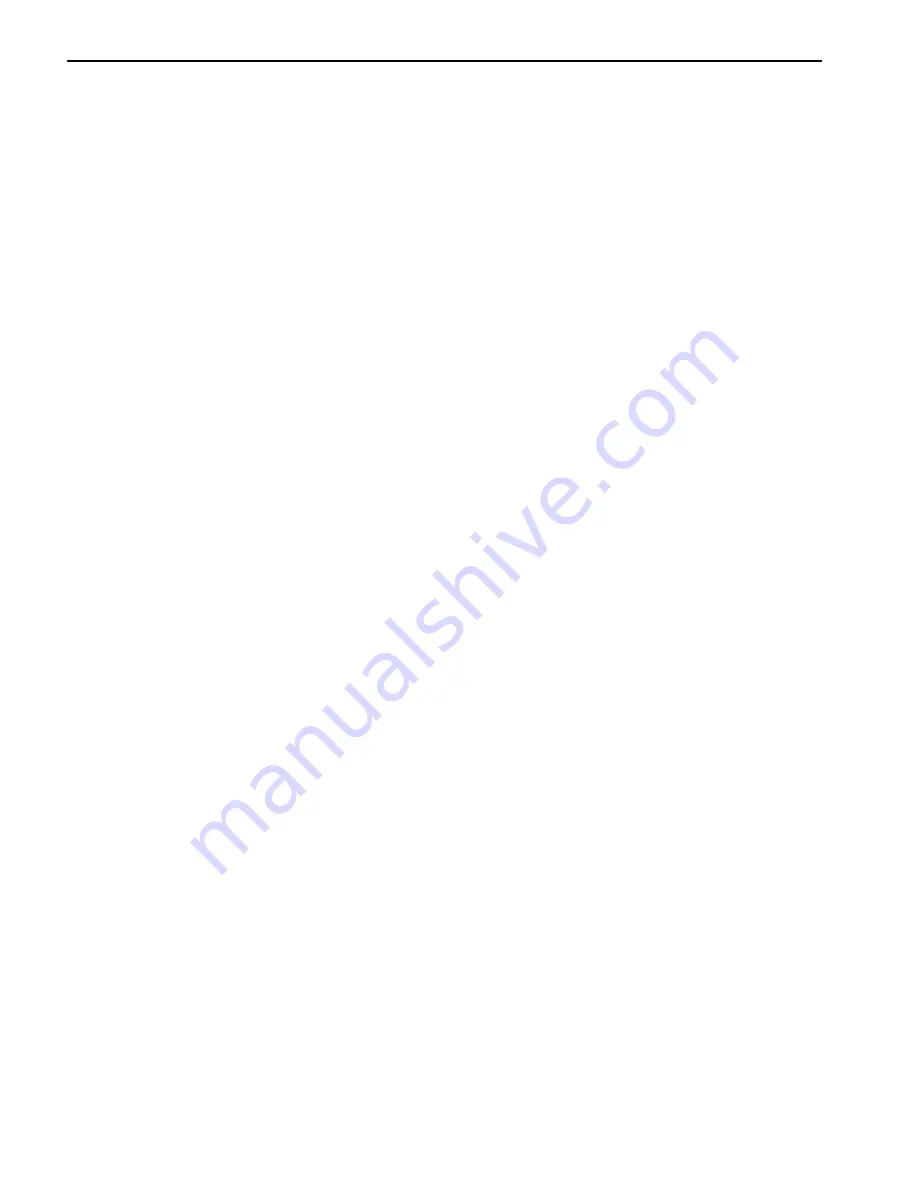
Raise and Lower Cutting Units
Raise
The gear pump (P2) is directly coupled to the hydrostat
through gear pump (P1). It supplies hydraulic pressure
for raising and lowering cutting units and maintaining
100 to 150 PSI (6.9 to 10.0 bar) to the low pressure side
of the traction circuit (charge pressure). The pump takes
its suction from the hydraulic reservoir.
During conditions of not lifting or lowering cutting units,
flow from the gear pump is by–passed through the steer-
ing control valve and solenoid valve (S2) directly to the
hydrostat and the charge relief valve(R4). Flow then re-
turns to the hydraulic reservoir.
When the cutting units are to be raised, solenoid valve
(S2) is energized and blocks flow directly to the hydros-
tat. Flow is directed to energized solenoid valve (S3),
which directs flow to de–energized solenoid valve (S4)
and the lift cylinders. Hydraulic pressure against the cyl-
inder pistons moves their shafts causing the cutting
units to raise. At the same time, the pistons push the hy-
draulic fluid out of the lift cylinders and back through so-
lenoid valves (S4 and S3) to the hydrostat. When the
solenoid valves de–energize, spring action returns the
valves to their original position and by–passes flow back
to the hydrostat stopping lift cylinder movement. The
cylinder position is locked in place since there is no com-
plete circuit of flow to and from the lift cylinders.
Lower
Circuit operation for lowering the lift cylinders is similar
to raising them. However, the solenoid valve (S3) re-
mains de–energized and in the down position and sole-
noid valve (S4) is energized and shifts down. Flow is
reversed to and from the lift cylinders, thus moving the
cutting units down.
When the cutting units are to be lowered, solenoid valve
(S2) is energized and blocks flow directly to the hydros-
tat. Flow is directed to de–energized solenoid valve
(S3), which directs flow to energized solenoid valve (S4)
and the lift cylinders. Hydraulic pressure against the cyl-
inder pistons moves their shafts causing the cutting
units to lower. At the same time, the pistons push the hy-
draulic fluid out of the lift cylinders and back through so-
lenoid valves (S4 and S3) to the hydrostat. Flow into the
flow control valve is slowed by the variable orifice to al-
low the rear cutting unit to lower after the front units.
When the solenoid valves de–energize, spring action
returns the valves to their original position and by–
passes flow back to the hydrostat stopping lift cylinder
movement.
Hydraulic System
Page 5 – 10
Greensmaster 3200/3200–D
Summary of Contents for 3200
Page 2: ...Greensmaster 3200 3200 D ...
Page 4: ...Greensmaster 3200 3200 D ...
Page 6: ...Greensmaster 3200 3200 D ...
Page 12: ...Safety Page 1 6 Greensmaster 3200 3200 D ...
Page 14: ...Equivalents and Conversions Product Records and Maintenance Page 2 2 Greensmaster 3200 3200 D ...
Page 17: ...Product Records and Maintenance Page 2 6 Greensmaster 3200 3200 D ...
Page 72: ...Perkins Diesel Engine Page 4 30 Greensmaster 3200 D ...
Page 113: ...Hydraulic System Greensmaster 3200 3200 D Page 5 41 Hydraulic System ...
Page 161: ...Hydraulic System Greensmaster 3200 3200 D Page 5 89 Hydraulic System ...
Page 173: ...Hydraulic System Greensmaster 3200 3200 D Page 5 101 Hydraulic System ...
Page 234: ...Wheels and Brakes Page 7 12 Greensmaster 3200 3200 D ...
Page 261: ...Cutting Units Greensmaster 3200 3200 D Page 8 27 Cutting Units ...
Page 273: ......
Page 274: ...Commercial Products FORM 96 900 SL E The Toro Company 1997 Printed in U S A ...