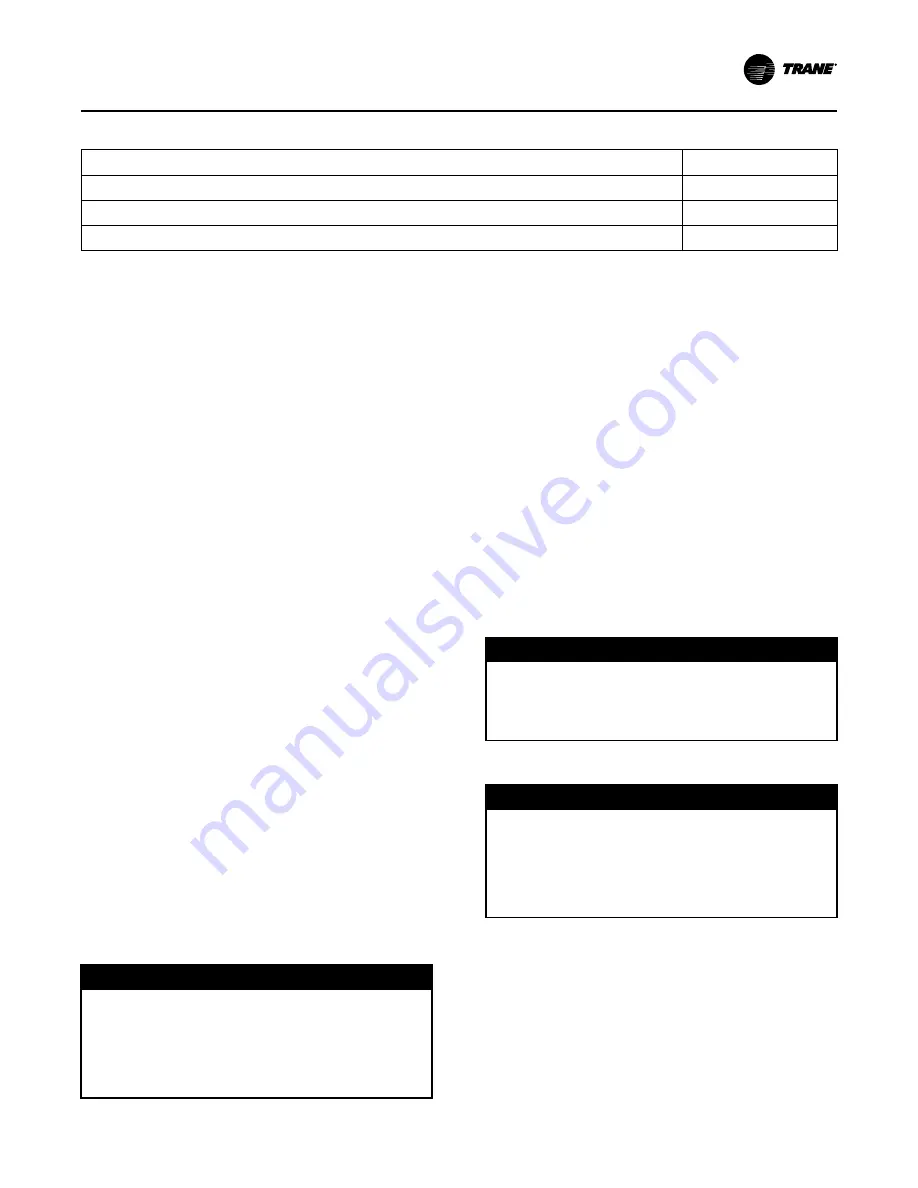
ARTC-SVX005B-EN
59
Table 14.
Recommended chiller service intervals (continued)
Task
Frequency
Confirm and record compressor amperage draw and voltage
Annually
Compare water/glycol flow against design specifications
Annually
Tighten compressor rotalock nuts
Annually
Weekly
Weekly inspection is a continuation and elaboration of
daily best practice:
•
Inspect touchscreen interface panel for alarm status
and additions to the alarm history. (Do not clear
alarms as this is a very important performance
record if troubleshooting problems occur.)
•
Listen for excessive vibrations or motor noise. This
usually signals a loose brace or section of piping.
•
Measure all refrigerant static pressure on any idle
circuits. Record any significant changes or
reductions in pressure.
•
Clean strainers weekly during initial weeks after
initial start up until water quality has been reliably
established. Thereafter, inspect and clean strainers
at least monthly .
Monthly
The monthly maintenance inspection examines many
items that generally require frequent attention. This
routine event identifies small problems early before
they can become big problems requiring serious repair
and refurbishment:
1. Remove the strainer on the inlet water pipe to the
chiller/heater and verify that it is clean and free of
debris.
2. The 30 Mesh screen is made of SAE Grade 304
stainless steel. Clean the interior of the end cap (or
service cap), and the gasket using a soft natural
bristle brush and tap water. If fine particles cannot
be removed with the water stream, use a mild
detergent and a non-abrasive brush to remove
them.
3. Check the compressor oil level sight glass. The oil
should always be clear and free-flowing. Any milky
or “slow rolling” effect indicates that liquid
refrigerant is making its way back into the
compressor and will cause premature compressor
failure.
N
NO
OT
TIIC
CE
E
E
Eq
qu
uiip
pm
me
en
ntt D
Da
am
ma
ag
ge
e!!
F
Fa
aiillu
urre
e tto
o rre
em
mo
ov
ve
e m
mo
oiissttu
urre
e ffrro
om
m ssy
ysstte
em
m cco
ou
ulld
d
cca
au
usse
e cco
orrrro
ossiio
on
n w
wiitth
hiin
n tth
he
e cch
hiilllle
err//h
he
ea
atte
err
cco
om
mp
po
on
ne
en
nttss,, a
an
nd
d d
de
eg
grra
ad
de
e p
pe
errffo
orrm
ma
an
ncce
e..
P
Pe
errffo
orrm
m v
va
accu
uu
um
m e
ev
va
accu
ua
attiio
on
n o
off ssy
ysstte
em
m tto
o rre
em
mo
ov
ve
e
m
mo
oiissttu
urre
e..
4. When the compressor is not operating, the oil level
should be at least at the bottom of the sight glass,
up to two-thirds full. When the compressor is
operating, the oil level will normally be at the
bottom of the sight glass, or even below, but it
must be visible.
5. Low oil sight glass conditions could signify an
undercharged chiller that lacks proper refrigerant
velocity to return oil to the compressor sump.
Eventually, dry compressor starts could occur
causing premature compressor failure. This may
indicate that some oil has been lost from a previous
refrigerant leak repair. The compressor data label
indicates the correct oil type and quantity with
which it should be filled.
N
No
otte
e:: A flashlight may be required to see the oil
churning in the sump of the compressor.
Adjusting the line of sight may be necessary to
visually inspect the oil in the compressor sump
during operation. At a minimum, the oil must be
seen churning in the compressor sump. It should
be clear.
N
NO
OT
TIIC
CE
E
C
Co
om
mp
prre
esssso
orr F
Fa
aiillu
urre
e!!
F
Fa
aiillu
urre
e tto
o ffo
ollllo
ow
w iin
nssttrru
uccttiio
on
nss b
be
ello
ow
w cco
ou
ulld
d rre
essu
ulltt iin
n
cca
atta
assttrro
op
ph
hiicc cco
om
mp
prre
esssso
orr ffa
aiillu
urre
e..
D
Do
o n
no
ott o
op
pe
erra
atte
e w
wiitth
h iin
nssu
uffffiicciie
en
ntt o
oiill..
6. Check the glycol concentration using a
refractometer.
N
NO
OT
TIIC
CE
E
C
Co
om
mp
prre
esssso
orr D
Da
am
ma
ag
ge
e!!
F
Fa
aiillu
urre
e tto
o ffo
ollllo
ow
w iin
nssttrru
uccttiio
on
nss b
be
ello
ow
w cco
ou
ulld
d rre
essu
ulltt iin
n
e
ex
xtte
en
nssiiv
ve
e cco
om
mp
prre
esssso
orr d
da
am
ma
ag
ge
e..
V
Ve
erriiffy
y tth
ha
att ssu
uccttiio
on
n p
prre
essssu
urre
e iiss ssu
uffffiicciie
en
ntt.. S
Se
eccu
urre
e
tth
he
e cciirrccu
uiitt o
orr m
mo
od
du
ulle
e o
offfflliin
ne
e u
un
nttiill sstta
attu
uss cca
an
n b
be
e
e
ex
xa
am
miin
ne
ed
d iin
n d
de
etta
aiill..
7. Check the refrigeration pressures.
8. For R410A refrigerant, low pressure refrigeration
gauge should read 120 to 160 psi and high pressure
refrigeration gauge should read 300 to 450 psi.
IIm
mp
po
orrtta
an
ntt:: Suction pressures below 90 psi (R410A) is a
clear sign of insufficient refrigerant charge,
low water flow, refrigeration obstruction, or
valve closed units running only water.