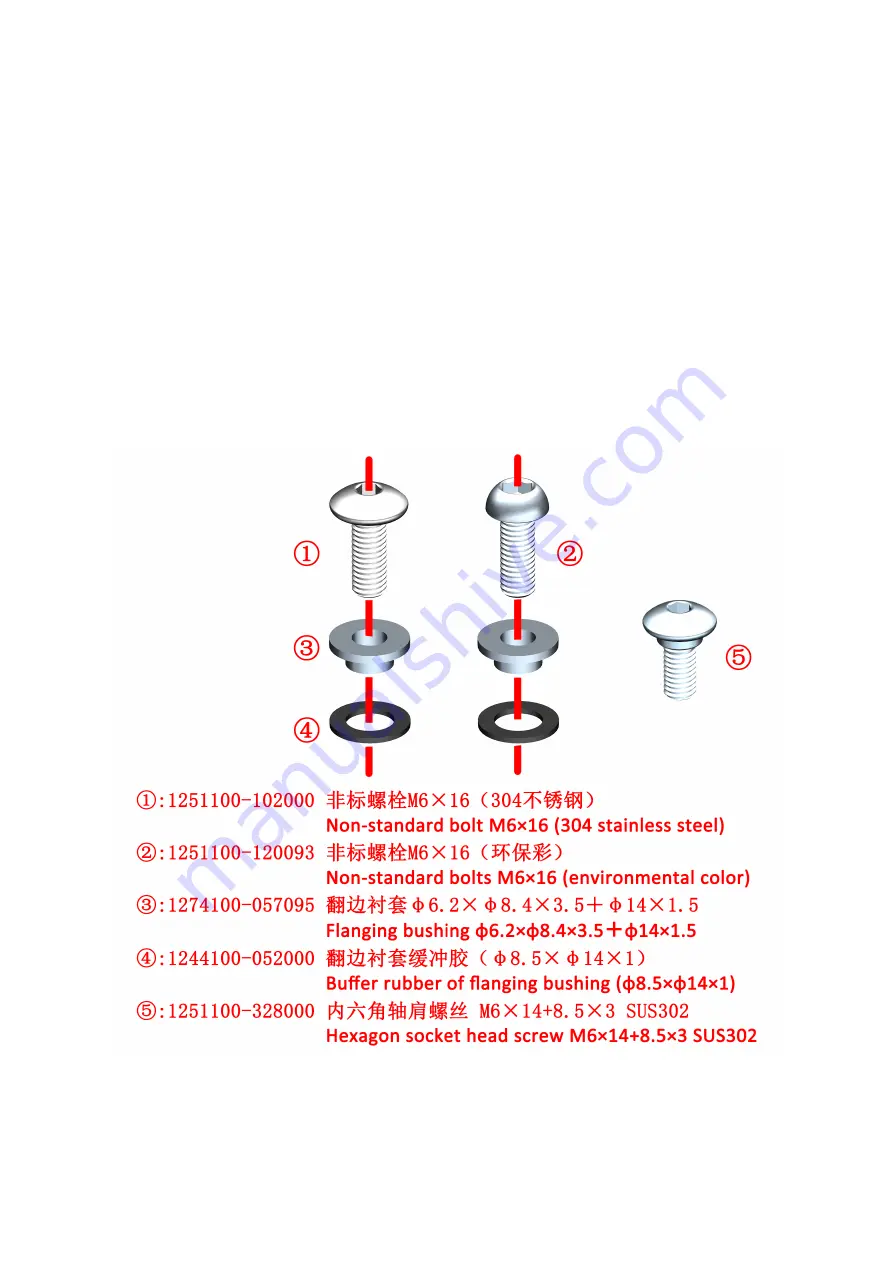
12 / 188
1. Vehicle information
Know Before Service
1. Use good quality tools, or special tools and fixtures designed by our company. The use of inferior tools may cause damage to
parts, peeling of plating, improper assembly, etc.
2. The O-rings, paper gaskets, copper gaskets, and component sealing rings used for sealing must be replaced before assembling.
3. Fasteners with torque requirements need to use a torque wrench to check the torque; if the torque is not required, refer to
the general torque value recommended by general fasteners.
4. Clean up before assembly; after assembly, check whether the assembly is correct and in place.
5. The vehicle should be parked balanced and pay attention to safety during disassembly and assembly. Including but not limited
to the use of electric tools, hand tools, pneumatic tools, hydraulic tools, handling; prevent contact with skin, eyes, burns, etc.
6. The replaced oils, liquids, batteries, etc. must be recycled and handed over to qualified institutions for disposal; it is forbidden
to dump them at will to pollute the environment or water sources.
7. Swallowing or inhaling coolant, brake fluid, etc. will cause certain harm to the human body. Any exposed skin such as hands
and face should be cleaned thoroughly after each addition. If swallowed by mistake, immediately contact the poison control
center or hospital; if inhaled, please immediately go to a ventilated environment. If it accidentally splashes into the eyes,
immediately rinse the eyes with a large amount of running water and seek medical advice or consultation in time. Keep away
from children and pets.
8 M310 and M125 vehicles produced before mid-August 2022 have the structure of M6×16 bolts + flanging b flanging
bushing buffer rubber, which can be replaced by M6×14 shoulder socket head cap bolts. Similar places in subsequent chapters
of this manual will not be repeated.
Only part of the basic requirements for matters needing attention, prevention of accidental injury, etc. can be listed; it is not
possible to list all situations in detail. Be vigilant during disassembly and assembly to prevent accidents.
Summary of Contents for Zontes ZT125-M 2022
Page 1: ...1 188 ZT125 310T M Maintenance Manual 2022 09 14 ...
Page 91: ...91 188 l So far the adjustment operation of the valve clearance is completed ...
Page 115: ...115 188 Electrical schematic diagram of EFI system ...
Page 156: ...156 188 Exploded view of front fork components M125 310 Directional exploded view ...
Page 173: ...173 188 ...