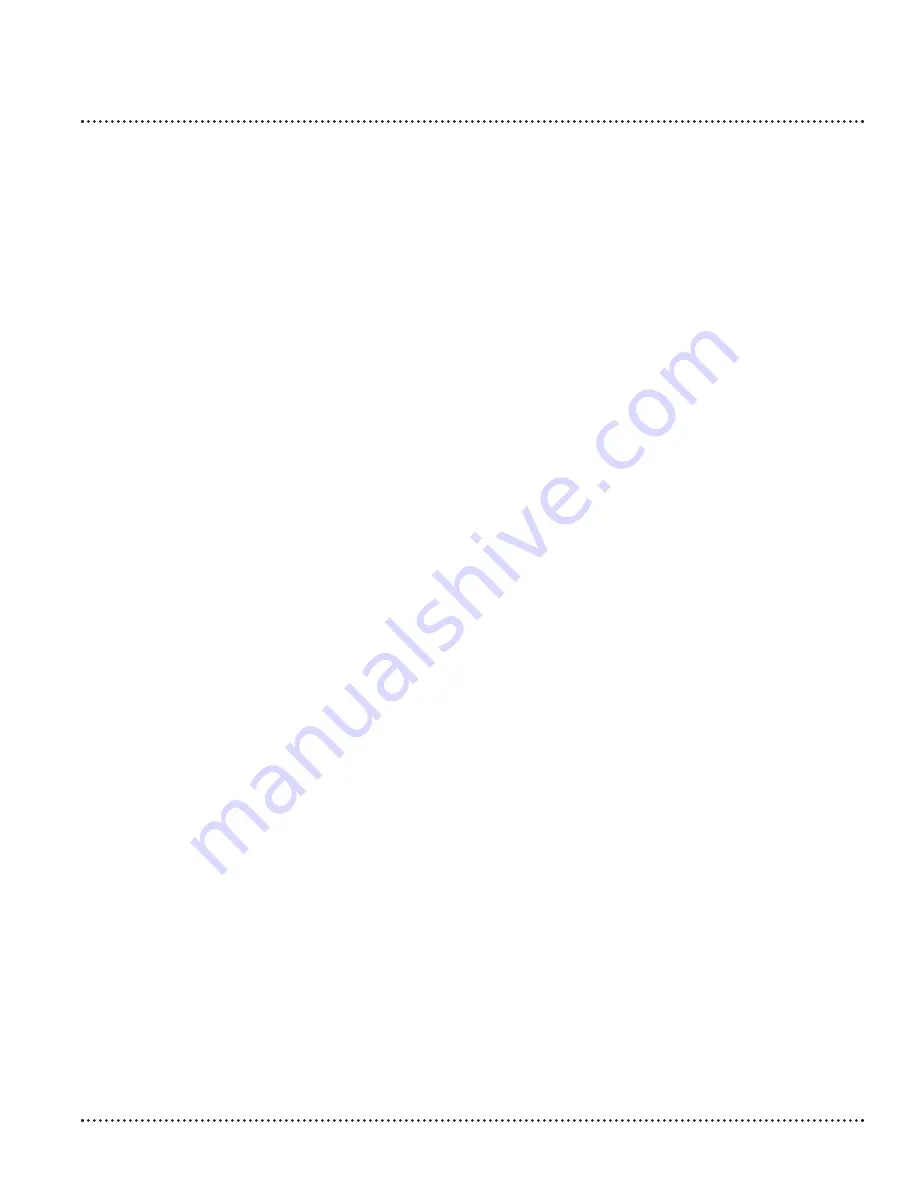
For Sales and Support, Contact Walker EMD • Toll-free: (800) 876-4444 • Tel: (203) 426-7700 • Fax: (203) 426-7800 • www.walkeremd.com
PC disable asserted (IS007)
- This bit flag is true if the disable
state is being forced by PC via serial communications.
PC step mode asserted (IS008)
- This bit flag is true if the PC
has set the controller in step mode for manual or auto-tuning.
Sequential End Program One Shot (IS009)
- Gives a one shot
when the sequential program executes an end of program
instruction.
Positive Motion Limit Reached (IS010) –
Bit flag is true when
the positive (cw) software travel limit has been reached.
Negative Motion Limit Reached (IS011) –
Bit flag is true
when the negative (ccw) software travel limit has been
reached.
Torque at Peak Limit (IS012)-
Bit flag is true when the drive
has reached the torque limit.
INDEXER CONTROL STATE FLAGS (ICS)
- This set of eight read
only bit flags can be read in the PLC in order to monitor the
status of the controller. Following is a list and description of
these bits.
Drive output enabled status (ICS001)
- This bit flag is true
when the controller is enabled and not faulted.
Cycle run status (ICS002)
- This bit flag is true when a
sequential program is executing, otherwise it is false.
Cycle pause status (ICS003)
- This bit flag is true when a
program cycle is in the “pause” state.
Jog 1 CW in process (ICS004)
- This bit flag is true when
using jog 1 in the CW direction.
Jog 1 CCW in process (ICS005)
- This bit flag is true when
using jog 1 in the CCW direction.
Jog 2 CW in process (ICS006)
- This bit flag is true when
using jog 2 in the CW direction.
Jog 2 CCW in process (ICS007)
- This bit flag is true when
using jog 2 in the CCW direction.
Auxiliary encoder following active (ICS008)
- This bit flag is
true when encoder following is true.
PC Debug PRG RUN (ICS009)
- User is running sequential
debug mode.
PC Debug PRG STOP (ICS010)
- User is running sequential
debug mode but sequential program is stopped.
PC Debug PRG JOG+ (ICS011)
- User is j from debug
mode.
12-39
P R O G R A M M I N G : 1 2