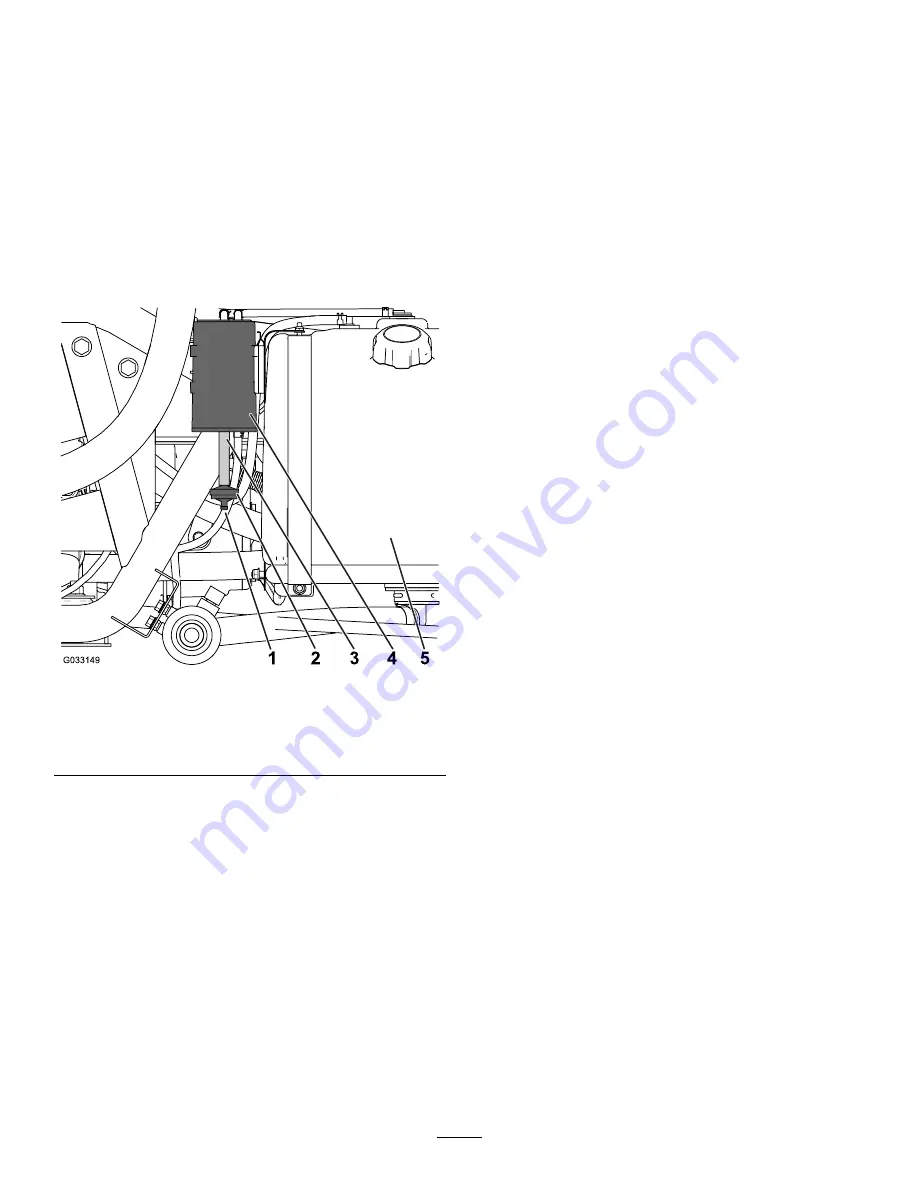
Servicing the Carbon
Canister
Checking the Air Filter for the
Carbon Canister
Service Interval:
After the first 50 hours
Every 200 hours
Check the opening at the bottom of the air filter for the
carbon canister to ensure that it is clean and free of
debris and obstructions (
).
g033149
Figure 42
1.
Air-filter opening
4.
Carbon canister
2.
Carbon-canister filter
5.
Fuel tank
3.
Hose
Replacing the Carbon-Canister
Filter
Service Interval:
After the first 50 hours
Every 200 hours
1.
Remove the barbed fitting of the carbon-canister
filter from the hose at the bottom of the carbon
canister, and remove the filter (
).
Note:
Discard the old filter.
2.
Fully insert the barbed fitting of the new
carbon-canister filter into the hose at the bottom
of the carbon canister.
Draining the Fuel Tank
Service Interval:
Every 400 hours/Yearly (whichever
comes first)
Drain and clean the fuel tank if the fuel system
becomes contaminated or if you plan to store the
machine for an extended period. Use fresh, clean fuel
to flush out the tank.
1.
Transfer the fuel from the tank into an approved
fuel container using a siphon pump, or remove
the tank from the machine and pour the fuel out
of the tank fill spout into the fuel container.
Note:
If you remove the fuel tank, also remove
the fuel and return hoses from the tank before
removing the tank.
2.
Replace the fuel filter; refer to
Fuel Filter (page 45)
.
3.
Flush the tank with fresh, clean fuel, if necessary.
4.
Install the tank if you removed it.
5.
Fill the tank with fresh, clean fuel.
46
Summary of Contents for Multi Pro 1750
Page 72: ...Schematics g028078 Sprayer System Schematic Rev DWG 125 0698 Rev B 72...
Page 73: ...Notes...
Page 74: ...Notes...