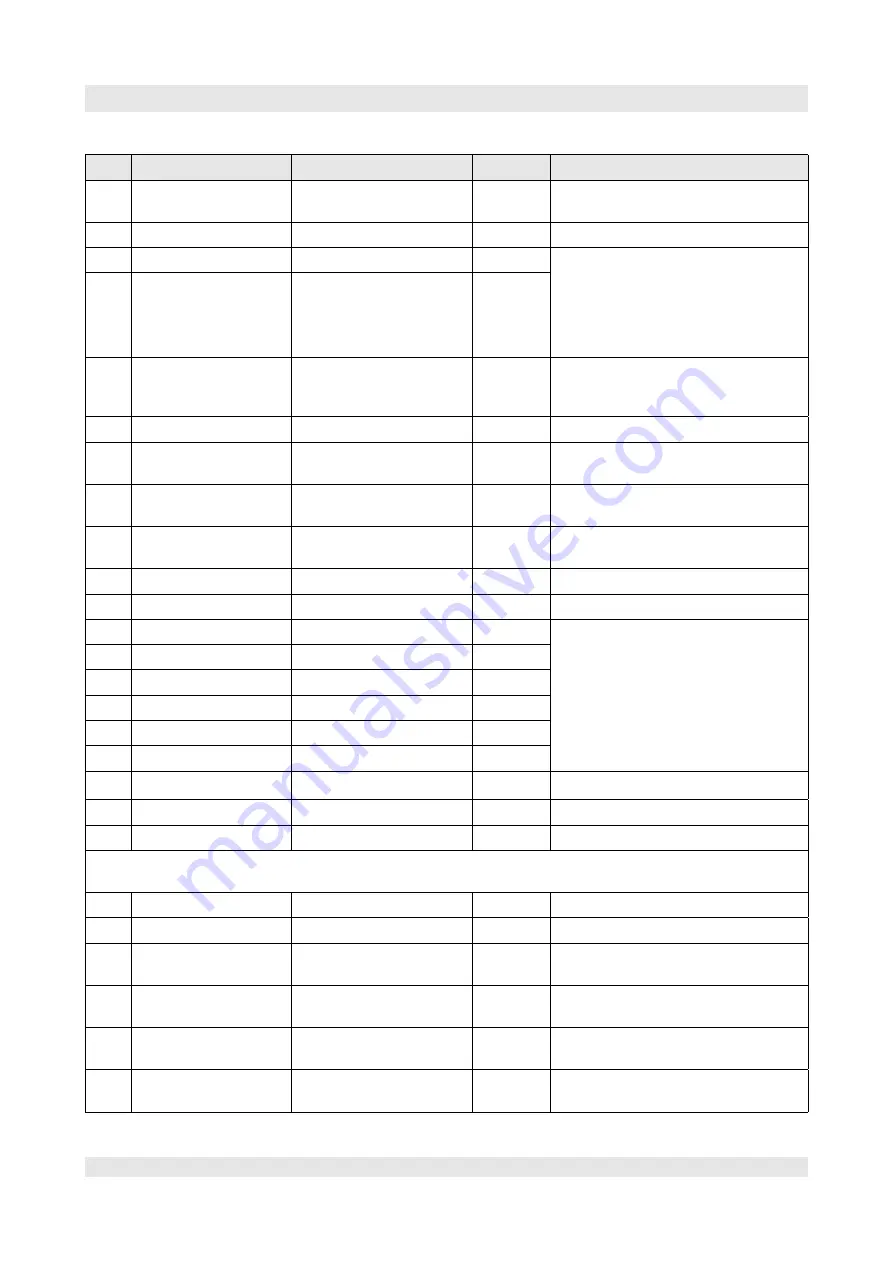
Manual-overview of system
Par.
name
Function
Setting
Remark
F59
Retardation brake off
Stoptime during start
0,5s
Came out as good compromise between
slight Rollback and fast Start .
F62
Running time limit.
Runningtime monitoring
32s
F76
Lim. UpDis. Ins.
End of insp. up
0mm
To avoid problems due to missing shaft
copying set on „0“. later there were
adopted not to run up into pre-end
switch Inspection and down not into
support.
F77
Lim. DnDis Ins.
End of insp. Down
0mm
F122
Retard. Run Insp
Retardation between Brake
OFF and running signals
0 – 1 s
Is only working when stopping by
pushing Auf and Ab during inspektion
F165
Door Kontr.Spez.
door open functionality
0
F175
Start creep-speed
Creep-speed during Start
0,006m/s
F180
Analog value->Vnen
Attribution speed to rated
speed
100,00%
Shouldn't be changed
F186
Duration of creep-speed
when Start
Duration of creep-speed
when Start
0,5s
F201
FU Modus
Inverter Modus
3
Vector Modus with encoder
F202
Motort Type
Motor Type
1
Synchronous-Motor
F203
M Rated Power
Rated motor power
4kW
This are values for
Torin
at 630kg/1m/s.
At 0,63m/s result a frquency of 16,67Hz
at a revolution of 100RPM!
In any doubt check type-plate.
F204
M Rated Current
Rated motor current
10,5A
F205
M Rated Freq
Rated motor frequency
26,25Hz
F206
M RPM
Rated motor revolution
159RPM
F207
M Rated Voltage
Rated motor tension
380V
F208
M Pole Num.
Numper of poles
20
F209
M Slip Freq
1.4 Hz
F210
Encoder Type
Type of encoder
2
EnDat
F211
Encoder Pulses
Number of pulses encoder
2048
F212 to F226 are for the revolution controller and so for die running quality. See also description „Parameter
Drehzahlregler“
F227
Brake Time
Retard brake fall in
0,2s
F228
Curr. Descent T
Time for demagetisation
0,3s
Should be ok to avoid „knack“ after stop.
F232
Encoder.Filter.Time
Time for filter
encodersignal
1ms
1ms proved as ideal.
F233
Enc. Direction
Sense of rotation encoder
1
Has to be at 1 If OC Error or jumping
after tuning. Change motorphase!
F234
Motor Phase
Adoption direc of rotation
motor
1
If Auf and Ab doesn't correspond with
direction of cabine-set on 0.
F239
Output-Torq Lmt
torque limit
175,00%
Could be raised ev. Up to 200%
Seite 21