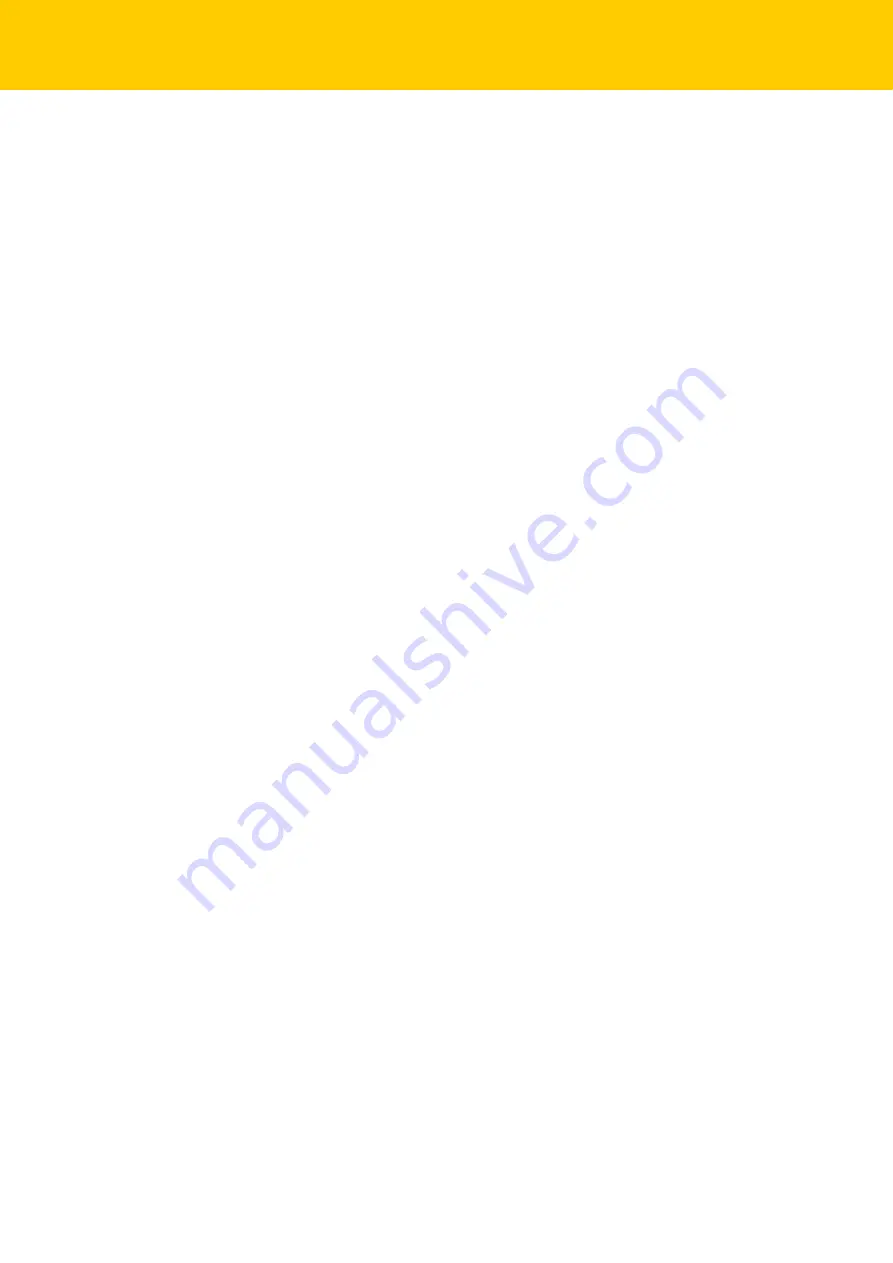
Product description
Hans Turck GmbH & Co. KG | T +49 208 4952-0 | F +49 208 4952-264 | [email protected] | www.turck.com
20
3.5
Safe I/O channels
The device provides two 2-channel safe digital inputs (FDI) and two safe connectors (FDX), configu-
rable as in- or outputs.
The two configurable FDX-channels can be used as input (FDI) or as output (FDO).
The safe I/O channels are designed for applications up to:
Cat4/PLe according to EN ISO 13849-1,
SIL3 according to IEC 61508,
SILCL 3 according to IEC62061.
3.5.1
Safe Status
In the safe state the device outputs are in LOW-state (0).
The inputs report a LOW-state (0) to the logic.
3.5.2
Fatal Error
The following errors lead to Fatal Error and thus to the safe state:
Incorrect wiring at the output (e.g. capacitive load, energetic recovery)
Incorrect power supply
Strong EMC disturbances
Internal device error
Summary of Contents for TBIP-L...-FDIO1-2IOL Series TBIP-L4-FDIO1-2IOL
Page 1: ...Your Global Automation Partner TBIP L FDIO1 2IOL Safety Block I O Module Instructions for Use...
Page 2: ...2 Hans Turck GmbH Co KG T 49 208 4952 0 F 49 208 4952 264 more turck com www turck com...
Page 118: ...Hans Turck GmbH Co KG T 49 208 4952 0 F 49 208 4952 264 more turck com www turck com 2...