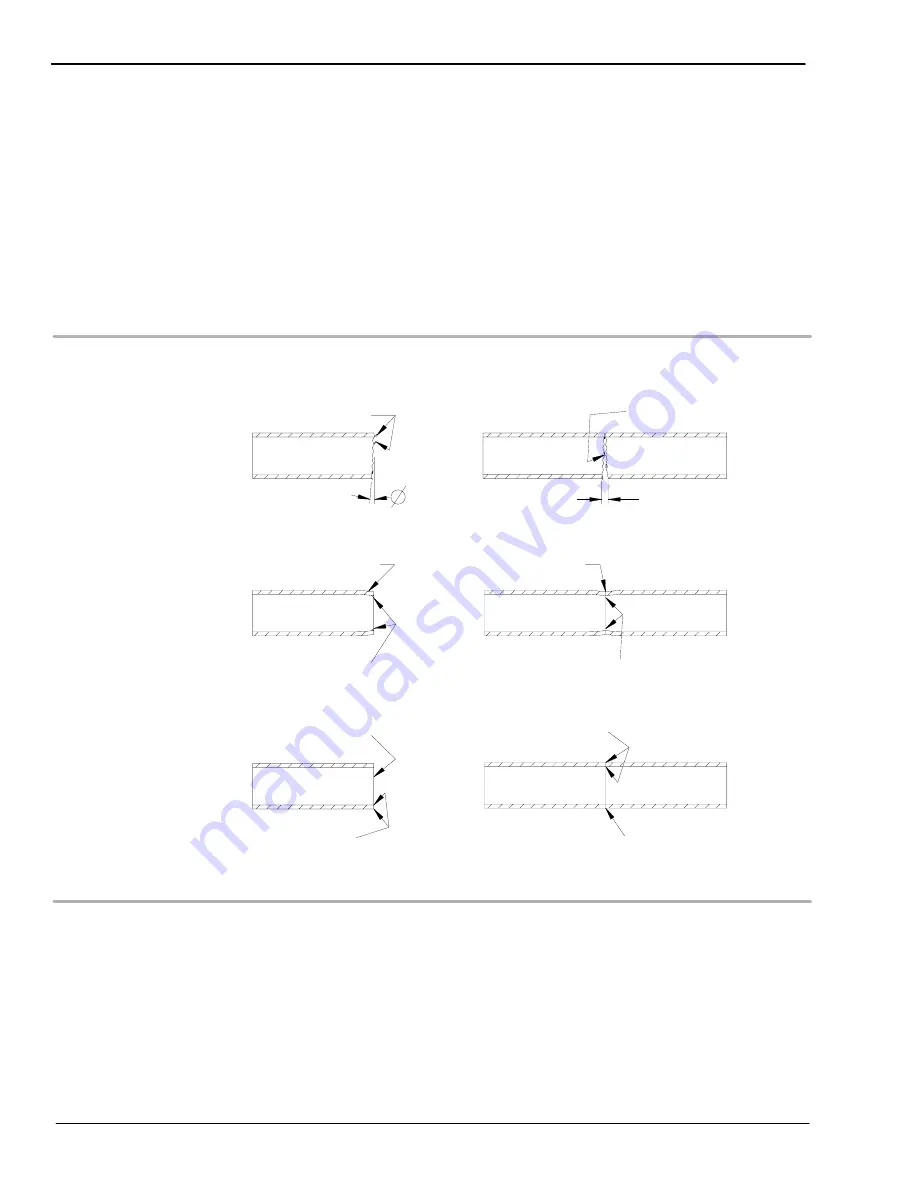
Operation
CWS
−
D100
−
B Welding System
2005 Swagelok Company, All rights reserved
September 2005
3-28
4.
Restore power to the SWS by turning the
circuit breaker on.
5.
Press
STOP/RESET
to return the rotor to the
home position and visually inspect the
rotor smooth rotation.
Preparing the Work
Refer to Figure 3-20. Prepare the tube pieces to be welded.
Figure 3-20 Tube Preparation
Method
Result
Hack Saw Cut
Burrs
Gap
Burrs in
Flow Path
Tube Cutter
End Roller in by Cutter
Burrs
Reduced Flow Area
Irregular Wall
Tube Facing Tool
Square Corners
Face Perpendicular
No Gaps
Smooth Transition
Blade and Roller
at Wall Faces
to Axis
Thickness
Tubing must be square and burr-free to ensure
repeatable, high-quality autogenous fusion welds. Cut
the tubing to length with a hacksaw or tube cutter. Face
the tube ends with a lathe or a portable facing tool.
Deburr the ends, making sure that both the inside and
outside diameters are square and burr-free. Clean the
tube ends using an appropriate solvent.