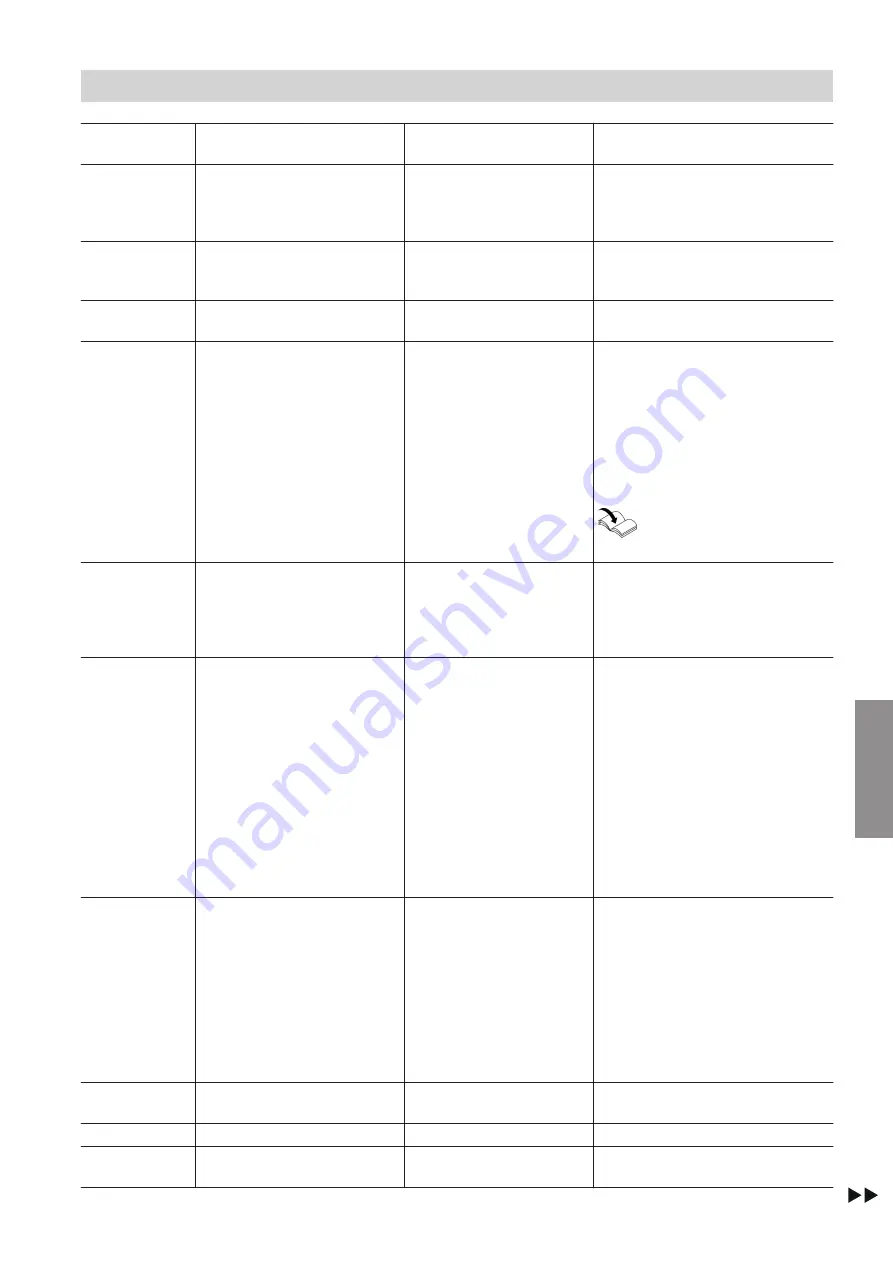
123
Displayed fault
code
System characteristics
Cause
Measures
A1
Burner locked out
Combustion chamber
overfilled
Firebed light barrier is in-
terrupted
Clean combustion chamber and re-
start boiler
A2
Burner locked out
Fault, burn-back: Feed
tube hot
■
Check ash box position
■
Check air dampers
■
Check the boiler for leaks
A3
Burner locked out
Fault, light barrier, firebed
monitoring
Clean light barrier and sight glass
A4
Burner locked out
Fault, material shortage
■
Check fuel store fill level
■
Manual charging: Check fill level
of day hopper
■
Pellet supply with vacuum sys-
tem: Check the output stage of
the vacuum module
If necessary, set a higher output
stage at the vacuum module
Installation and service in-
structions, vacuum module
A5
Burner locked out
Fault, material shortage
due to time-out
The blocking time set for
the vacuum module is too
long
Adjust the vacuum module block-
ing time in the control unit
The fault is cleared after the block-
ing time and the boiler is started
A6
Burner locked out
Ash box full
■
Emptying the ash box
■
Confirm message "Has the ash
box been emptied?"
Note
The ash box fill level can be reset
manually as follows:
1.
å
for
"Menu"
.
2.
|
/
~
to select.
3. Confirm
"Information"
with
d
.
4.
|
/
~
to select.
5. Confirm
"Reset data"
with
d
.
AA
Burner locked out
Boiler had excess temper-
ature
■
Check set values in control unit
■
Check pump
■
Check valves
■
Check sensors
Note
For resetting the high limit safety
cut-out, see chapter "Maintenance,
high limit safety cut-out"
AB
Burner locked out
Water pressure is too low
Check for water shortage and wa-
ter pressure
AC
Burner locked out
Water pressure is too high Check water pressure
AD
Burner locked out
Fault, flue gas filter
Check the fault on the external
control unit
Troubleshooting
Fault codes
(cont.)
5679249
Diagnosis