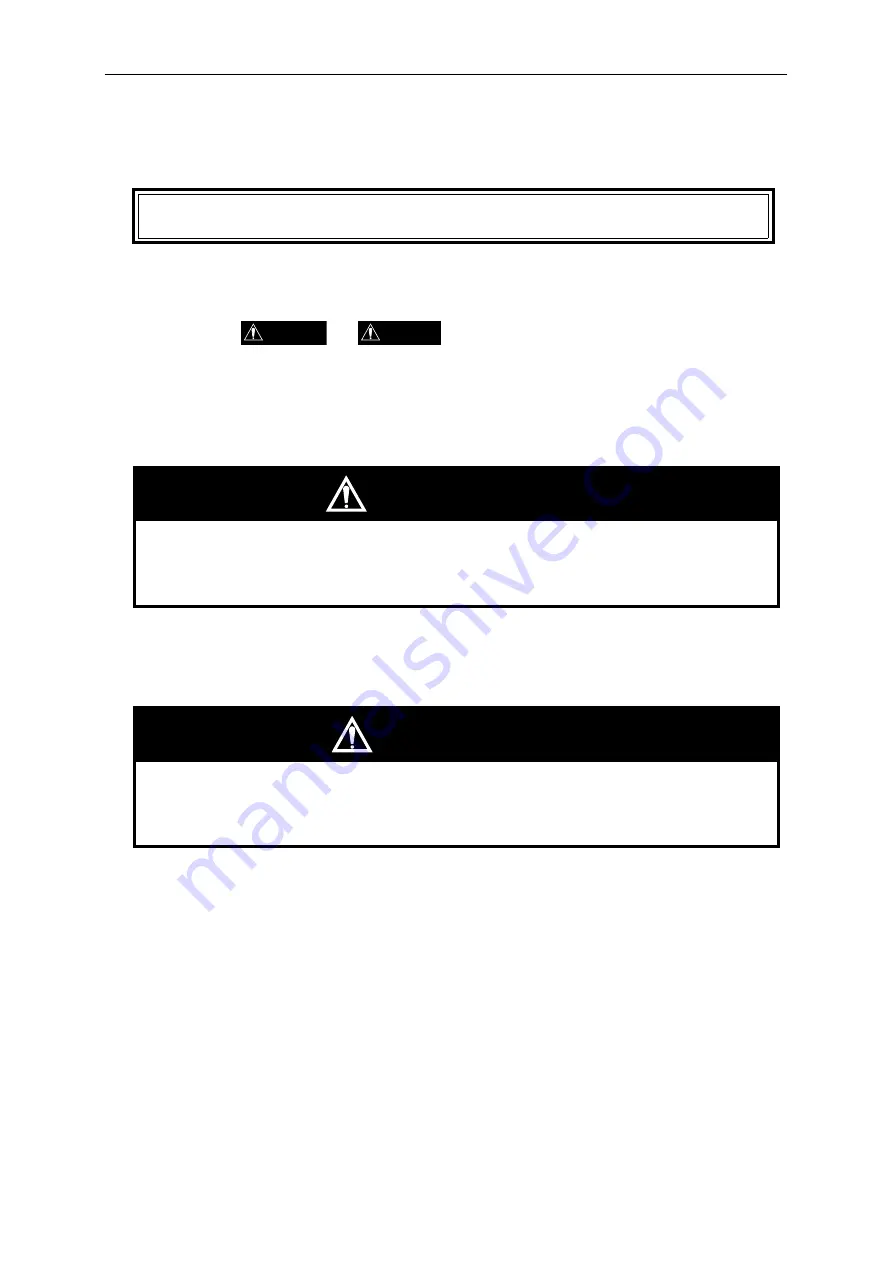
Safety Precautions
Safety Precautions
Be sure to read for safety.
In order to have an F159 Weight Module used safely, notes I would like you to surely follow
divide into
and
, and are indicated by the following documents.
Notes indicated here are the serious contents related to safety. Please use F159 after
understanding the contents well.
WARNING
CAUTION
WARNING
Misuse may cause the risk of death or serious
injury to persons.
CAUTION
Misuse may cause the risk of injury to persons
or damage to property.