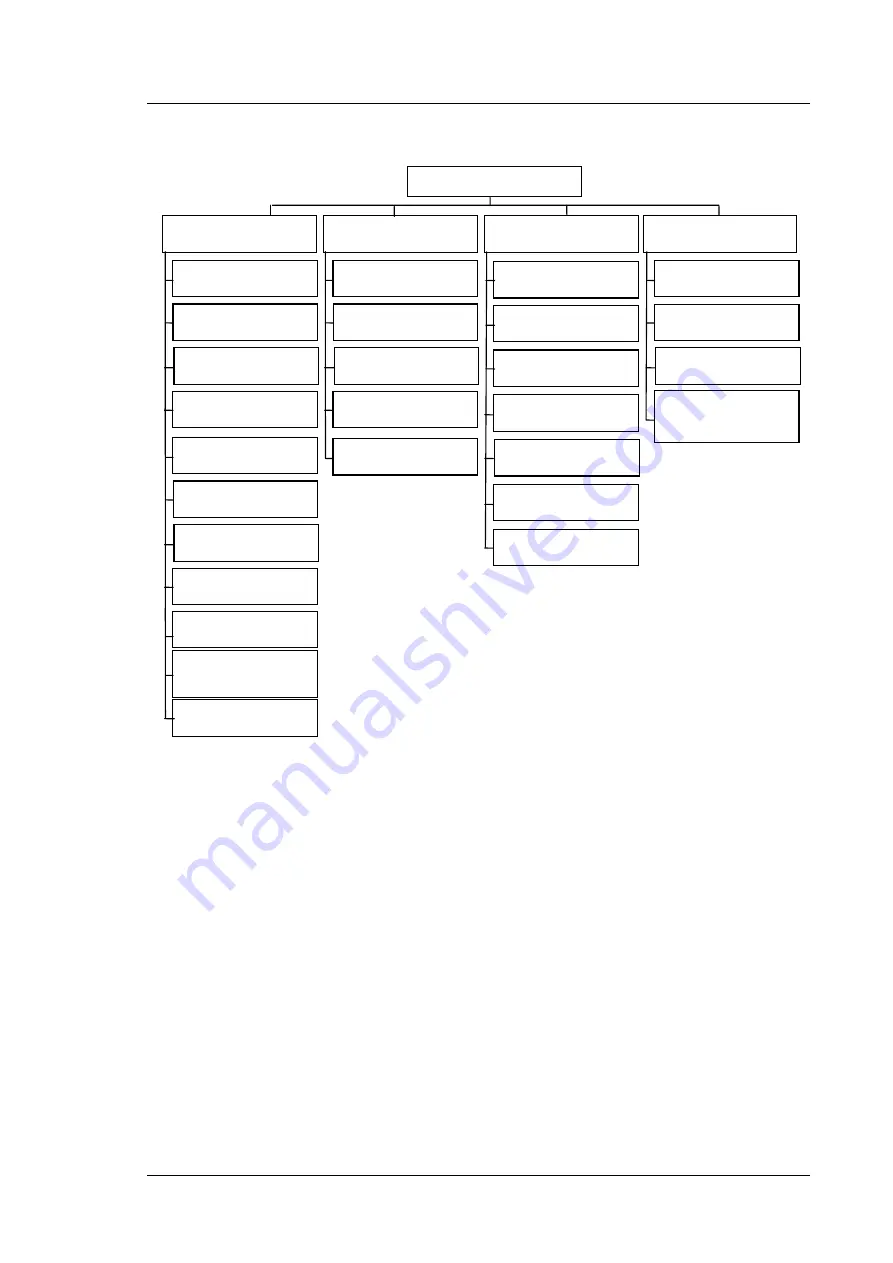
UltiMate 3000 Series:
NCS-3500RS and NCP-3200RS
Operating Instructions
Page
99
1. Control
2. Preferences
3. Diagnostics
Main
1. Self Test
2. Compression
3. Workload
4. Model
6. Bootloader Version
1. Flow
2. Flow Rate
3. %A
4. %B
4. Configuration
1. Display & Soft Keys
2. Leak Sensor Mode
3. Pressure Unit
5. %C
6. Max. Pressure
7. Min. Pressure
8. Purge
9. Change Pump Pistons
10. Catch Right Valve
Head
11. Catch Left Valve Head
1. Degasser
2. Purge Time
3. Purge Flow
4. Flow Acceleration
5. Flow Deceleration
5. Firmware Version
7. Serial Number
4. Reset to Factory
Defaults
Fig. 51: Loading pump menus
Summary of Contents for Dionex UltiMate 3000 Series
Page 2: ...UltiMate 3000 Series NCS 3500RS and NCP 3200RS Operating Instructions ...
Page 8: ...UltiMate 3000 Series NCS 3500RS and NCP 3200RS Page vi Operating Instructions ...
Page 24: ...UltiMate 3000 Series NCS 3500RS and NCP 3200RS Page 16 Operating Instructions ...
Page 62: ...UltiMate 3000 Series NCS 3500RS and NCP 3200RS Page 54 Operating Instructions ...
Page 92: ...UltiMate 3000 Series NCS 3500RS and NCP 3200RS Page 84 Operating Instructions ...
Page 246: ...UltiMate 3000 Series NCS 3500RS and NCP 3200RS Page 238 Operating Instructions ...
Page 262: ...UltiMate 3000 Series NCS 3500RS and NCP 3200RS Page 254 Operating Instructions ...