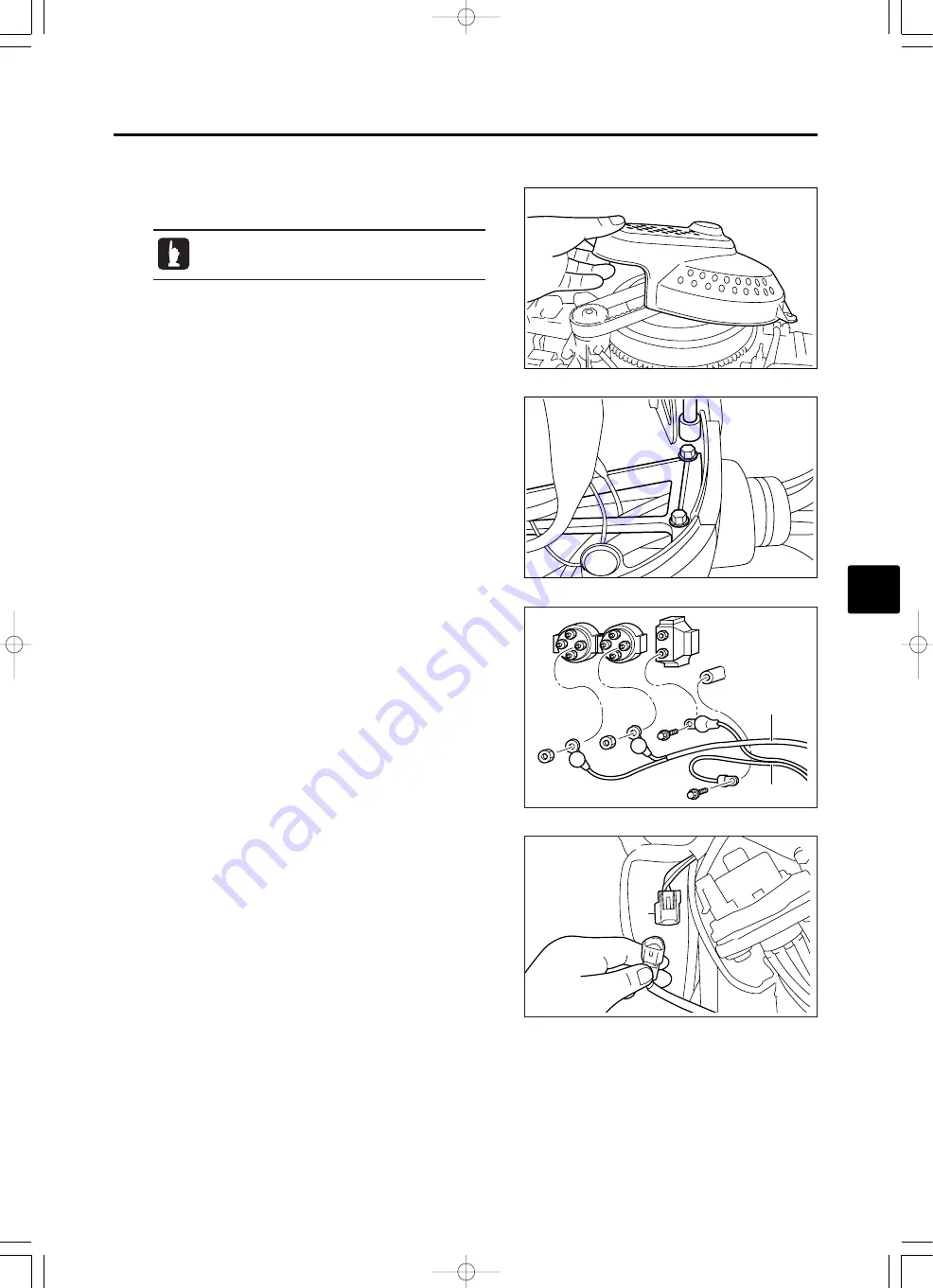
5
5-15
TLDI 115A 2007
3. Inspection Items
1) Removing Power Unit
1.
Remove ring gear cover.
2
1
3.
Remove bracket cover, and then, remove battery cables
1
and PTT cable
2
from solenoid switch and other parts.
3
4.
Disconnect connector
3
of PTT switch.
2.
Remove clamps that secure shift cable and remote control
cable from bottom cowl.
Disconnect battery cables from battery terminal.
MD115A̲ch05̲E̲2校̲070606.qxd 07.6.6 6:30 PM ページ 15