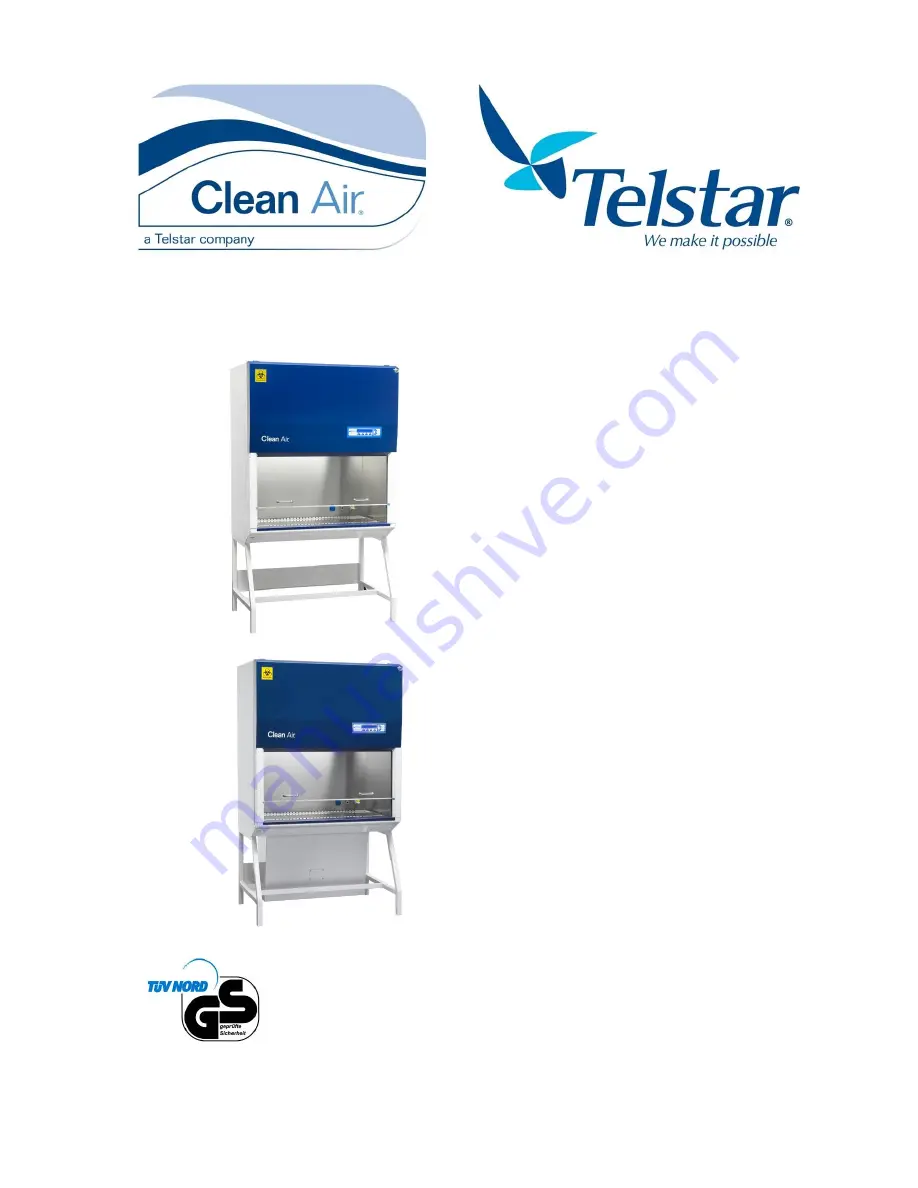
EF
EF/B
User manual
English
Version
10.0
(valid for software V4.9 and higher)
Series EuroFlow,
Type EF
Biological Safety Cabinet Class II
&
Type EF/B
Biological Safety Cabinet Class II
Types:
EF 4
EF 5
EF 6
EF/B 4
EF/B 6
Offers protection for personnel,
environment and product.
Before using the safety cabinet, please read
this manual carefully. The required
instructions have to be carried out first.
Clean Air Techniek B.V.
Kuipersweg 37
3449 JA Woerden
Nederland
t: +31 (0) 348 41 11 14
f: +31 (0) 348 42 26 84
e: [email protected]
i: www.cleanair.eu