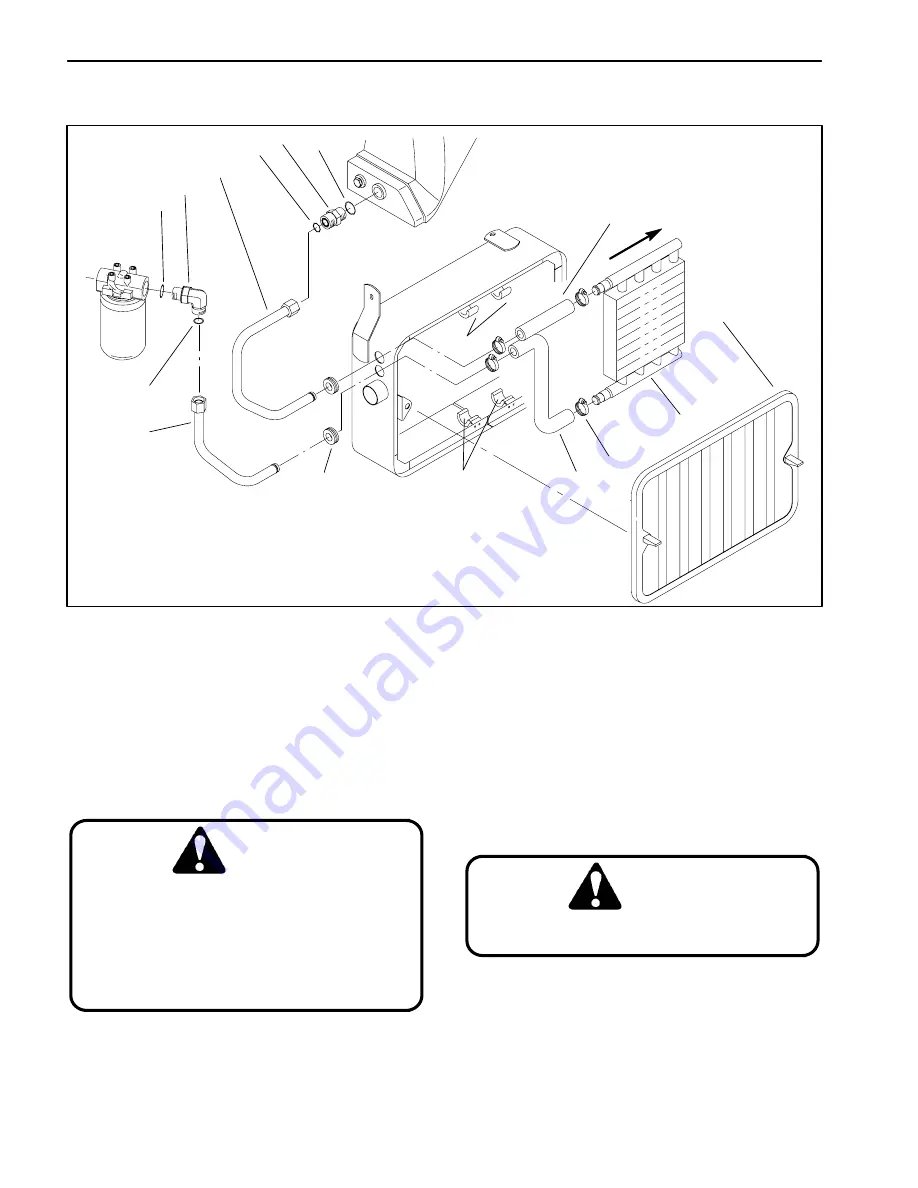
Oil Cooler
3
2
6
4
1
10
5
7
9
8
10
11
11
12
13
14
OIL FLOW
Figure 58
1. Oil
cooler
6. Tube
assembly
11. O–ring
2. Lower formed hose
7. Tube
assembly
12. Radiator screen
3. Upper formed hose
8. Hydraulic
fitting
13. Upper cooler bracket
4. Grommet
9. Hydraulic
fitting
14. Lower cooler bracket
5. Hose
clamp
10. O–ring
Removal (Fig. 58)
4. Lift oil cooler up from the cooler brackets. Remove
oil cooler from the formed hoses. Allow hoses and cooler
to drain into a suitable container.
5. To clean the oil cooler, back flush with cleaning sol-
vent. After the cooler is clean, make sure all solvent is
drained from the cooler.
CAUTION
Use eye protection such as goggles when
using compressed air.
6. Use compressed air in a direction opposite the oil
flow to dry the cooler.
7. Plug ends of the oil cooler. Clean exterior of the
cooler.
8. The oil cooler should be free of corrosion and exces-
sive pitting of tubes.
1. Before removing any parts from the hydraulic sys-
tem, park machine on a level surface, engage parking
brake, lower cutting units, and stop engine.
CAUTION
Operate all hydraulic controls to relieve sys-
tem pressure and avoid injury from pressur-
ized hydraulic oil. Controls must be oper-
ated with the ignition switch in RUN and the
when pressure has been relieved. Remove
key from the ignition switch.
engine OFF. Return ignition switch to OFF
2. Clamp upper and lower formed hoses to prevent
draining of the hydraulic system and tank.
3. Remove loosen hose clamps securing the formed
hoses to the oil cooler.
Hydraulic System
Page 5 – 74
Greensmaster 3200/3200–D
Summary of Contents for 3200
Page 2: ...Greensmaster 3200 3200 D ...
Page 4: ...Greensmaster 3200 3200 D ...
Page 6: ...Greensmaster 3200 3200 D ...
Page 12: ...Safety Page 1 6 Greensmaster 3200 3200 D ...
Page 14: ...Equivalents and Conversions Product Records and Maintenance Page 2 2 Greensmaster 3200 3200 D ...
Page 17: ...Product Records and Maintenance Page 2 6 Greensmaster 3200 3200 D ...
Page 72: ...Perkins Diesel Engine Page 4 30 Greensmaster 3200 D ...
Page 113: ...Hydraulic System Greensmaster 3200 3200 D Page 5 41 Hydraulic System ...
Page 161: ...Hydraulic System Greensmaster 3200 3200 D Page 5 89 Hydraulic System ...
Page 173: ...Hydraulic System Greensmaster 3200 3200 D Page 5 101 Hydraulic System ...
Page 234: ...Wheels and Brakes Page 7 12 Greensmaster 3200 3200 D ...
Page 261: ...Cutting Units Greensmaster 3200 3200 D Page 8 27 Cutting Units ...
Page 273: ......
Page 274: ...Commercial Products FORM 96 900 SL E The Toro Company 1997 Printed in U S A ...