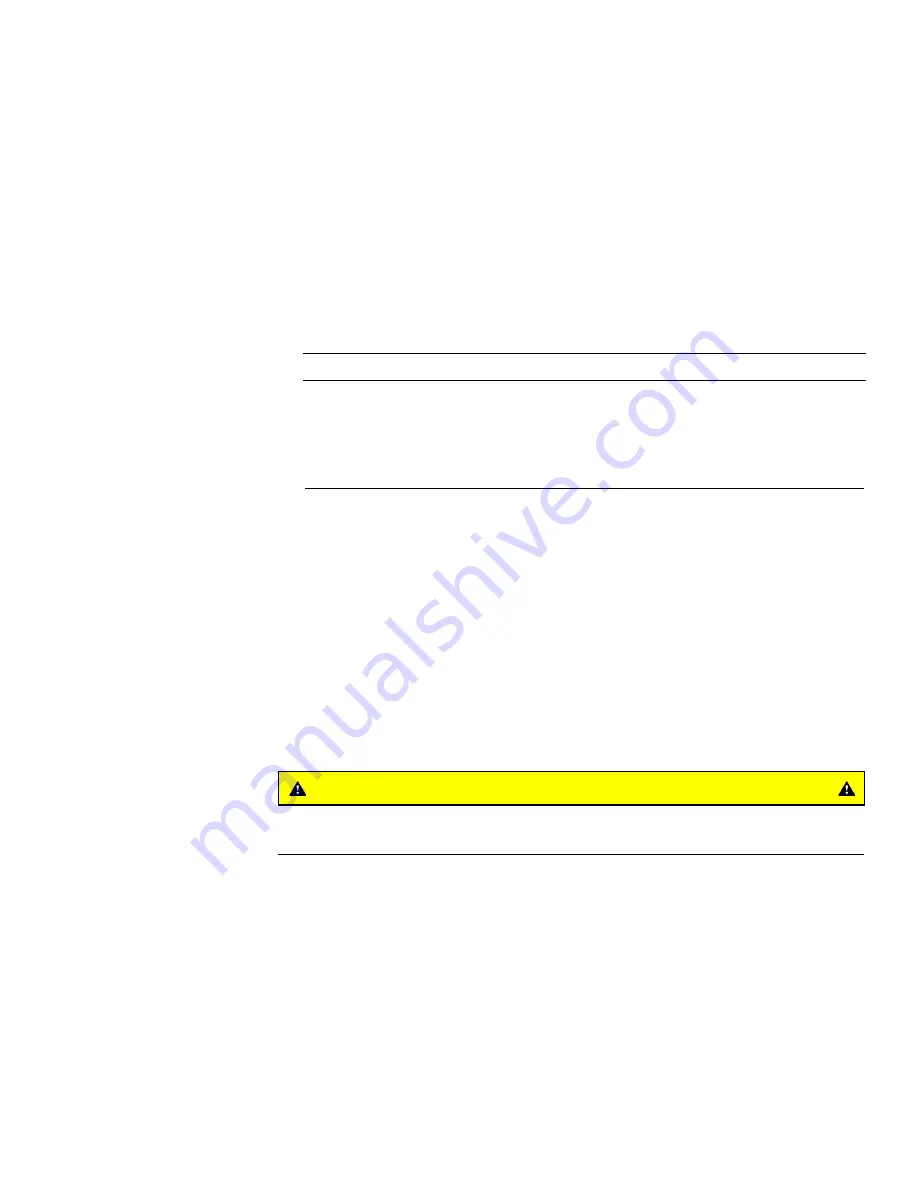
Cartridge Valve Service
Note:
For solenoid style cartridge valve coil testing information; refer to
Solenoid Valve Coils (page 6–59)
.
Read and adhere to the information provided in
Removing and Installing the Hydraulic System Components (page 5–52)
prior to
removing hydraulic system components.
1. Park the machine on a level surface. Lower the cutting unit, engage the
parking brake, stop the engine and remove the key from the key switch.
2. Ensure that the manifold is clean before you remove the cartridge valve
from the manifold.
3. Remove the cartridge valve:
A. For solenoid style valves, disconnect the wire harness connector and
remove the nut that secures the solenoid coil to the cartridge valve.
Carefully slide the coil off the valve.
IMPORTANT
Handle the cartridge valve carefully. Slight bending or distortion
of the stem tube can cause binding and malfunction. When
removing the cartridge valve from the manifold, ensure that the
deep well socket fully engages the valve base.
B. Use a deep socket wrench to remove the cartridge valve from the
manifold.
4. Record the correct location of the O-rings, the sealing rings, and the back-up
rings. Remove and discard the seal kit from the cartridge valve.
5. Visually inspect the manifold port and the cartridge valve:
A. Check for damaged threads on the cartridge valve and in the manifold
block.
B. If valve sealing surfaces appear pitted or damaged, the hydraulic system
may be overheating or there may be water in the system.
C. Contamination may cause valves to stick or hang up. Contamination
can become lodged in small valve orifices or seal areas causing valve
malfunction.
CAUTION
Use eye protection such as goggles when using compressed air.
Note:
Particles as fine as talcum powder can affect the operation of high
pressure hydraulic valves.
6. Clean the cartridge valve.
A. For non-solenoid operated valves: Submerge the valve in clean mineral
spirits to flush out contamination. If the valve design allows, use a
non–metallic probe to push the internal spool in and out 20 to 30 times
to flush out contamination. Clean and dry the cartridge valve with
compressed air.
B. For solenoid operated valves: Temporarily install the solenoid on the
cartridge valve and connect a 12 volt power source to the solenoid.
While energized, flush out any contamination with a nonflammable
aerosol brake cleaner. De-energize the solenoid. Repeat the flush
Groundsmaster
®
3200, 3300 and 3310
Page 5–93
Hydraulic System: Service and Repairs
19240SL Rev A
Summary of Contents for Groundmaster 31900
Page 4: ...Reader Comments Page 4 Groundsmaster 3200 3300 and 3310 19240SL Rev A...
Page 16: ...Safety Safety and Instructional Decals Page 1 8 Groundsmaster 3200 3300 and 3310 19240SL Rev A...
Page 86: ...Engine Service and Repairs Page 4 24 Groundsmaster 3200 3300 and 3310 19240SL Rev A...
Page 332: ...Operator Cab Service and Repairs Page 9 18 Groundsmaster 3200 3300 and 3310 19240SL Rev A...
Page 355: ......