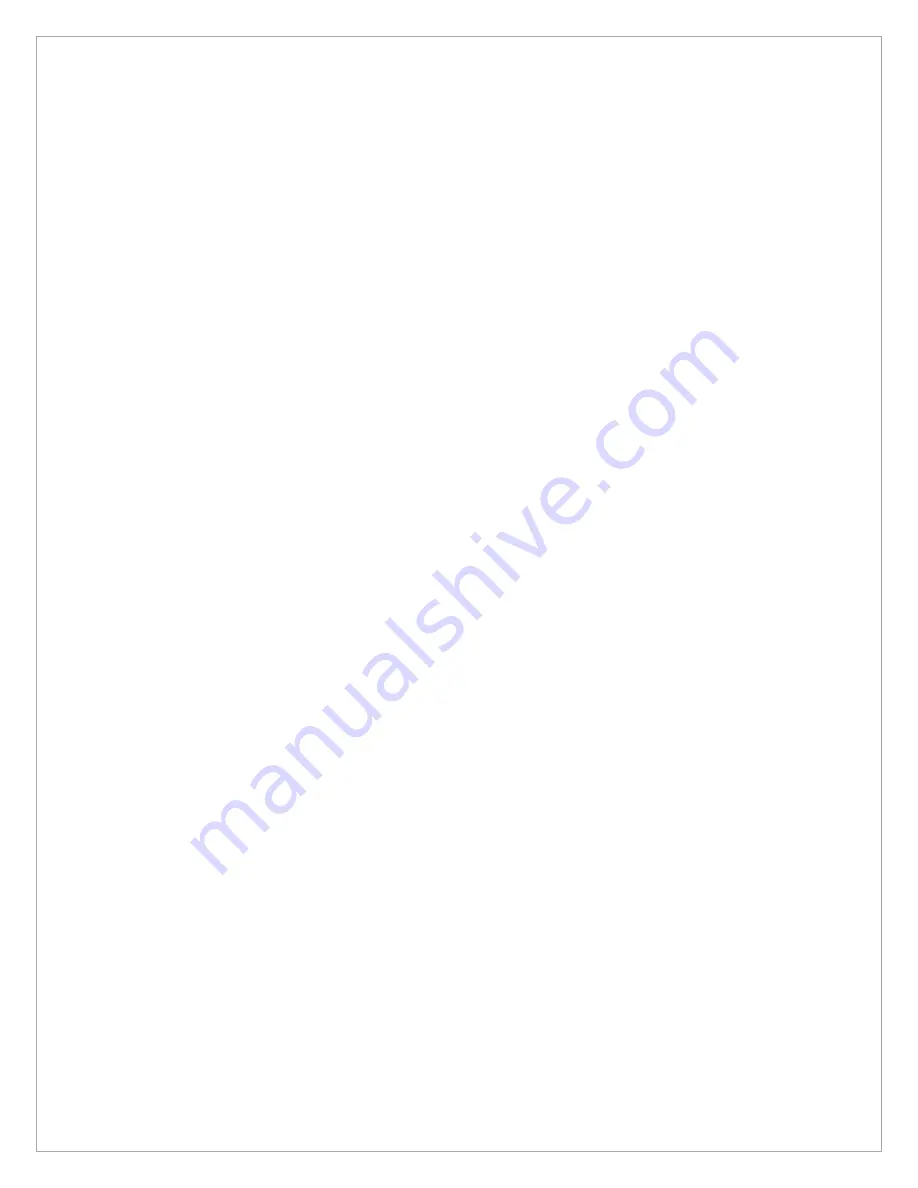
VersaPro Temperature Controller
Page 57
Copyright © 2013, United Process Controls Inc.
All rights to copy, reproduce and transmit are reserved
18
Troubleshooting Questions
This section is organized alphabetically by the functional name of various instrument operations and features.
Some explanations may be listed in more than one category since the problem can be approached from
several different points of view. Each problem is presented as a question for typical problems that may be
encountered. In most cases the problem can be resolved by changing a setup parameter in the instrument.
18.1 Analog
Inputs
How come the display flashes HHHH or LLLL when I try to read a signal at input A or input B in linear
mode?
There are possibly two reasons; the decimal point setting in the Calc menu has to be adjusted for the
maximum signal level to be read or the signal level has exceeded the range of the input channel. Channel A is
set up primarily for thermocouple levels from –10mV to 70mV. Channel B is set up for oxygen sensor millivolt
ranges of 0 to 2000 mV. The display decimal point setting will not truncate the input value, it just increases the
resolution of the input signal. If the value is within the input range of the channel but greater than or less than
the possible display setting then the limit warnings will flash on the display.
How come I can’t see the linear reading on my controller / monitor?
It is necessary to change the decimal point in the Calc setup menu.
I am trying to offset the temperature using the offset and scaling number in the Input menu but the
temperature does not change.
The input offset and scaling numbers for inputs A and B only work if either Linear A or Linear B are selected as
the process source in the Control Menu. If it is necessary to offset the temperature slightly it is possible to do
this by changing the cold junction trim adjustment in the Input Calibration menu. It is not recommended that
the actual linear calibration values for input A are changed.
18.2 Control
Outputs
I have a dual contact control mode selected but my second contact does not work.
When a dual control mode is selected it is necessary to also set the high percent output (HIPO) and low
percent output (LOPO). In single time proportioning, the default mode, the HIPO is 100 and the LOPO is 0.
When a dual mode is selected it is necessary to change the LOPO to –100. In the case of carbon control it is
typically required to control gas and air. The first control contact would be connected to the gas solenoid and
the second control contact would be connected to the air solenoid. The gas solenoid would be turn on all the
time when the control output goes to 100%. Likewise the air solenoid would be on all the time if the control
output was –100%.
When would I change my HIPO or LOPO settings to something other then the 100% or –100%?
These values rarely have to be changed but one case that requires it is when the control actuator is not acting
an expected linear fashion. An example would be an SCR driving a heater. If the SCR is not actually turning
on until the control signal is at 20% and stops increasing at 80% then the linear response of the actuator is
only between 20% and 80%. If the controller assumes the full output range of 0 to 100% then a large delay in
process reaction will drive the reset function in the PID control calculation into oscillation. It would be
necessary to set the LOPO to 20% and the HIPO to 100% to achieve stable control.