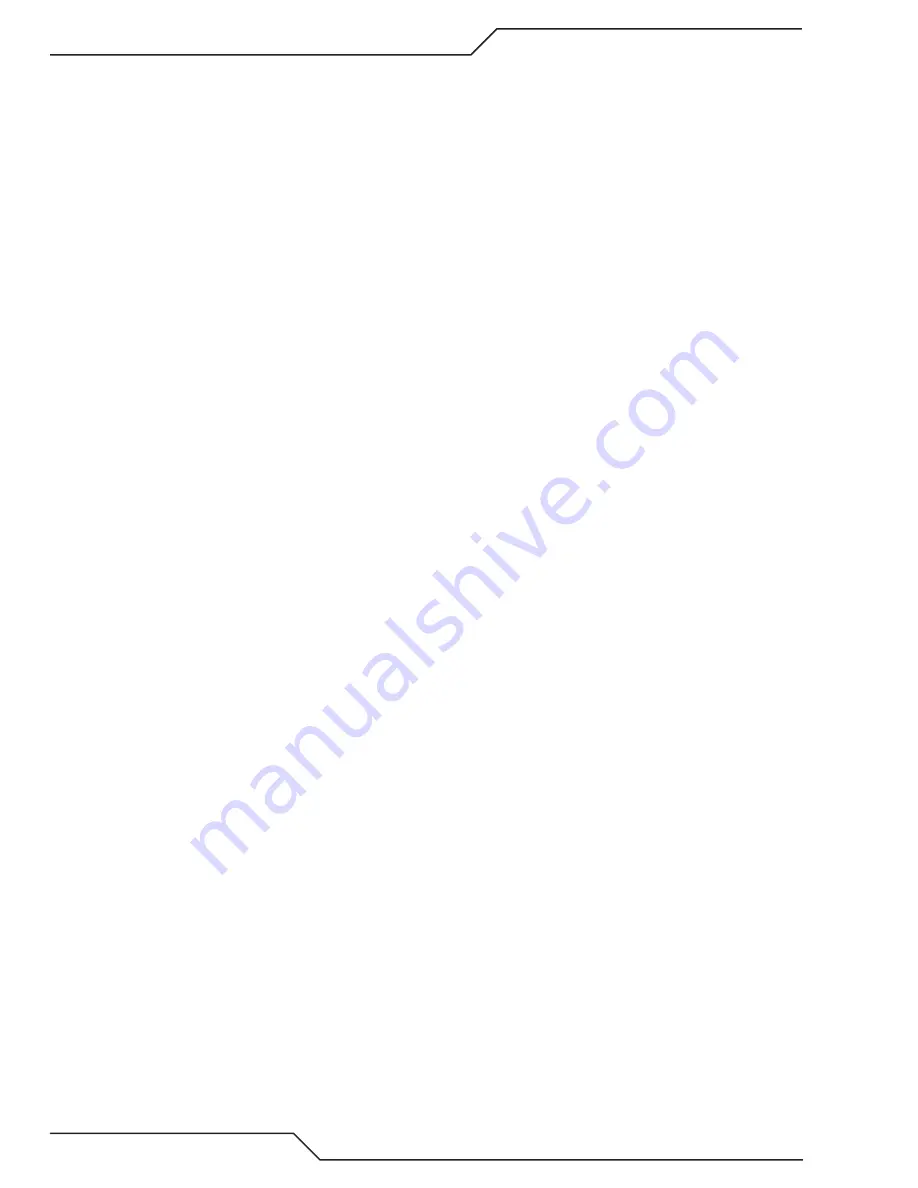
ULTRA-CUT 400 XT
A-82
APPENDIX
Manual 0-5275
When the 1Torch trigger is pressed an interlock circuit first determines if the 1Torch consumables are in place
and making proper contact as required to start a pilot.
1. -15V (J85-3) is applied to the 1Torch electrode via K201 NC contacts and returns from the tip on J85-1 where
measurement is taken by U13A on the Relay Board. The signal “/Pressure OK 1Torch” on pin 6 of the 40
pin ribbon cable (between Relay and I/O boards (J4, J23)) is used for both the interlock and for confirming
gas pressure. When this signal is pulled low during the parts continuity test, it indicates it’s OK to energize
the 1Torch. There is an LED, D35, called T-E CONTACT that when on, indicates this test is satisfied. No
continuity will set the fault code 702.
2. Once it is confirmed the consumables are in place, K201 and W5 are energized and W5’s normally closed
auxiliary contact (W5 AUX) opens de-energizing W4 isolating the automation torch tip from the 1Torch tip.
If for some reason K201 does not energize or if the PS2 pressure switch is shorted closed, it will set fault 703.
3. Now the 1Torch gas solenoid is turned on and gas should flow causing the 1Torch start cartridge to move
away from the tip. At the same time the inverter is energized to put out open circuit voltage. If the start
cartridge has separated from the tip the XT supply will detect the open circuit voltage between tip and
electrode. If there is not enough air pressure, at least 35 PSI, the Pressure fault 704 will be set. If pressure is
above 35 PSI and the cartridge does not separate then the Start Cartridge fault 705 is set.
4. Assuming there is enough gas pressure (should be 70-85 PSI) and the start cartridge works properly, gas is
then shut off, the parts come together and pilot current flows through them, gas is turned on again and the
parts separate drawing an arc between them which is blown out of the tip by the gas flow.
Interlock measurements during XT Automation torch operation:
1. Regardless of whether a 1Torch is plugged into the ATC, -15 V is applied via K201 to the 1Torch electrode
circuit (ATC negative terminal) as previously explained. If W5, which should be open, has any of its 3 nega-
tive contacts closed (welded or stuck on) the -15V will be measured by U13B giving the signal “Contactor
Fault 1Torch”. If the contactor fault is not detected it’s Ok to energize the automation torch.
2. If a 1Torch is plugged in and it parts are in place making contact, the -15V will also be seen on the tip circuit
and if the W5 Pilot (tip) contact is closed (welded or stuck on), U13D will detect the -15V and give the signal
“Contactor Fault 1Torch”. “Contactor Fault 1Torch” sets the 701 fault code. If contactor fault is not detected
it’s OK to energize the automation torch. There is a green LED, D40, on the Relay board that is on when the
circuit is satisfied, not in fault condition.
Troubleshooting the 1Torch module.
First read the descriptions above. This guide assumes you have a copy of the XT 1Torch module & Intercon-
nections Schematic 42X1366. The 1Torch Module is mounted in the XT front panel with screws that accept
Torx T25 driver or 8 mm socket. If the procedure requires you to remove it, the wires are long enough to allow
removing the module far enough from the panel to also remove the cover. You will have to support the module
with something while working on it.
Removing and opening the 1Torch module.
Should troubleshooting/repair require accessing the inside of the 1Torch module this is what is required. First
remove the right side panels and make sure the connector J86 on the back of module is plugged in. There are
6 screws in the module’s front panel, 4 attach it to the panel and 2 hold the cover, remove them all. Pull the
module out of the front panel until you can access its cover screws, 2 on each side and 2 in the rear. The harness
and cables remain connected. The rear of the cover is slotted so you only have to loosen those screws. You will
need to support the module while doing this.
Summary of Contents for Ultra-Cut 300 XT
Page 6: ...This Page Intentionally Blank...
Page 10: ...TABLE OF CONTENTS This Page Intentionally Blank...
Page 15: ...ULTRA CUT 400 XT Manual 0 5275 SAFETY INSTRUCTIONS 1 5 This Page Intentionally Blank...
Page 88: ...ULTRA CUT 400 XT OPERATION Manual 0 5275 This Page Intentionally Blank...
Page 106: ...ULTRA CUT 400 XT REPLACEMENT PARTS Manual 0 5275 This Page Intentionally Blank...
Page 114: ...ULTRA CUT 400 XT TORCH INFORMATION Manual 0 5275 This Page Intentionally Blank...
Page 139: ...ULTRA CUT 400 XT Manual 0 5275 APPENDIX A 25 Display PCB Test Points TP1GND TP2 5VDC TP3 24VDC...
Page 148: ...ULTRA CUT 400 XT APPENDIX Manual 0 5275 APPENDIX 17 Cap Bias Bottom PCB Layout Art A 11685_AB...
Page 150: ...ULTRA CUT 400 XT APPENDIX Manual 0 5275 APPENDIX 19 Suppressor PCB Layout Art A 11684_AB...
Page 201: ...ULTRA CUT 400 XT Manual 0 5275 APPENDIX A 87 This Page Intentionally Blank...
Page 213: ......