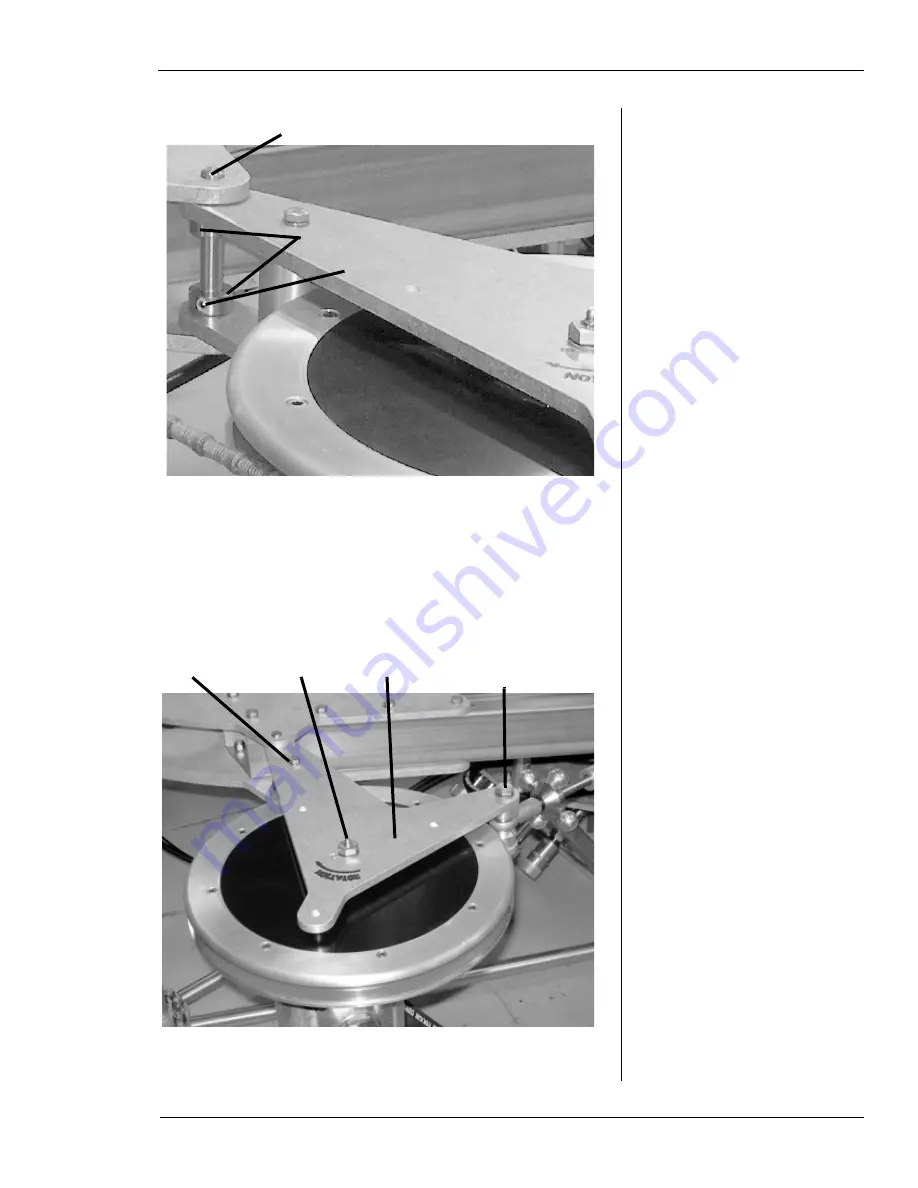
Chapter 4, Maintenance: Replacing the Wheel Liners
E.H. Wachs
Part No. 10-010-MAN, Rev. 1-0310
47
Figure 4-17. Loosen the set screws in the stop collars
to remove the pivot pin.
3.
Remove the nut from the bolt holding the wheel
assembly to the tension rod, then remove the bolt. The
wheel and motor assembly will be free from the saw
bow.
Figure 4-18. Remove the nut (on the bottom) of the
tension rod mounting bolt, and remove the bolt.
Pivot pin
Stop collars
Set screw
Tension rod
mounting bolt
Hub bolt
Spacer bolt
Top plate
Summary of Contents for WS-8460
Page 2: ...Diamond Wire Saw User s Manual Part No 10 010 MAN Rev 1 0310 E H Wachs...
Page 18: ...Diamond Wire Saw User s Manual 14 Part No 10 010 MAN Rev 1 0310 E H Wachs A B C...
Page 22: ...Diamond Wire Saw User s Manual 18 Part No 10 010 MAN Rev 1 0310 E H Wachs...
Page 40: ...Diamond Wire Saw User s Manual 36 Part No 10 010 MAN Rev 1 0310 E H Wachs...