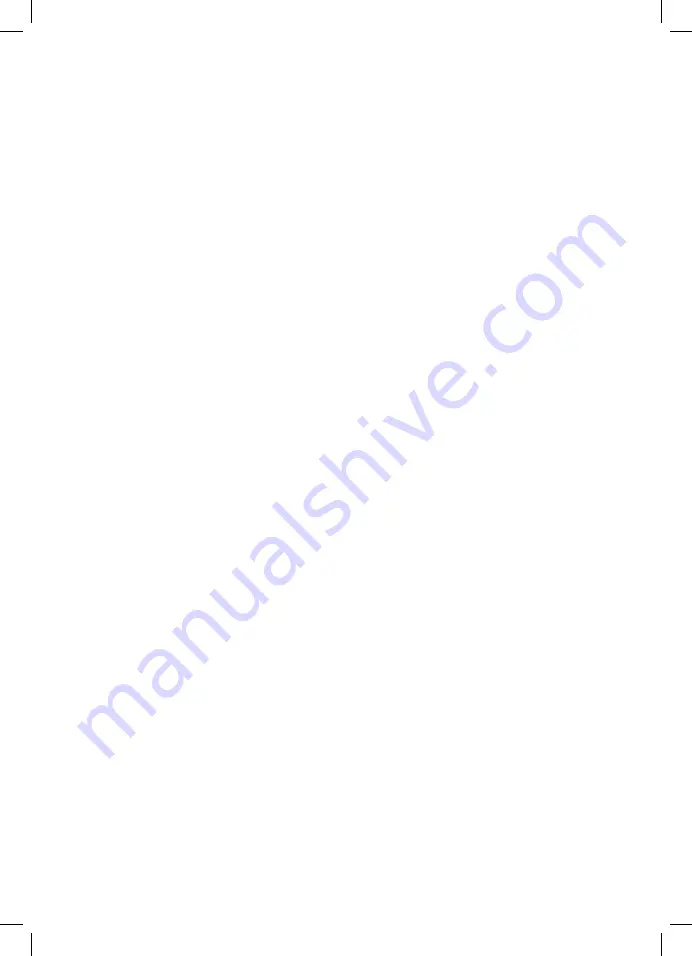
sparks.
- Reassemble sealed enclosures accurately. If
seals are worn, replace them.
- Check safety equipment before putting into
service.
REPAIR
- Portable equipment shall be repaired outside or
in a workshop specially equipped for servicing
units with flammable refrigerants.
- Ensure sufficient ventilation at the repair place.
- Be aware that malfunction of the equipment
may be caused by refrigerant loss and a refrig-
erant leak is possible.
- Discharge capacitors in a way that won’t cause
any spark.
- When brazing is required, the following proce-
dures shall be carried out in the right order:
-Remove the refrigerant. If the recovery is not
required by national regulations, drain
-the refrigerant to the outside. Take care that the
drained refrigerant will not cause any danger. In
doubt, one person should guard the outlet. Take
special care that drained refrigerant will not float
back into the building.
-Evacuate the refrigerant circuit.
-Purge the refrigerant circuit with nitrogen for 5
min.
-Evacuate again.
-Remove parts to be replaced by cutting, not by
flame.
-Purge the braze point with nitrogen during the
brazing procedure.
-Carry out a leak test before charging with
refrigerant.
- Reassemble sealed enclosures accurately. If
seals are worn, replace them.
- Check safety equipment before putting into
service.
DECOMMISSIONING
- If the safety is affected when the equipment
is putted out of service, the refrigerant charge
shall be removed before decommissioning.
- Ensure sufficient ventilation at the equipment
location.
- Be aware that malfunction of the equipment
may be caused by refrigerant loss and a refrig-
erant leak is possible.
- Discharge capacitors in a way that won’t cause
any spark.
- Remove the refrigerant. If the recovery is not
required by national regulations, drain the
refrigerant to the outside. Take care that the
drained refrigerant will not cause any danger. In
doubt, one person should guard the outlet. Take
special care that drained refrigerant will not float
back into the building.
- Evacuate the refrigerant circuit.
- Purge the refrigerant circuit with nitrogen for 5 min.
- Evacuate again.
- Fill with nitrogen up to atmospheric pressure.
- Put a label on the equipment that the refrigerant
is removed.
DISPOSAL
- Ensure sufficient ventilation at the working
place.
- Remove the refrigerant. If the recovery is not
required by national regulations, drain the
refrigerant to the outside. Take care that the
drained refrigerant will not cause any danger. In
doubt, one person should guard the outlet. Take
special care that drained refrigerant will not float
back into the building.
- Evacuate the refrigerant circuit.
- Purge the refrigerant circuit with nitrogen for 5
min.
- Evacuate again.
- Cut out the compressor and drain the oil.
TRANSPORTATION, MARKING AND
STORAGE FOR UNITS THAT EMPLOY
FLAMMABLE REFRIGERANTS
TRANSPORT OF EQUIPMENT CONTAINING
FLAMMABLE REFRIGERANTS
- Attention is drawn to the fact that additional
transportation regulations may exist with re-
spect to equipment containing flammable gas.
The maximum number of pieces of equipment
or the configuration of the equipment, permitted
to be transported together will be determined by
the applicable transport regulations.
MARKING OF EQUIPMENT USING SIGNS
- Signs for similar appliances used in a work area
generally are addressed by local regulations
and give the minimum requirements for the
provision of safety and/or health signs for a
work location.
- All required signs are to be maintained and em-
ployers should ensure that employees receive
suitable and sufficient instruction and training
on the meaning of appropriate safety signs and
the actions that need to be taken in connection
with these signs.
- The effectiveness of signs should not be dimin-
Summary of Contents for COLD DESIGN
Page 2: ...1 2 3 4 5 6 7 8 9 10 11 12 13 14 15 16 24...
Page 4: ...Fig 1 Fig 2 Fig 3 Fig 4 Fig 5...
Page 5: ...Fig 6 Fig 8 Fig 9...
Page 99: ...on off A pH 2...
Page 100: ...7 35 C 44 95 F 17 C 62 F 3 E1 E2...
Page 101: ...R290 CO2...
Page 102: ......
Page 103: ...LFL 25 OFN OFN OFN OFN OFN...
Page 104: ...a b c d e f g h 80 i j k...
Page 105: ...GG 2 GG 4 GG 5 IEC 60079 15 2010...
Page 106: ...5 5 5...
Page 107: ......
Page 110: ...A pH 2...
Page 111: ...7 35 C 44 95 C 17 C 62 F 3 E1 E2...
Page 112: ...R290 CO 2...
Page 113: ......
Page 114: ...LFL 25 OFN OFN OFN OFN OFN...
Page 115: ...a b c d e f g h 80 i j k...
Page 116: ...GG 2 GG 4 GG 5 IEC 60079 15 2010...
Page 117: ...5 5 5...
Page 118: ......
Page 131: ...on off A pH 2...
Page 132: ...7 35 C 44 95 F 17 C 62 F 3 E1 Pantallas E2...
Page 133: ...R290 CO2...
Page 134: ......
Page 135: ...LFL 25 OFN OFN OFN 0 OFN OFN...
Page 136: ...a b c d e f g h 80 i j k...
Page 137: ...GG 2 GG 4 GG 5 IEC 60079 15 2010...
Page 138: ...5 5 5...
Page 139: ......
Page 140: ...5 5 5...
Page 141: ...2 GG 4 GG 5 GG 0102 51 97006 CEI...
Page 142: ...LFL 52 NFO NFO NFO NFO NFO a b c d e f g 08 h i j k...
Page 143: ...EU 03 4102 EU 53 4102 EC 521 9002 UE 56 1102 092R...
Page 144: ...2 53 7 59 44 71 26 3 1E 2E...
Page 152: ...Avda Barcelona s n 25790 Oliana Spain Rev 10 12 20...
Page 153: ...COLD DESIGN TEMP DESIGN...
Page 190: ...EL TAURUS ALPATEC 11 m2 R290 220 R290 R290...
Page 191: ...EL 8 20 cm 20 cm T 3 15A 250VAC 10...
Page 192: ...EL 30 mA o...
Page 194: ...PYCCK RU TAURUS ALPATEC 11 2 R290 220 R290 R290...
Page 195: ...RU 8 20 20 T 3 15A 250VAC...
Page 196: ...RU 10 30 H...
Page 197: ...RU WEEE 2014 35 EU 2014 30 EU 2011 65 EU 2009 125 EC...
Page 203: ...BG TAURUS ALPATEC 11 m2 R290 220 R290 R290...
Page 204: ...BG 8 20 20 T 3 15A 250VAC...
Page 205: ...BG 10 c a pa o a a e c po c a epe c 30 mA...
Page 206: ...BG U 2014 35 EU 2014 30 EU 2011 65 U 2009 125 EC...
Page 209: ...AR WEEE...
Page 210: ...AR 8 20 20 T 3 15A 250VAC 10 30...
Page 211: ...AR TAURUS ALPATEC 2 11 R290 220 R290 R290...
Page 212: ...Ver I 1 12 20 A5...