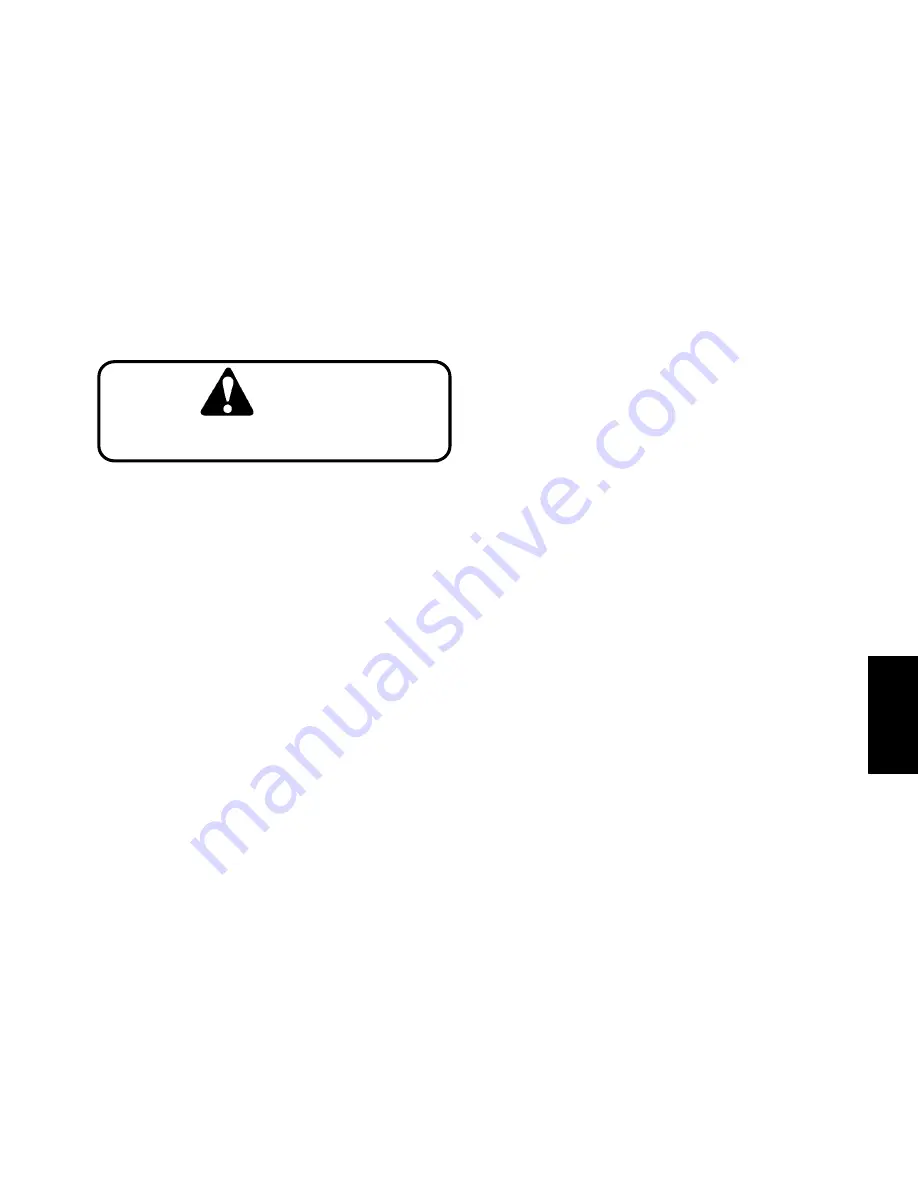
3. Remove hex socket head screws and washers from
the cover assembly and body assembly.
4. Separate cover assembly from body assembly by
tapping lightly on the drive shaft with a plastic hammer;
do not pry apart.
5. Remove load plate assembly from the drive shaft
and idler gear assemblies. Discard load plate assembly.
6. Remove seal ring from the body assembly. Discard
seal ring.
Inspection (Fig. 57)
1. Remove all nicks and burrs from all parts with an
emery cloth.
CAUTION
Use eye protection such as goggles when
using compressed air.
2. Clean all parts with solvent. Dry all parts with com-
pressed air.
3. Inspect drive shaft and idler gear assemblies.
A. Bushing points and seal areas should be free of
excessive excessive wear and rough surfaces.
B. Gear faces should be free of excessive scoring
and wear.
C. Gears should be free of excessive wear, nicks,
and, missing or broken teeth. Break sharp edges
with emery cloth.
D. Replace if either shaft is visibly bent.
4. Inspect cover and body assemblies.
A. Bearing needles should remain in cage and
move freely. If needle bearing (s) need replace-
ment, the entire assembly must be replaced.
B. Sealing faces and gear pockets should be free of
excessive scoring.
Assembly (Fig. 57)
1. Coat new seal ring lightly with petroleum jelly. Install
seal ring into matching groove on the body assembly.
2. Apply a thin coat of petroleum jelly to both gear
pockets of the cover assembly. Install dowel pins into
body assembly.
Note: Make sure idler gear is installed into the gear
pocket opposite the external drain port.
3. Dip idler gear and drive shaft assemblies into clean
hydraulic oil. Install both assemblies into the cover as-
sembly gear pockets. Make sure that both gears mesh.
4. Coat new load plate assembly lightly with petroleum
jelly. Install load plate assembly onto idler gear and drive
shaft assemblies. Make sure seal of assembly faces
away from the gear face.
5. Slide body assembly over the idler gear and drive
shaft assemblies onto the cover assembly. Make sure
that none of the parts become displaced. Install hex
socket head screws and washers. Hand tighten screws.
6. Rotate drive shaft to make sure gears mesh proper-
ly. Torque hex socket head screws from 190 to 210 in–lb
(219 to 242 kg–cm).
7. Install new spacer onto the drive shaft and into the
body assembly.
IMPORTANT: Use extreme care when installing the
shaft seal to prevent damage to the seal.
8. Install new shaft seal as follows:
A. Make sure that the bore of the body assembly is
clean and free of burrs and nicks which could dam-
age the seal.
B. Lubricate lips of the seal generously with clean
No. 2 multipurpose lithium base grease. Apply Loc-
tite gasket eliminator 515 or equivalent to the outer
edge of the metal case of the seal.
C. Make sure metal case of shaft seal faces away
from the motor. Use seal installer to press shaft seal
squarely into the bore.
9. Install retaining ring into bore of the body assembly.
10. Lubricate motor generously with clean hydraulic oil.
Hydraulic
System
Greensmaster 3200/3200–D
Page 5 – 73
Hydraulic System
Summary of Contents for 3200
Page 2: ...Greensmaster 3200 3200 D ...
Page 4: ...Greensmaster 3200 3200 D ...
Page 6: ...Greensmaster 3200 3200 D ...
Page 12: ...Safety Page 1 6 Greensmaster 3200 3200 D ...
Page 14: ...Equivalents and Conversions Product Records and Maintenance Page 2 2 Greensmaster 3200 3200 D ...
Page 17: ...Product Records and Maintenance Page 2 6 Greensmaster 3200 3200 D ...
Page 72: ...Perkins Diesel Engine Page 4 30 Greensmaster 3200 D ...
Page 113: ...Hydraulic System Greensmaster 3200 3200 D Page 5 41 Hydraulic System ...
Page 161: ...Hydraulic System Greensmaster 3200 3200 D Page 5 89 Hydraulic System ...
Page 173: ...Hydraulic System Greensmaster 3200 3200 D Page 5 101 Hydraulic System ...
Page 234: ...Wheels and Brakes Page 7 12 Greensmaster 3200 3200 D ...
Page 261: ...Cutting Units Greensmaster 3200 3200 D Page 8 27 Cutting Units ...
Page 273: ......
Page 274: ...Commercial Products FORM 96 900 SL E The Toro Company 1997 Printed in U S A ...